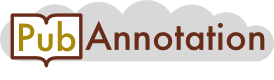
PMC:7143804 / 21957-25694
Annnotations
LitCovid-PubTator
{"project":"LitCovid-PubTator","denotations":[{"id":"145","span":{"begin":195,"end":204},"obj":"Chemical"},{"id":"146","span":{"begin":249,"end":267},"obj":"Chemical"},{"id":"147","span":{"begin":269,"end":279},"obj":"Chemical"},{"id":"148","span":{"begin":325,"end":331},"obj":"Chemical"},{"id":"149","span":{"begin":579,"end":589},"obj":"Chemical"},{"id":"150","span":{"begin":1501,"end":1512},"obj":"Chemical"},{"id":"151","span":{"begin":733,"end":747},"obj":"Disease"},{"id":"154","span":{"begin":1802,"end":1813},"obj":"Chemical"},{"id":"155","span":{"begin":2099,"end":2110},"obj":"Chemical"},{"id":"164","span":{"begin":2433,"end":2438},"obj":"Chemical"},{"id":"165","span":{"begin":2505,"end":2510},"obj":"Chemical"},{"id":"166","span":{"begin":2746,"end":2748},"obj":"Chemical"},{"id":"167","span":{"begin":2752,"end":2754},"obj":"Chemical"},{"id":"168","span":{"begin":3297,"end":3302},"obj":"Chemical"},{"id":"169","span":{"begin":3353,"end":3358},"obj":"Chemical"},{"id":"170","span":{"begin":2459,"end":2467},"obj":"Disease"},{"id":"171","span":{"begin":3554,"end":3563},"obj":"CellLine"}],"attributes":[{"id":"A146","pred":"tao:has_database_id","subj":"146","obj":"MESH:D006844"},{"id":"A147","pred":"tao:has_database_id","subj":"147","obj":"MESH:C046060"},{"id":"A148","pred":"tao:has_database_id","subj":"148","obj":"MESH:C036216"},{"id":"A149","pred":"tao:has_database_id","subj":"149","obj":"MESH:C046060"},{"id":"A150","pred":"tao:has_database_id","subj":"150","obj":"MESH:C506365"},{"id":"A151","pred":"tao:has_database_id","subj":"151","obj":"MESH:D006333"},{"id":"A154","pred":"tao:has_database_id","subj":"154","obj":"MESH:C506365"},{"id":"A155","pred":"tao:has_database_id","subj":"155","obj":"MESH:C506365"},{"id":"A164","pred":"tao:has_database_id","subj":"164","obj":"MESH:D008670"},{"id":"A165","pred":"tao:has_database_id","subj":"165","obj":"MESH:D008670"},{"id":"A166","pred":"tao:has_database_id","subj":"166","obj":"MESH:D006046"},{"id":"A167","pred":"tao:has_database_id","subj":"167","obj":"MESH:D010984"},{"id":"A168","pred":"tao:has_database_id","subj":"168","obj":"MESH:D008670"},{"id":"A169","pred":"tao:has_database_id","subj":"169","obj":"MESH:D008670"},{"id":"A171","pred":"tao:has_database_id","subj":"171","obj":"CVCL:S575"}],"namespaces":[{"prefix":"Tax","uri":"https://www.ncbi.nlm.nih.gov/taxonomy/"},{"prefix":"MESH","uri":"https://id.nlm.nih.gov/mesh/"},{"prefix":"Gene","uri":"https://www.ncbi.nlm.nih.gov/gene/"},{"prefix":"CVCL","uri":"https://web.expasy.org/cellosaurus/CVCL_"}],"text":"2.3. Fabrication\nCOC [42] is chosen as polymeric substrate because of its biocompatibility, optical transparency, physical resistance, chemical resistance, electrical insulation, and price. This copolymer consists of two monomers, an apolar bridged cyclic hydrocarbon (norbornene) monomer and a linear, lesser apolar, linear ethene monomers. Injection molded COC plates (10 cm by 10 cm and 1.5 mm thickness) of the grade TOPAS 6017 (see Figure 4a) are obtained via Kunststoff-Zentrum Leipzig (Kunststoff-Zentrum gGmbH, Leipzig, Germany). This grade is chosen because of its high norbornene content, giving it a relatively high Tg of 170 °C. This minimizes the chance of melting during the milling process and decreases the chance of heater failure due to a deforming substrate during operation of the heater [28]. The microfluidic structure explained in Section 2.1 is CNC-milled using a Mikron WF 21C milling machine (Mikron SA Agno, Agno, Switzerland), as can be seen in Figure 4b. Milling is a very fast prototyping technique and chosen because of its flexibility [41]. The milling creates a surface roughness, which increases the surface-area-to-volume ratio. This roughness increases the chance of inhibition during the amplification due to the interaction of the used chemicals with the surface [44]. It also causes a considerable loss of optical transparency, which could obstruct the potential use of in situ fluorescence detection in future devices. Therefore, a chemical post-treatment with cyclohexane vapor is done (see Figure 4c). Such treatment dissolves a thin outer layer of the COC substrate and causes reflowing of the surface roughness due to the surface tension of the material, restoring the optical transparency and reducing the surface roughness [59].\nCNC milling and subsequent cyclohexane vapor post-treatment are less suitable for mass production. However, COC has the possibility of being injection molded [42]. The used substrates are made using this method. This is a large-scale production method and could lower the costs of the eventual product and it eliminates the cyclohexane vapor post-treatment, as injection-molded chips would have the same optical transparency as the pristine substrates. Guckenberger et al. mention production costs of $ 47 per simple microfluidic device when only 50 pieces are fabricated [41]. This price is expected to drop drastically when large numbers are fabricated.\nA metal is deposited on the backside of the substrate using two laser-cut metal (Mo) shadow masks to outline the shape of the resistive heater (see Figure 4d). Mo has a smaller coefficient of thermal expansion than stainless steel, and therefore gives less deformation during the deposition. Metals of interest are Au or Pt, which are commonly used metals to function as resistive heaters [54]. The deposition methods studied are DC magnetron sputtering using a custom-build machine (Techno Centrum voor Onderwijs en Onderzoek, University of Twente, Enschede, The Netherlands) and e-beam physical vapor deposition (evaporation) using a Balzers BAK 600 CE (Oerlikon Balzers limited, Balzers, Principality of Liechtenstein). Both deposition methods are capable of large-scale production, which will lower the production costs in the large-volume production stage. The metal and deposition method will be chosen based on the metal adhesion performances on the COC substrate, which is studied using the Scotch tape test [60,61], and the resistance versus temperature behavior in the range 20 °C to 100 °C, which is measured in a Heraeus T5025 oven (Heraeus Holding GmbH, Hanau, Germany), customized with electrical readout and connected to a custom-build National Instruments LabVIEW program (Austin, TX, USA)."}
LitCovid-PD-UBERON
{"project":"LitCovid-PD-UBERON","denotations":[{"id":"T3","span":{"begin":2003,"end":2008},"obj":"Body_part"},{"id":"T4","span":{"begin":3199,"end":3204},"obj":"Body_part"}],"attributes":[{"id":"A3","pred":"uberon_id","subj":"T3","obj":"http://purl.obolibrary.org/obo/UBERON_0002542"},{"id":"A4","pred":"uberon_id","subj":"T4","obj":"http://purl.obolibrary.org/obo/UBERON_0002542"}],"text":"2.3. Fabrication\nCOC [42] is chosen as polymeric substrate because of its biocompatibility, optical transparency, physical resistance, chemical resistance, electrical insulation, and price. This copolymer consists of two monomers, an apolar bridged cyclic hydrocarbon (norbornene) monomer and a linear, lesser apolar, linear ethene monomers. Injection molded COC plates (10 cm by 10 cm and 1.5 mm thickness) of the grade TOPAS 6017 (see Figure 4a) are obtained via Kunststoff-Zentrum Leipzig (Kunststoff-Zentrum gGmbH, Leipzig, Germany). This grade is chosen because of its high norbornene content, giving it a relatively high Tg of 170 °C. This minimizes the chance of melting during the milling process and decreases the chance of heater failure due to a deforming substrate during operation of the heater [28]. The microfluidic structure explained in Section 2.1 is CNC-milled using a Mikron WF 21C milling machine (Mikron SA Agno, Agno, Switzerland), as can be seen in Figure 4b. Milling is a very fast prototyping technique and chosen because of its flexibility [41]. The milling creates a surface roughness, which increases the surface-area-to-volume ratio. This roughness increases the chance of inhibition during the amplification due to the interaction of the used chemicals with the surface [44]. It also causes a considerable loss of optical transparency, which could obstruct the potential use of in situ fluorescence detection in future devices. Therefore, a chemical post-treatment with cyclohexane vapor is done (see Figure 4c). Such treatment dissolves a thin outer layer of the COC substrate and causes reflowing of the surface roughness due to the surface tension of the material, restoring the optical transparency and reducing the surface roughness [59].\nCNC milling and subsequent cyclohexane vapor post-treatment are less suitable for mass production. However, COC has the possibility of being injection molded [42]. The used substrates are made using this method. This is a large-scale production method and could lower the costs of the eventual product and it eliminates the cyclohexane vapor post-treatment, as injection-molded chips would have the same optical transparency as the pristine substrates. Guckenberger et al. mention production costs of $ 47 per simple microfluidic device when only 50 pieces are fabricated [41]. This price is expected to drop drastically when large numbers are fabricated.\nA metal is deposited on the backside of the substrate using two laser-cut metal (Mo) shadow masks to outline the shape of the resistive heater (see Figure 4d). Mo has a smaller coefficient of thermal expansion than stainless steel, and therefore gives less deformation during the deposition. Metals of interest are Au or Pt, which are commonly used metals to function as resistive heaters [54]. The deposition methods studied are DC magnetron sputtering using a custom-build machine (Techno Centrum voor Onderwijs en Onderzoek, University of Twente, Enschede, The Netherlands) and e-beam physical vapor deposition (evaporation) using a Balzers BAK 600 CE (Oerlikon Balzers limited, Balzers, Principality of Liechtenstein). Both deposition methods are capable of large-scale production, which will lower the production costs in the large-volume production stage. The metal and deposition method will be chosen based on the metal adhesion performances on the COC substrate, which is studied using the Scotch tape test [60,61], and the resistance versus temperature behavior in the range 20 °C to 100 °C, which is measured in a Heraeus T5025 oven (Heraeus Holding GmbH, Hanau, Germany), customized with electrical readout and connected to a custom-build National Instruments LabVIEW program (Austin, TX, USA)."}
LitCovid-PD-MONDO
{"project":"LitCovid-PD-MONDO","denotations":[{"id":"T24","span":{"begin":869,"end":872},"obj":"Disease"},{"id":"T26","span":{"begin":1775,"end":1778},"obj":"Disease"}],"attributes":[{"id":"A24","pred":"mondo_id","subj":"T24","obj":"http://purl.obolibrary.org/obo/MONDO_0015285"},{"id":"A25","pred":"mondo_id","subj":"T24","obj":"http://purl.obolibrary.org/obo/MONDO_0019134"},{"id":"A26","pred":"mondo_id","subj":"T26","obj":"http://purl.obolibrary.org/obo/MONDO_0015285"},{"id":"A27","pred":"mondo_id","subj":"T26","obj":"http://purl.obolibrary.org/obo/MONDO_0019134"}],"text":"2.3. Fabrication\nCOC [42] is chosen as polymeric substrate because of its biocompatibility, optical transparency, physical resistance, chemical resistance, electrical insulation, and price. This copolymer consists of two monomers, an apolar bridged cyclic hydrocarbon (norbornene) monomer and a linear, lesser apolar, linear ethene monomers. Injection molded COC plates (10 cm by 10 cm and 1.5 mm thickness) of the grade TOPAS 6017 (see Figure 4a) are obtained via Kunststoff-Zentrum Leipzig (Kunststoff-Zentrum gGmbH, Leipzig, Germany). This grade is chosen because of its high norbornene content, giving it a relatively high Tg of 170 °C. This minimizes the chance of melting during the milling process and decreases the chance of heater failure due to a deforming substrate during operation of the heater [28]. The microfluidic structure explained in Section 2.1 is CNC-milled using a Mikron WF 21C milling machine (Mikron SA Agno, Agno, Switzerland), as can be seen in Figure 4b. Milling is a very fast prototyping technique and chosen because of its flexibility [41]. The milling creates a surface roughness, which increases the surface-area-to-volume ratio. This roughness increases the chance of inhibition during the amplification due to the interaction of the used chemicals with the surface [44]. It also causes a considerable loss of optical transparency, which could obstruct the potential use of in situ fluorescence detection in future devices. Therefore, a chemical post-treatment with cyclohexane vapor is done (see Figure 4c). Such treatment dissolves a thin outer layer of the COC substrate and causes reflowing of the surface roughness due to the surface tension of the material, restoring the optical transparency and reducing the surface roughness [59].\nCNC milling and subsequent cyclohexane vapor post-treatment are less suitable for mass production. However, COC has the possibility of being injection molded [42]. The used substrates are made using this method. This is a large-scale production method and could lower the costs of the eventual product and it eliminates the cyclohexane vapor post-treatment, as injection-molded chips would have the same optical transparency as the pristine substrates. Guckenberger et al. mention production costs of $ 47 per simple microfluidic device when only 50 pieces are fabricated [41]. This price is expected to drop drastically when large numbers are fabricated.\nA metal is deposited on the backside of the substrate using two laser-cut metal (Mo) shadow masks to outline the shape of the resistive heater (see Figure 4d). Mo has a smaller coefficient of thermal expansion than stainless steel, and therefore gives less deformation during the deposition. Metals of interest are Au or Pt, which are commonly used metals to function as resistive heaters [54]. The deposition methods studied are DC magnetron sputtering using a custom-build machine (Techno Centrum voor Onderwijs en Onderzoek, University of Twente, Enschede, The Netherlands) and e-beam physical vapor deposition (evaporation) using a Balzers BAK 600 CE (Oerlikon Balzers limited, Balzers, Principality of Liechtenstein). Both deposition methods are capable of large-scale production, which will lower the production costs in the large-volume production stage. The metal and deposition method will be chosen based on the metal adhesion performances on the COC substrate, which is studied using the Scotch tape test [60,61], and the resistance versus temperature behavior in the range 20 °C to 100 °C, which is measured in a Heraeus T5025 oven (Heraeus Holding GmbH, Hanau, Germany), customized with electrical readout and connected to a custom-build National Instruments LabVIEW program (Austin, TX, USA)."}
LitCovid-PD-CLO
{"project":"LitCovid-PD-CLO","denotations":[{"id":"T150","span":{"begin":293,"end":294},"obj":"http://purl.obolibrary.org/obo/CLO_0001020"},{"id":"T151","span":{"begin":609,"end":610},"obj":"http://purl.obolibrary.org/obo/CLO_0001020"},{"id":"T152","span":{"begin":755,"end":756},"obj":"http://purl.obolibrary.org/obo/CLO_0001020"},{"id":"T153","span":{"begin":869,"end":872},"obj":"http://purl.obolibrary.org/obo/UBERON_0003099"},{"id":"T154","span":{"begin":886,"end":887},"obj":"http://purl.obolibrary.org/obo/CLO_0001020"},{"id":"T155","span":{"begin":995,"end":996},"obj":"http://purl.obolibrary.org/obo/CLO_0001020"},{"id":"T156","span":{"begin":1068,"end":1070},"obj":"http://purl.obolibrary.org/obo/CLO_0053794"},{"id":"T157","span":{"begin":1093,"end":1094},"obj":"http://purl.obolibrary.org/obo/CLO_0001020"},{"id":"T158","span":{"begin":1322,"end":1323},"obj":"http://purl.obolibrary.org/obo/CLO_0001020"},{"id":"T159","span":{"begin":1450,"end":1457},"obj":"http://purl.obolibrary.org/obo/OBI_0000968"},{"id":"T160","span":{"begin":1470,"end":1471},"obj":"http://purl.obolibrary.org/obo/CLO_0001020"},{"id":"T161","span":{"begin":1539,"end":1541},"obj":"http://purl.obolibrary.org/obo/CLO_0001387"},{"id":"T162","span":{"begin":1569,"end":1570},"obj":"http://purl.obolibrary.org/obo/CLO_0001020"},{"id":"T163","span":{"begin":1775,"end":1778},"obj":"http://purl.obolibrary.org/obo/UBERON_0003099"},{"id":"T164","span":{"begin":1887,"end":1890},"obj":"http://purl.obolibrary.org/obo/CLO_0051582"},{"id":"T165","span":{"begin":1995,"end":1996},"obj":"http://purl.obolibrary.org/obo/CLO_0001020"},{"id":"T166","span":{"begin":2305,"end":2311},"obj":"http://purl.obolibrary.org/obo/OBI_0000968"},{"id":"T167","span":{"begin":2348,"end":2350},"obj":"http://purl.obolibrary.org/obo/CLO_0053794"},{"id":"T168","span":{"begin":2431,"end":2432},"obj":"http://purl.obolibrary.org/obo/CLO_0001020"},{"id":"T169","span":{"begin":2512,"end":2514},"obj":"http://purl.obolibrary.org/obo/CLO_0007815"},{"id":"T170","span":{"begin":2591,"end":2593},"obj":"http://purl.obolibrary.org/obo/CLO_0007815"},{"id":"T171","span":{"begin":2594,"end":2597},"obj":"http://purl.obolibrary.org/obo/CLO_0051582"},{"id":"T172","span":{"begin":2598,"end":2599},"obj":"http://purl.obolibrary.org/obo/CLO_0001020"},{"id":"T173","span":{"begin":2891,"end":2892},"obj":"http://purl.obolibrary.org/obo/CLO_0001020"},{"id":"T174","span":{"begin":2945,"end":2947},"obj":"http://purl.obolibrary.org/obo/CLO_0037161"},{"id":"T175","span":{"begin":3065,"end":3066},"obj":"http://purl.obolibrary.org/obo/CLO_0001020"},{"id":"T176","span":{"begin":3442,"end":3446},"obj":"http://purl.obolibrary.org/obo/UBERON_0000473"},{"id":"T177","span":{"begin":3554,"end":3555},"obj":"http://purl.obolibrary.org/obo/CLO_0001020"},{"id":"T178","span":{"begin":3667,"end":3668},"obj":"http://purl.obolibrary.org/obo/CLO_0001020"},{"id":"T179","span":{"begin":3691,"end":3702},"obj":"http://purl.obolibrary.org/obo/OBI_0000968"}],"text":"2.3. Fabrication\nCOC [42] is chosen as polymeric substrate because of its biocompatibility, optical transparency, physical resistance, chemical resistance, electrical insulation, and price. This copolymer consists of two monomers, an apolar bridged cyclic hydrocarbon (norbornene) monomer and a linear, lesser apolar, linear ethene monomers. Injection molded COC plates (10 cm by 10 cm and 1.5 mm thickness) of the grade TOPAS 6017 (see Figure 4a) are obtained via Kunststoff-Zentrum Leipzig (Kunststoff-Zentrum gGmbH, Leipzig, Germany). This grade is chosen because of its high norbornene content, giving it a relatively high Tg of 170 °C. This minimizes the chance of melting during the milling process and decreases the chance of heater failure due to a deforming substrate during operation of the heater [28]. The microfluidic structure explained in Section 2.1 is CNC-milled using a Mikron WF 21C milling machine (Mikron SA Agno, Agno, Switzerland), as can be seen in Figure 4b. Milling is a very fast prototyping technique and chosen because of its flexibility [41]. The milling creates a surface roughness, which increases the surface-area-to-volume ratio. This roughness increases the chance of inhibition during the amplification due to the interaction of the used chemicals with the surface [44]. It also causes a considerable loss of optical transparency, which could obstruct the potential use of in situ fluorescence detection in future devices. Therefore, a chemical post-treatment with cyclohexane vapor is done (see Figure 4c). Such treatment dissolves a thin outer layer of the COC substrate and causes reflowing of the surface roughness due to the surface tension of the material, restoring the optical transparency and reducing the surface roughness [59].\nCNC milling and subsequent cyclohexane vapor post-treatment are less suitable for mass production. However, COC has the possibility of being injection molded [42]. The used substrates are made using this method. This is a large-scale production method and could lower the costs of the eventual product and it eliminates the cyclohexane vapor post-treatment, as injection-molded chips would have the same optical transparency as the pristine substrates. Guckenberger et al. mention production costs of $ 47 per simple microfluidic device when only 50 pieces are fabricated [41]. This price is expected to drop drastically when large numbers are fabricated.\nA metal is deposited on the backside of the substrate using two laser-cut metal (Mo) shadow masks to outline the shape of the resistive heater (see Figure 4d). Mo has a smaller coefficient of thermal expansion than stainless steel, and therefore gives less deformation during the deposition. Metals of interest are Au or Pt, which are commonly used metals to function as resistive heaters [54]. The deposition methods studied are DC magnetron sputtering using a custom-build machine (Techno Centrum voor Onderwijs en Onderzoek, University of Twente, Enschede, The Netherlands) and e-beam physical vapor deposition (evaporation) using a Balzers BAK 600 CE (Oerlikon Balzers limited, Balzers, Principality of Liechtenstein). Both deposition methods are capable of large-scale production, which will lower the production costs in the large-volume production stage. The metal and deposition method will be chosen based on the metal adhesion performances on the COC substrate, which is studied using the Scotch tape test [60,61], and the resistance versus temperature behavior in the range 20 °C to 100 °C, which is measured in a Heraeus T5025 oven (Heraeus Holding GmbH, Hanau, Germany), customized with electrical readout and connected to a custom-build National Instruments LabVIEW program (Austin, TX, USA)."}
LitCovid-PD-CHEBI
{"project":"LitCovid-PD-CHEBI","denotations":[{"id":"T136","span":{"begin":17,"end":20},"obj":"Chemical"},{"id":"T137","span":{"begin":195,"end":204},"obj":"Chemical"},{"id":"T139","span":{"begin":249,"end":267},"obj":"Chemical"},{"id":"T140","span":{"begin":256,"end":267},"obj":"Chemical"},{"id":"T141","span":{"begin":269,"end":279},"obj":"Chemical"},{"id":"T142","span":{"begin":325,"end":331},"obj":"Chemical"},{"id":"T143","span":{"begin":359,"end":362},"obj":"Chemical"},{"id":"T144","span":{"begin":465,"end":475},"obj":"Chemical"},{"id":"T145","span":{"begin":493,"end":503},"obj":"Chemical"},{"id":"T146","span":{"begin":579,"end":589},"obj":"Chemical"},{"id":"T147","span":{"begin":627,"end":629},"obj":"Chemical"},{"id":"T148","span":{"begin":869,"end":872},"obj":"Chemical"},{"id":"T149","span":{"begin":895,"end":897},"obj":"Chemical"},{"id":"T150","span":{"begin":926,"end":928},"obj":"Chemical"},{"id":"T154","span":{"begin":1501,"end":1512},"obj":"Chemical"},{"id":"T155","span":{"begin":1595,"end":1598},"obj":"Chemical"},{"id":"T156","span":{"begin":1775,"end":1778},"obj":"Chemical"},{"id":"T157","span":{"begin":1802,"end":1813},"obj":"Chemical"},{"id":"T158","span":{"begin":1883,"end":1886},"obj":"Chemical"},{"id":"T159","span":{"begin":2099,"end":2110},"obj":"Chemical"},{"id":"T160","span":{"begin":2512,"end":2514},"obj":"Chemical"},{"id":"T161","span":{"begin":2591,"end":2593},"obj":"Chemical"},{"id":"T162","span":{"begin":2746,"end":2748},"obj":"Chemical"},{"id":"T163","span":{"begin":2752,"end":2754},"obj":"Chemical"},{"id":"T165","span":{"begin":2780,"end":2786},"obj":"Chemical"},{"id":"T166","span":{"begin":2945,"end":2947},"obj":"Chemical"},{"id":"T167","span":{"begin":3083,"end":3085},"obj":"Chemical"},{"id":"T168","span":{"begin":3388,"end":3391},"obj":"Chemical"}],"attributes":[{"id":"A136","pred":"chebi_id","subj":"T136","obj":"http://purl.obolibrary.org/obo/CHEBI_53310"},{"id":"A137","pred":"chebi_id","subj":"T137","obj":"http://purl.obolibrary.org/obo/CHEBI_53310"},{"id":"A138","pred":"chebi_id","subj":"T137","obj":"http://purl.obolibrary.org/obo/CHEBI_60804"},{"id":"A139","pred":"chebi_id","subj":"T139","obj":"http://purl.obolibrary.org/obo/CHEBI_33663"},{"id":"A140","pred":"chebi_id","subj":"T140","obj":"http://purl.obolibrary.org/obo/CHEBI_24632"},{"id":"A141","pred":"chebi_id","subj":"T141","obj":"http://purl.obolibrary.org/obo/CHEBI_52286"},{"id":"A142","pred":"chebi_id","subj":"T142","obj":"http://purl.obolibrary.org/obo/CHEBI_18153"},{"id":"A143","pred":"chebi_id","subj":"T143","obj":"http://purl.obolibrary.org/obo/CHEBI_53310"},{"id":"A144","pred":"chebi_id","subj":"T144","obj":"http://purl.obolibrary.org/obo/CHEBI_60027"},{"id":"A145","pred":"chebi_id","subj":"T145","obj":"http://purl.obolibrary.org/obo/CHEBI_60027"},{"id":"A146","pred":"chebi_id","subj":"T146","obj":"http://purl.obolibrary.org/obo/CHEBI_52286"},{"id":"A147","pred":"chebi_id","subj":"T147","obj":"http://purl.obolibrary.org/obo/CHEBI_9516"},{"id":"A148","pred":"chebi_id","subj":"T148","obj":"http://purl.obolibrary.org/obo/CHEBI_48390"},{"id":"A149","pred":"chebi_id","subj":"T149","obj":"http://purl.obolibrary.org/obo/CHEBI_74874"},{"id":"A150","pred":"chebi_id","subj":"T150","obj":"http://purl.obolibrary.org/obo/CHEBI_35962"},{"id":"A151","pred":"chebi_id","subj":"T150","obj":"http://purl.obolibrary.org/obo/CHEBI_38358"},{"id":"A152","pred":"chebi_id","subj":"T150","obj":"http://purl.obolibrary.org/obo/CHEBI_45373"},{"id":"A153","pred":"chebi_id","subj":"T150","obj":"http://purl.obolibrary.org/obo/CHEBI_74801"},{"id":"A154","pred":"chebi_id","subj":"T154","obj":"http://purl.obolibrary.org/obo/CHEBI_29005"},{"id":"A155","pred":"chebi_id","subj":"T155","obj":"http://purl.obolibrary.org/obo/CHEBI_53310"},{"id":"A156","pred":"chebi_id","subj":"T156","obj":"http://purl.obolibrary.org/obo/CHEBI_48390"},{"id":"A157","pred":"chebi_id","subj":"T157","obj":"http://purl.obolibrary.org/obo/CHEBI_29005"},{"id":"A158","pred":"chebi_id","subj":"T158","obj":"http://purl.obolibrary.org/obo/CHEBI_53310"},{"id":"A159","pred":"chebi_id","subj":"T159","obj":"http://purl.obolibrary.org/obo/CHEBI_29005"},{"id":"A160","pred":"chebi_id","subj":"T160","obj":"http://purl.obolibrary.org/obo/CHEBI_28685"},{"id":"A161","pred":"chebi_id","subj":"T161","obj":"http://purl.obolibrary.org/obo/CHEBI_28685"},{"id":"A162","pred":"chebi_id","subj":"T162","obj":"http://purl.obolibrary.org/obo/CHEBI_29287"},{"id":"A163","pred":"chebi_id","subj":"T163","obj":"http://purl.obolibrary.org/obo/CHEBI_33364"},{"id":"A164","pred":"chebi_id","subj":"T163","obj":"http://purl.obolibrary.org/obo/CHEBI_75318"},{"id":"A165","pred":"chebi_id","subj":"T165","obj":"http://purl.obolibrary.org/obo/CHEBI_33521"},{"id":"A166","pred":"chebi_id","subj":"T166","obj":"http://purl.obolibrary.org/obo/CHEBI_30347"},{"id":"A167","pred":"chebi_id","subj":"T167","obj":"http://purl.obolibrary.org/obo/CHEBI_3663"},{"id":"A168","pred":"chebi_id","subj":"T168","obj":"http://purl.obolibrary.org/obo/CHEBI_53310"}],"text":"2.3. Fabrication\nCOC [42] is chosen as polymeric substrate because of its biocompatibility, optical transparency, physical resistance, chemical resistance, electrical insulation, and price. This copolymer consists of two monomers, an apolar bridged cyclic hydrocarbon (norbornene) monomer and a linear, lesser apolar, linear ethene monomers. Injection molded COC plates (10 cm by 10 cm and 1.5 mm thickness) of the grade TOPAS 6017 (see Figure 4a) are obtained via Kunststoff-Zentrum Leipzig (Kunststoff-Zentrum gGmbH, Leipzig, Germany). This grade is chosen because of its high norbornene content, giving it a relatively high Tg of 170 °C. This minimizes the chance of melting during the milling process and decreases the chance of heater failure due to a deforming substrate during operation of the heater [28]. The microfluidic structure explained in Section 2.1 is CNC-milled using a Mikron WF 21C milling machine (Mikron SA Agno, Agno, Switzerland), as can be seen in Figure 4b. Milling is a very fast prototyping technique and chosen because of its flexibility [41]. The milling creates a surface roughness, which increases the surface-area-to-volume ratio. This roughness increases the chance of inhibition during the amplification due to the interaction of the used chemicals with the surface [44]. It also causes a considerable loss of optical transparency, which could obstruct the potential use of in situ fluorescence detection in future devices. Therefore, a chemical post-treatment with cyclohexane vapor is done (see Figure 4c). Such treatment dissolves a thin outer layer of the COC substrate and causes reflowing of the surface roughness due to the surface tension of the material, restoring the optical transparency and reducing the surface roughness [59].\nCNC milling and subsequent cyclohexane vapor post-treatment are less suitable for mass production. However, COC has the possibility of being injection molded [42]. The used substrates are made using this method. This is a large-scale production method and could lower the costs of the eventual product and it eliminates the cyclohexane vapor post-treatment, as injection-molded chips would have the same optical transparency as the pristine substrates. Guckenberger et al. mention production costs of $ 47 per simple microfluidic device when only 50 pieces are fabricated [41]. This price is expected to drop drastically when large numbers are fabricated.\nA metal is deposited on the backside of the substrate using two laser-cut metal (Mo) shadow masks to outline the shape of the resistive heater (see Figure 4d). Mo has a smaller coefficient of thermal expansion than stainless steel, and therefore gives less deformation during the deposition. Metals of interest are Au or Pt, which are commonly used metals to function as resistive heaters [54]. The deposition methods studied are DC magnetron sputtering using a custom-build machine (Techno Centrum voor Onderwijs en Onderzoek, University of Twente, Enschede, The Netherlands) and e-beam physical vapor deposition (evaporation) using a Balzers BAK 600 CE (Oerlikon Balzers limited, Balzers, Principality of Liechtenstein). Both deposition methods are capable of large-scale production, which will lower the production costs in the large-volume production stage. The metal and deposition method will be chosen based on the metal adhesion performances on the COC substrate, which is studied using the Scotch tape test [60,61], and the resistance versus temperature behavior in the range 20 °C to 100 °C, which is measured in a Heraeus T5025 oven (Heraeus Holding GmbH, Hanau, Germany), customized with electrical readout and connected to a custom-build National Instruments LabVIEW program (Austin, TX, USA)."}
LitCovid-PD-GO-BP
{"project":"LitCovid-PD-GO-BP","denotations":[{"id":"T8","span":{"begin":3494,"end":3502},"obj":"http://purl.obolibrary.org/obo/GO_0007610"}],"text":"2.3. Fabrication\nCOC [42] is chosen as polymeric substrate because of its biocompatibility, optical transparency, physical resistance, chemical resistance, electrical insulation, and price. This copolymer consists of two monomers, an apolar bridged cyclic hydrocarbon (norbornene) monomer and a linear, lesser apolar, linear ethene monomers. Injection molded COC plates (10 cm by 10 cm and 1.5 mm thickness) of the grade TOPAS 6017 (see Figure 4a) are obtained via Kunststoff-Zentrum Leipzig (Kunststoff-Zentrum gGmbH, Leipzig, Germany). This grade is chosen because of its high norbornene content, giving it a relatively high Tg of 170 °C. This minimizes the chance of melting during the milling process and decreases the chance of heater failure due to a deforming substrate during operation of the heater [28]. The microfluidic structure explained in Section 2.1 is CNC-milled using a Mikron WF 21C milling machine (Mikron SA Agno, Agno, Switzerland), as can be seen in Figure 4b. Milling is a very fast prototyping technique and chosen because of its flexibility [41]. The milling creates a surface roughness, which increases the surface-area-to-volume ratio. This roughness increases the chance of inhibition during the amplification due to the interaction of the used chemicals with the surface [44]. It also causes a considerable loss of optical transparency, which could obstruct the potential use of in situ fluorescence detection in future devices. Therefore, a chemical post-treatment with cyclohexane vapor is done (see Figure 4c). Such treatment dissolves a thin outer layer of the COC substrate and causes reflowing of the surface roughness due to the surface tension of the material, restoring the optical transparency and reducing the surface roughness [59].\nCNC milling and subsequent cyclohexane vapor post-treatment are less suitable for mass production. However, COC has the possibility of being injection molded [42]. The used substrates are made using this method. This is a large-scale production method and could lower the costs of the eventual product and it eliminates the cyclohexane vapor post-treatment, as injection-molded chips would have the same optical transparency as the pristine substrates. Guckenberger et al. mention production costs of $ 47 per simple microfluidic device when only 50 pieces are fabricated [41]. This price is expected to drop drastically when large numbers are fabricated.\nA metal is deposited on the backside of the substrate using two laser-cut metal (Mo) shadow masks to outline the shape of the resistive heater (see Figure 4d). Mo has a smaller coefficient of thermal expansion than stainless steel, and therefore gives less deformation during the deposition. Metals of interest are Au or Pt, which are commonly used metals to function as resistive heaters [54]. The deposition methods studied are DC magnetron sputtering using a custom-build machine (Techno Centrum voor Onderwijs en Onderzoek, University of Twente, Enschede, The Netherlands) and e-beam physical vapor deposition (evaporation) using a Balzers BAK 600 CE (Oerlikon Balzers limited, Balzers, Principality of Liechtenstein). Both deposition methods are capable of large-scale production, which will lower the production costs in the large-volume production stage. The metal and deposition method will be chosen based on the metal adhesion performances on the COC substrate, which is studied using the Scotch tape test [60,61], and the resistance versus temperature behavior in the range 20 °C to 100 °C, which is measured in a Heraeus T5025 oven (Heraeus Holding GmbH, Hanau, Germany), customized with electrical readout and connected to a custom-build National Instruments LabVIEW program (Austin, TX, USA)."}
LitCovid-sentences
{"project":"LitCovid-sentences","denotations":[{"id":"T169","span":{"begin":0,"end":4},"obj":"Sentence"},{"id":"T170","span":{"begin":5,"end":16},"obj":"Sentence"},{"id":"T171","span":{"begin":17,"end":189},"obj":"Sentence"},{"id":"T172","span":{"begin":190,"end":341},"obj":"Sentence"},{"id":"T173","span":{"begin":342,"end":537},"obj":"Sentence"},{"id":"T174","span":{"begin":538,"end":640},"obj":"Sentence"},{"id":"T175","span":{"begin":641,"end":813},"obj":"Sentence"},{"id":"T176","span":{"begin":814,"end":983},"obj":"Sentence"},{"id":"T177","span":{"begin":984,"end":1072},"obj":"Sentence"},{"id":"T178","span":{"begin":1073,"end":1163},"obj":"Sentence"},{"id":"T179","span":{"begin":1164,"end":1306},"obj":"Sentence"},{"id":"T180","span":{"begin":1307,"end":1458},"obj":"Sentence"},{"id":"T181","span":{"begin":1459,"end":1543},"obj":"Sentence"},{"id":"T182","span":{"begin":1544,"end":1774},"obj":"Sentence"},{"id":"T183","span":{"begin":1775,"end":1873},"obj":"Sentence"},{"id":"T184","span":{"begin":1874,"end":1938},"obj":"Sentence"},{"id":"T185","span":{"begin":1939,"end":1986},"obj":"Sentence"},{"id":"T186","span":{"begin":1987,"end":2227},"obj":"Sentence"},{"id":"T187","span":{"begin":2228,"end":2352},"obj":"Sentence"},{"id":"T188","span":{"begin":2353,"end":2430},"obj":"Sentence"},{"id":"T189","span":{"begin":2431,"end":2590},"obj":"Sentence"},{"id":"T190","span":{"begin":2591,"end":2722},"obj":"Sentence"},{"id":"T191","span":{"begin":2723,"end":2825},"obj":"Sentence"},{"id":"T192","span":{"begin":2826,"end":3153},"obj":"Sentence"},{"id":"T193","span":{"begin":3154,"end":3292},"obj":"Sentence"},{"id":"T194","span":{"begin":3293,"end":3737},"obj":"Sentence"}],"namespaces":[{"prefix":"_base","uri":"http://pubannotation.org/ontology/tao.owl#"}],"text":"2.3. Fabrication\nCOC [42] is chosen as polymeric substrate because of its biocompatibility, optical transparency, physical resistance, chemical resistance, electrical insulation, and price. This copolymer consists of two monomers, an apolar bridged cyclic hydrocarbon (norbornene) monomer and a linear, lesser apolar, linear ethene monomers. Injection molded COC plates (10 cm by 10 cm and 1.5 mm thickness) of the grade TOPAS 6017 (see Figure 4a) are obtained via Kunststoff-Zentrum Leipzig (Kunststoff-Zentrum gGmbH, Leipzig, Germany). This grade is chosen because of its high norbornene content, giving it a relatively high Tg of 170 °C. This minimizes the chance of melting during the milling process and decreases the chance of heater failure due to a deforming substrate during operation of the heater [28]. The microfluidic structure explained in Section 2.1 is CNC-milled using a Mikron WF 21C milling machine (Mikron SA Agno, Agno, Switzerland), as can be seen in Figure 4b. Milling is a very fast prototyping technique and chosen because of its flexibility [41]. The milling creates a surface roughness, which increases the surface-area-to-volume ratio. This roughness increases the chance of inhibition during the amplification due to the interaction of the used chemicals with the surface [44]. It also causes a considerable loss of optical transparency, which could obstruct the potential use of in situ fluorescence detection in future devices. Therefore, a chemical post-treatment with cyclohexane vapor is done (see Figure 4c). Such treatment dissolves a thin outer layer of the COC substrate and causes reflowing of the surface roughness due to the surface tension of the material, restoring the optical transparency and reducing the surface roughness [59].\nCNC milling and subsequent cyclohexane vapor post-treatment are less suitable for mass production. However, COC has the possibility of being injection molded [42]. The used substrates are made using this method. This is a large-scale production method and could lower the costs of the eventual product and it eliminates the cyclohexane vapor post-treatment, as injection-molded chips would have the same optical transparency as the pristine substrates. Guckenberger et al. mention production costs of $ 47 per simple microfluidic device when only 50 pieces are fabricated [41]. This price is expected to drop drastically when large numbers are fabricated.\nA metal is deposited on the backside of the substrate using two laser-cut metal (Mo) shadow masks to outline the shape of the resistive heater (see Figure 4d). Mo has a smaller coefficient of thermal expansion than stainless steel, and therefore gives less deformation during the deposition. Metals of interest are Au or Pt, which are commonly used metals to function as resistive heaters [54]. The deposition methods studied are DC magnetron sputtering using a custom-build machine (Techno Centrum voor Onderwijs en Onderzoek, University of Twente, Enschede, The Netherlands) and e-beam physical vapor deposition (evaporation) using a Balzers BAK 600 CE (Oerlikon Balzers limited, Balzers, Principality of Liechtenstein). Both deposition methods are capable of large-scale production, which will lower the production costs in the large-volume production stage. The metal and deposition method will be chosen based on the metal adhesion performances on the COC substrate, which is studied using the Scotch tape test [60,61], and the resistance versus temperature behavior in the range 20 °C to 100 °C, which is measured in a Heraeus T5025 oven (Heraeus Holding GmbH, Hanau, Germany), customized with electrical readout and connected to a custom-build National Instruments LabVIEW program (Austin, TX, USA)."}
2_test
{"project":"2_test","denotations":[{"id":"32106462-25906246-69893319","span":{"begin":1068,"end":1070},"obj":"25906246"},{"id":"32106462-25906246-69893320","span":{"begin":2348,"end":2350},"obj":"25906246"},{"id":"32106462-26835667-69893321","span":{"begin":2821,"end":2823},"obj":"26835667"}],"text":"2.3. Fabrication\nCOC [42] is chosen as polymeric substrate because of its biocompatibility, optical transparency, physical resistance, chemical resistance, electrical insulation, and price. This copolymer consists of two monomers, an apolar bridged cyclic hydrocarbon (norbornene) monomer and a linear, lesser apolar, linear ethene monomers. Injection molded COC plates (10 cm by 10 cm and 1.5 mm thickness) of the grade TOPAS 6017 (see Figure 4a) are obtained via Kunststoff-Zentrum Leipzig (Kunststoff-Zentrum gGmbH, Leipzig, Germany). This grade is chosen because of its high norbornene content, giving it a relatively high Tg of 170 °C. This minimizes the chance of melting during the milling process and decreases the chance of heater failure due to a deforming substrate during operation of the heater [28]. The microfluidic structure explained in Section 2.1 is CNC-milled using a Mikron WF 21C milling machine (Mikron SA Agno, Agno, Switzerland), as can be seen in Figure 4b. Milling is a very fast prototyping technique and chosen because of its flexibility [41]. The milling creates a surface roughness, which increases the surface-area-to-volume ratio. This roughness increases the chance of inhibition during the amplification due to the interaction of the used chemicals with the surface [44]. It also causes a considerable loss of optical transparency, which could obstruct the potential use of in situ fluorescence detection in future devices. Therefore, a chemical post-treatment with cyclohexane vapor is done (see Figure 4c). Such treatment dissolves a thin outer layer of the COC substrate and causes reflowing of the surface roughness due to the surface tension of the material, restoring the optical transparency and reducing the surface roughness [59].\nCNC milling and subsequent cyclohexane vapor post-treatment are less suitable for mass production. However, COC has the possibility of being injection molded [42]. The used substrates are made using this method. This is a large-scale production method and could lower the costs of the eventual product and it eliminates the cyclohexane vapor post-treatment, as injection-molded chips would have the same optical transparency as the pristine substrates. Guckenberger et al. mention production costs of $ 47 per simple microfluidic device when only 50 pieces are fabricated [41]. This price is expected to drop drastically when large numbers are fabricated.\nA metal is deposited on the backside of the substrate using two laser-cut metal (Mo) shadow masks to outline the shape of the resistive heater (see Figure 4d). Mo has a smaller coefficient of thermal expansion than stainless steel, and therefore gives less deformation during the deposition. Metals of interest are Au or Pt, which are commonly used metals to function as resistive heaters [54]. The deposition methods studied are DC magnetron sputtering using a custom-build machine (Techno Centrum voor Onderwijs en Onderzoek, University of Twente, Enschede, The Netherlands) and e-beam physical vapor deposition (evaporation) using a Balzers BAK 600 CE (Oerlikon Balzers limited, Balzers, Principality of Liechtenstein). Both deposition methods are capable of large-scale production, which will lower the production costs in the large-volume production stage. The metal and deposition method will be chosen based on the metal adhesion performances on the COC substrate, which is studied using the Scotch tape test [60,61], and the resistance versus temperature behavior in the range 20 °C to 100 °C, which is measured in a Heraeus T5025 oven (Heraeus Holding GmbH, Hanau, Germany), customized with electrical readout and connected to a custom-build National Instruments LabVIEW program (Austin, TX, USA)."}