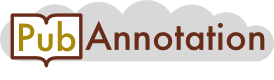
PMC:7143804 / 27292-43081
Annnotations
LitCovid-PubTator
{"project":"LitCovid-PubTator","denotations":[{"id":"195","span":{"begin":551,"end":554},"obj":"Chemical"},{"id":"196","span":{"begin":724,"end":727},"obj":"Chemical"},{"id":"197","span":{"begin":732,"end":735},"obj":"Chemical"},{"id":"198","span":{"begin":918,"end":921},"obj":"Chemical"},{"id":"199","span":{"begin":926,"end":929},"obj":"Chemical"},{"id":"200","span":{"begin":1124,"end":1127},"obj":"Chemical"},{"id":"201","span":{"begin":1132,"end":1135},"obj":"Chemical"},{"id":"204","span":{"begin":3086,"end":3091},"obj":"Chemical"},{"id":"205","span":{"begin":2940,"end":2948},"obj":"Disease"},{"id":"213","span":{"begin":4396,"end":4398},"obj":"Chemical"},{"id":"214","span":{"begin":4549,"end":4560},"obj":"Chemical"},{"id":"215","span":{"begin":4725,"end":4735},"obj":"Chemical"},{"id":"216","span":{"begin":4761,"end":4767},"obj":"Chemical"},{"id":"217","span":{"begin":4782,"end":4792},"obj":"Chemical"},{"id":"218","span":{"begin":4827,"end":4845},"obj":"Chemical"},{"id":"219","span":{"begin":4945,"end":4956},"obj":"Chemical"},{"id":"221","span":{"begin":5719,"end":5724},"obj":"Chemical"},{"id":"227","span":{"begin":5866,"end":5868},"obj":"Chemical"},{"id":"228","span":{"begin":5873,"end":5875},"obj":"Chemical"},{"id":"229","span":{"begin":6077,"end":6082},"obj":"Chemical"},{"id":"230","span":{"begin":6146,"end":6151},"obj":"Chemical"},{"id":"231","span":{"begin":6212,"end":6221},"obj":"Chemical"},{"id":"237","span":{"begin":6404,"end":6409},"obj":"Chemical"},{"id":"238","span":{"begin":6462,"end":6467},"obj":"Chemical"},{"id":"239","span":{"begin":6997,"end":7000},"obj":"Chemical"},{"id":"240","span":{"begin":7067,"end":7069},"obj":"Chemical"},{"id":"241","span":{"begin":7074,"end":7076},"obj":"Chemical"},{"id":"248","span":{"begin":7116,"end":7121},"obj":"Chemical"},{"id":"249","span":{"begin":7755,"end":7757},"obj":"Chemical"},{"id":"250","span":{"begin":7762,"end":7764},"obj":"Chemical"},{"id":"251","span":{"begin":8004,"end":8009},"obj":"Chemical"},{"id":"252","span":{"begin":8023,"end":8025},"obj":"Chemical"},{"id":"253","span":{"begin":8041,"end":8043},"obj":"Chemical"},{"id":"255","span":{"begin":8224,"end":8229},"obj":"Chemical"},{"id":"259","span":{"begin":8466,"end":8469},"obj":"Chemical"},{"id":"260","span":{"begin":8498,"end":8503},"obj":"Chemical"},{"id":"261","span":{"begin":8919,"end":8922},"obj":"Chemical"},{"id":"263","span":{"begin":9138,"end":9140},"obj":"Chemical"},{"id":"266","span":{"begin":9628,"end":9630},"obj":"Chemical"},{"id":"267","span":{"begin":10332,"end":10337},"obj":"Chemical"},{"id":"270","span":{"begin":11803,"end":11806},"obj":"Gene"},{"id":"271","span":{"begin":11760,"end":11763},"obj":"Gene"},{"id":"277","span":{"begin":12420,"end":12425},"obj":"Chemical"},{"id":"278","span":{"begin":12521,"end":12526},"obj":"Chemical"},{"id":"279","span":{"begin":12722,"end":12730},"obj":"Chemical"},{"id":"280","span":{"begin":13023,"end":13028},"obj":"Chemical"},{"id":"281","span":{"begin":13367,"end":13372},"obj":"Chemical"},{"id":"285","span":{"begin":13546,"end":13548},"obj":"Chemical"},{"id":"286","span":{"begin":13678,"end":13683},"obj":"Chemical"},{"id":"287","span":{"begin":13737,"end":13742},"obj":"Chemical"},{"id":"290","span":{"begin":14176,"end":14178},"obj":"Gene"},{"id":"291","span":{"begin":14189,"end":14194},"obj":"Chemical"},{"id":"296","span":{"begin":15058,"end":15063},"obj":"Chemical"},{"id":"297","span":{"begin":15100,"end":15102},"obj":"Chemical"},{"id":"298","span":{"begin":15203,"end":15208},"obj":"Chemical"},{"id":"299","span":{"begin":15410,"end":15417},"obj":"Chemical"}],"attributes":[{"id":"A204","pred":"tao:has_database_id","subj":"204","obj":"MESH:D008670"},{"id":"A205","pred":"tao:has_database_id","subj":"205","obj":"MESH:D000079225"},{"id":"A214","pred":"tao:has_database_id","subj":"214","obj":"MESH:C506365"},{"id":"A215","pred":"tao:has_database_id","subj":"215","obj":"MESH:C046060"},{"id":"A216","pred":"tao:has_database_id","subj":"216","obj":"MESH:C036216"},{"id":"A217","pred":"tao:has_database_id","subj":"217","obj":"MESH:C046060"},{"id":"A218","pred":"tao:has_database_id","subj":"218","obj":"MESH:D006844"},{"id":"A219","pred":"tao:has_database_id","subj":"219","obj":"MESH:C506365"},{"id":"A221","pred":"tao:has_database_id","subj":"221","obj":"MESH:D008670"},{"id":"A227","pred":"tao:has_database_id","subj":"227","obj":"MESH:D006046"},{"id":"A228","pred":"tao:has_database_id","subj":"228","obj":"MESH:D010984"},{"id":"A229","pred":"tao:has_database_id","subj":"229","obj":"MESH:D008670"},{"id":"A230","pred":"tao:has_database_id","subj":"230","obj":"MESH:D008670"},{"id":"A237","pred":"tao:has_database_id","subj":"237","obj":"MESH:D008670"},{"id":"A238","pred":"tao:has_database_id","subj":"238","obj":"MESH:D008670"},{"id":"A240","pred":"tao:has_database_id","subj":"240","obj":"MESH:D006046"},{"id":"A241","pred":"tao:has_database_id","subj":"241","obj":"MESH:D010984"},{"id":"A248","pred":"tao:has_database_id","subj":"248","obj":"MESH:D008670"},{"id":"A249","pred":"tao:has_database_id","subj":"249","obj":"MESH:D006046"},{"id":"A250","pred":"tao:has_database_id","subj":"250","obj":"MESH:D010984"},{"id":"A251","pred":"tao:has_database_id","subj":"251","obj":"MESH:D008670"},{"id":"A252","pred":"tao:has_database_id","subj":"252","obj":"MESH:D006046"},{"id":"A253","pred":"tao:has_database_id","subj":"253","obj":"MESH:D010984"},{"id":"A255","pred":"tao:has_database_id","subj":"255","obj":"MESH:D008670"},{"id":"A260","pred":"tao:has_database_id","subj":"260","obj":"MESH:D008670"},{"id":"A263","pred":"tao:has_database_id","subj":"263","obj":"MESH:D006046"},{"id":"A266","pred":"tao:has_database_id","subj":"266","obj":"MESH:D006046"},{"id":"A267","pred":"tao:has_database_id","subj":"267","obj":"MESH:D014867"},{"id":"A270","pred":"tao:has_database_id","subj":"270","obj":"Gene:6236"},{"id":"A271","pred":"tao:has_database_id","subj":"271","obj":"Gene:6236"},{"id":"A277","pred":"tao:has_database_id","subj":"277","obj":"MESH:D014867"},{"id":"A278","pred":"tao:has_database_id","subj":"278","obj":"MESH:D014867"},{"id":"A280","pred":"tao:has_database_id","subj":"280","obj":"MESH:D014867"},{"id":"A281","pred":"tao:has_database_id","subj":"281","obj":"MESH:D014867"},{"id":"A285","pred":"tao:has_database_id","subj":"285","obj":"MESH:D006046"},{"id":"A286","pred":"tao:has_database_id","subj":"286","obj":"MESH:D014867"},{"id":"A287","pred":"tao:has_database_id","subj":"287","obj":"MESH:D014867"},{"id":"A290","pred":"tao:has_database_id","subj":"290","obj":"Gene:4591"},{"id":"A291","pred":"tao:has_database_id","subj":"291","obj":"MESH:D014867"},{"id":"A296","pred":"tao:has_database_id","subj":"296","obj":"MESH:D014867"},{"id":"A297","pred":"tao:has_database_id","subj":"297","obj":"MESH:D006046"},{"id":"A298","pred":"tao:has_database_id","subj":"298","obj":"MESH:D014867"}],"namespaces":[{"prefix":"Tax","uri":"https://www.ncbi.nlm.nih.gov/taxonomy/"},{"prefix":"MESH","uri":"https://id.nlm.nih.gov/mesh/"},{"prefix":"Gene","uri":"https://www.ncbi.nlm.nih.gov/gene/"},{"prefix":"CVCL","uri":"https://web.expasy.org/cellosaurus/CVCL_"}],"text":"3. Results and Discussion\n\n3.1. COMSOL MultiPhysics Simulation Results\nIn Figure 5, the results of heat transfer simulations of two different heater spacings are shown. The heater width for both geometries is 0.3 mm, while the heater spacing in Figure 5b,c are 0.3 mm and 2.0 mm, respectively. In Figure 6a–d, tables with the results of the full parametric sweep for different heater widths and heater spacings are shown. Figure 6a shows the temperature deviation between the highest and lowest temperature at the top of the chamber, i.e., the second H2O and COC interface (ΔTtopofchamber=Ttop,max−Ttop,min). Figure 6b shows the deviation between the highest and lowest temperature inside the chamber, i.e., between the two COC and H2O interfaces (ΔTacrosschamber=Tbottom,max−Ttop,min). Figure 6c shows the temperature deviation between the highest and lowest temperature at the bottom of the chamber, i.e., the first COC and H2O interface (ΔTbottomofchamber=Tbot,max−Tbot,min). Figure 6d shows the deviation between the set heater temperature of 30 °C and the lowest temperature at the top of the chamber, i.e., the second H2O and COC interface (ΔTdeviationfromsetT=Theater−Ttop,min). As can be seen from the results in Figure 6, a combination of small heater widths and heater spacings will result in smaller temperature differences inside the reaction mixture. This is evident as smaller heater spacings will result in a better coverage of the heated area by heater material. The smaller heater widths will result in a smaller heater cross-sectional area, and thus can be operated at lower powers, as is evident from Equation (1). Resulting in the fact that a densely packed meander structure with small heater widths and small heater spacings can dissipate more heat into the system.\nBased on these results and its simplicity, a meandering heater pattern of a heater with a width of 0.3 mm and a spacing of 0.3 mm in between the lines is designed. A side note on the chosen heater width and heater spacing is that according to the simulations, the temperature differences within the chamber are less than ±0.3 °C for the most unfavorable dimensions. This temperature difference is still well-accepted in the temperature window in which the MDA reaction takes place (25 °C to 35 °C). However, as pointed out, a smaller cross-sectional area will result in a lower power consumption and therefore these dimensions are chosen. It is known that a meandering heater structure does not give the optimal temperature distribution over the device [26]. Therefore, the heater lines are longer than the width of the reaction chamber, and thus also covering the bulk material outside the chamber in order to improve the temperature uniformity inside the reaction mixture.\nThe heater pattern is divided over two shadow masks to minimize the length of the narrow Mo tracks in between the meandering structure. This prevents curvature due to intrinsic stresses. See Figure 7 for the outlines of both shadow masks, together with the resulting pattern on COC. The use of two shadow masks will give a metal track in which small parts has the double thickness. Here, the temperature will be lower. The system is designed such that these thicker parts are outside the reaction chamber and temperature control chamber region.\n\n3.2. Fabrication\n\nMilling and Optical Transparency\nThe milling increased the surface roughness of the COC plates also increases the surface area. Inhibition of the amplification can be caused by large surface areas as the used chemicals have more surface to have interaction with [44]. The created surface roughness is visualized using a FEI Sirion high resolution scanning electron microscope (HR-SEM) (FEI Company, Hillsboro, OR, USA) and measured using a Bruker Icon Dimension AFM in tapping mode with Bruker Tespa-V2 cantilevers (Bruker Nano Surfaces, Santa Barbara, CA, USA) and Gwyddion 2.52 open source freeware [62]. The results are shown in Figure 8. The surface roughness of pristine COC had a RRMS of 3.5 nm. This increased two orders of magnitude after milling (RRMS of 310.1 nm). With the reported surface treatment [44,59] we were capable of decreasing the surface roughness to a value even lower than that of pristine COC and the lowest reported in literature (RRMS of 0.9 nm). For this grade of COC (TOPAS 6017) it worked the best to do four short exposures of 5 s, with N2 blow drying after each exposure, instead of one longer exposure, as is more common in other grades of COC [44,59]. The difference in duration for the cyclohexane vapor post-treatment can be explained by the different ratios of the copolymers present in each grade. As the grade number increase, the ratio changes towards more norbornene monomers and less linear ethene monomers. The norbornene is more apolar due to the bridged cyclic hydrocarbon present in its molecular structure and therefore, will dissolve faster in non-polar solvents, like cyclohexane (vapor).\nLowering the surface roughness also increased the optical transmittance fivefold. Transmittance measurements in the visible range are done using a Woollam M-2000UI ellipsometer (J.A. Woollam Co., Lincoln, NE, USA). The results can be seen in Figure 9 and Figure 10. Having a high optical transparency in the visible range can be desired when in situ fluorescence detection will be implemented (e.g., EvaGreen fluorescence dye has an excitation wavelength of 500 nm and emission wavelength of 525 nm [63]). However, as in situ fluorescence detection is not used yet in this system and can also be done through the transparent PCR plate sealing foil, no further effort is put into optimizing this procedure to get even better optical transmittance.\n\n3.3. Metal Adhesion\nTo get reliable heaters, four possible options are investigated for their adhesion properties to the COC substrate. The adhesion of Au and Pt deposited by either evaporation or DC magnetron sputtering is investigated using the Scotch tape test [60,61] before and after temperature cycling up to 100 °C. Test patterns consisting of rectangular metal strips of 2 mm by 14 mm are fabricated by depositing 100 nm of metal using a hand-made shadow mask made out of DuPont Kapton® HN polyimide film of 0.05 mm thickness (RS Components B.V., Haarlem, The Netherlands). See Table 4 for the results of the Scotch tape test.\nNormally, heating up a glass or Si substrate with thin metal strips while measuring the resistance (RT) in these metal strips at certain temperature intervals (T) yields directly a linear relation, which can be fitted with RT/R0=1+αT−T0 [64], in which α is the the temperature coefficient of resistance (TCR) value. The thin-film TCR values have to be measured as they differ from the bulk TCR values due to its dependency on layer purity, grain size, and deposition method [65,66]. Belser and Hicklin also lists other attributes, such as surface roughness, porosity, and adsorbed materials present in or on the substrate which could influence the TCR value [64]. The bulk TCR values are 0.0034 K−1 and 0.0037 K−1 for Au and Pt [67].\nThe TCR characterizations of the metal strips on a COC substrate did not yield trustworthy TCR values at the first cycle. The first temperature cycle can be seen as a kind of thermal annealing, and therefore gives an hysteresis in the graphs, as can be seen in Figure A2 in Appendix C.1. After this first cycle, the values more or less show the linear behavior. The resulting TCR of this linear part is in agreement with the TCR ranges of Belser and Hicklin [64] and is given in Table 4. Belser and Hicklin used for their experiments substrates with coefficients of linear thermal expansion lower than 1.2 × 10−5 °C−1 [64]. The coefficient of linear thermal expansion for Au and Pt are 1.42 × 10−5 K−1 and 0.88 × 10−5 K−1, respectively [68]. COC of the grade TOPAS 6017 has a coefficient of linear thermal expansion of 6.0 × 10−5 K−1 [42]. This mismatch in coefficients of linear thermal expansion can give strain in the metal layers. Both Au [69,70,71] and Pt [72,73,74] are used as strain-sensitive gauges, and thus are sensitive to strain-induced geometry changes due to thermal expansion.\nAnother effect influencing the TCR value of the metal layer is aging. As can be seen in Figure A3 in Appendix C.2, the TCR value already changes after two weeks storing in ambient conditions. This could be due to adsorbed materials present on the surface [64].\nHowever, in this device, the TCR is not of importance as the metal structure will not be used as temperature sensor. Real-time temperature sensing is done using a thermocouple in the temperature monitor chamber. The resistance of the heater structure changes with temperature; thus, the dissipated power changes when a fixed voltage or current is used. However, the results in Section 3.4 show a 25 h stability test with a constant input potential and only a ±1.5 °C deviation. The TCR can become more important when other (higher) temperatures are required for the amplification.\nBased on the results in Table 4, the choice of heater material and deposition method to be used in the actual device is Au deposited using sputtering. Sputtering is an industrial-scale technique that is already being used in, for example, the car mirror and headlight industry [75].\n\n3.4. Chip Functioning\nCharacterization of the actual heat distribution is done using a FLIR One Pro iOS thermal camera (FLIR Systems, Inc., Wilsonville, OR, USA). Thermal images of the heat distribution are made at the side of the substrate without the resistor, whereas different input powers are used to heat up the heater. Au reflects the infrared radiation of the environment directly, therefore an image with the resistor facing the camera would give a heat map of the surrounding and not of the real temperature of the heater. These measurements also gives a better insight of the heat distribution inside the reaction chamber. The images are processed using the FLIR postprocessing freeware. Results of these measurements are shown in Figure 11a,b. The results are in good agreement with the estimations in Table 1. The slight deviation between the values can be explained by the fact that the heated area in the calculations had an assumed value, the thermal camera measurements used 1.5 mm thick COC substrates without a water-filled chamber, the actual resistors have small parts wich have a double thickness due to the two used shadow masks, and rounding of the values used in the calculations.\nThe reliability of the heater is tested by inserting the thermocouple into the temperature control chamber (see Figure 3a). A constant input potential of 4 V is applied using the Keithley source and the temperature is measured for 25 h. This exceeds the required operation time at least twelve-fold, meaning that it is a good indication for the reliability of the heater and thermocouple. The results are shown in Figure 11c.\nTo perform on-chip amplifications, the resistive heater on the chip is connected to the Keithley source using crocodile connections and the thermocouple is inserted in the temperature control chamber and connected to a Tenma 72-7715 Thermometer (see Figure 12).\n\n3.5. DNA Amplification\nFirst, to determine the temperature window of operation, MDA reactions are performed at 25 °C and 30 °C using the Illustra GenomiPhi V2 DNA amplification kit and EvaGreen fluorescence dye. From the literature, we know that this reaction does not work above 35 °C due to degradation of the protein activity in presence of a substrate [44]. In Figure 13, a graph of the fluorescence signal during MDA reactions at 25 °C and 30 °C, together with their non template control (NTC) is shown. These reactions are carried out in a conventional Bio-Rad CFX96 Touch Real-Time PCR machine (Bio-Rad Laboratories, Inc., Hercules, CA, USA) and the results show that the chosen proof-of-principle DNA amplification reaction is temperature dependent to some extent, but that there is a wide range of temperatures at which the amplification can be performed, i.e., 25°C to 35°C. This makes the functioning of the integrated resistive heater less critical than the stability shown in Figure 11c.\nMDA reactions are also performed inside an Eppendorf tube (Eppendorf AG, Hamburg, Germany) and inside the chip, again using the Illustra GenomiPhi V2 DNA amplification kit and EvaGreen fluorescence dye. As heat supply the water bath of an IKA Rotary Evaporator RV 8V (IKA-Werke, Staufen im Breisgau, Germany) is used. This water bath is according to its specification stable within a range of the set temperature ±0.1 °C. The chip and an Eppendorf tube are loaded with the reaction mixture containing the DNA sample and the EvaGreen dye solution. Here, the Eppendorf tube is serving as a control to show that the fabrication steps of the chips are not inhibiting the MDA reaction. The inlet and outlet of the chip are sealed with the Microseal “B” PCR plate sealing foil. The closed chip and tube are heated up in a separate water bath to 95 °C and kept at that temperature for 3 min to denaturate the dsDNA. Subsequently, the chip and tube are cooled down by placing it in an ice bath for 5 min after which the rest of the reagents are added. The complete mixtures are according to Table A3 in Appendix D. After closing the chip and tube again, they are placed in the water bath of the rotary evaporater and left there for 90 min, after which the reaction is terminated at 65 °C.\nThe MDA is also performed inside the chip, but with the integrated Au resistive heater serving as heat source. The set up shown schematically in Figure 12. The same procedure is followed as with the water bath heated test. Denaturation is done in a separate water bath. The heater is driven by an input potential of 3.2 V to get to a temperature of 30 °C and at the end of the reaction, the system is heated up to 65 °C by applying a potential of 9.2 V in order to terminate the amplification. In Figure 14 the logged temperature during the amplification is shown.\nAfter the amplifications, the reaction mixtures are pipetted out of the chips and tubes and into 1 mL quartz cuvettes containing 55 μL MilliQ DI water (Merck Millipore, Burlington, MA, USA). Fluorescence measurements are done in a Horiba Scientific FluoroMax+ spectrofluorometer to verify each amplification. The mixture is excitated at a wavelength of 500 nm and the emission spectrum is measured at wavelengths from 510 nm to 550 nm (bounded EvaGreen dye has a peak at 525 nm [63]). The measured spectra are normalized by subtracting the background signal of a mixture containing only the reaction buffer, the sample buffer, EvaGreen, and DNA. No Enzyme was added to this mixture, therefore no amplification could take place. See Figure 15 for the results obtained in the Eppendorf tube and chips. Figure A4 in Appendix E shows the background signal which is subtracted from all measurements.\nAs can be seen in Figure 15, the spectra of the amplification performed inside the chip, and by applying heat with the water bath as well as with the integrated Au-resistive heater, show the same trend as the amplification performed in the Eppendorf and heated by water bath. There is an order of magnitude difference in the fluorescence signal. However, the fluorescence intensity cannot be used as a value to quantify the amount of DNA. EvaGreen is a bis-intercalating cyanine fluorescence dye consisting of two monomeric DNA-binding dyes which are linked by a flexible spacer. These two DNA-binding dyes bind each in between two base pairs, which make them simple and fast, but also nonuniform and non-specific [44,63]. However, with this dye, a simple yes-or-no answer can be obtained if the amplification took place, as can be seen in Figure 15."}
LitCovid-PD-FMA-UBERON
{"project":"LitCovid-PD-FMA-UBERON","denotations":[{"id":"T50","span":{"begin":3827,"end":3829},"obj":"Body_part"},{"id":"T52","span":{"begin":6160,"end":6164},"obj":"Body_part"},{"id":"T53","span":{"begin":7351,"end":7353},"obj":"Body_part"},{"id":"T54","span":{"begin":7357,"end":7365},"obj":"Body_part"},{"id":"T55","span":{"begin":8271,"end":8273},"obj":"Body_part"},{"id":"T56","span":{"begin":8277,"end":8285},"obj":"Body_part"},{"id":"T57","span":{"begin":9765,"end":9768},"obj":"Body_part"},{"id":"T58","span":{"begin":11202,"end":11205},"obj":"Body_part"},{"id":"T59","span":{"begin":11353,"end":11355},"obj":"Body_part"},{"id":"T61","span":{"begin":11356,"end":11359},"obj":"Body_part"},{"id":"T62","span":{"begin":11509,"end":11516},"obj":"Body_part"},{"id":"T63","span":{"begin":11902,"end":11905},"obj":"Body_part"},{"id":"T64","span":{"begin":12267,"end":12269},"obj":"Body_part"},{"id":"T65","span":{"begin":12345,"end":12347},"obj":"Body_part"},{"id":"T67","span":{"begin":12348,"end":12351},"obj":"Body_part"},{"id":"T68","span":{"begin":12703,"end":12706},"obj":"Body_part"},{"id":"T69","span":{"begin":13287,"end":13289},"obj":"Body_part"},{"id":"T70","span":{"begin":13293,"end":13301},"obj":"Body_part"},{"id":"T71","span":{"begin":14685,"end":14688},"obj":"Body_part"},{"id":"T72","span":{"begin":14857,"end":14865},"obj":"Body_part"},{"id":"T73","span":{"begin":15373,"end":15376},"obj":"Body_part"},{"id":"T74","span":{"begin":15463,"end":15466},"obj":"Body_part"},{"id":"T75","span":{"begin":15529,"end":15532},"obj":"Body_part"}],"attributes":[{"id":"A50","pred":"fma_id","subj":"T50","obj":"http://purl.org/sig/ont/fma/fma13443"},{"id":"A51","pred":"fma_id","subj":"T50","obj":"http://purl.org/sig/ont/fma/fma68615"},{"id":"A52","pred":"fma_id","subj":"T52","obj":"http://purl.org/sig/ont/fma/fma9712"},{"id":"A53","pred":"fma_id","subj":"T53","obj":"http://purl.org/sig/ont/fma/fma66595"},{"id":"A54","pred":"fma_id","subj":"T54","obj":"http://purl.org/sig/ont/fma/fma14542"},{"id":"A55","pred":"fma_id","subj":"T55","obj":"http://purl.org/sig/ont/fma/fma66599"},{"id":"A56","pred":"fma_id","subj":"T56","obj":"http://purl.org/sig/ont/fma/fma14542"},{"id":"A57","pred":"fma_id","subj":"T57","obj":"http://purl.org/sig/ont/fma/fma67847"},{"id":"A58","pred":"fma_id","subj":"T58","obj":"http://purl.org/sig/ont/fma/fma74412"},{"id":"A59","pred":"fma_id","subj":"T59","obj":"http://purl.org/sig/ont/fma/fma13443"},{"id":"A60","pred":"fma_id","subj":"T59","obj":"http://purl.org/sig/ont/fma/fma68615"},{"id":"A61","pred":"fma_id","subj":"T61","obj":"http://purl.org/sig/ont/fma/fma74412"},{"id":"A62","pred":"fma_id","subj":"T62","obj":"http://purl.org/sig/ont/fma/fma67257"},{"id":"A63","pred":"fma_id","subj":"T63","obj":"http://purl.org/sig/ont/fma/fma74412"},{"id":"A64","pred":"fma_id","subj":"T64","obj":"http://purl.org/sig/ont/fma/fma61898"},{"id":"A65","pred":"fma_id","subj":"T65","obj":"http://purl.org/sig/ont/fma/fma13443"},{"id":"A66","pred":"fma_id","subj":"T65","obj":"http://purl.org/sig/ont/fma/fma68615"},{"id":"A67","pred":"fma_id","subj":"T67","obj":"http://purl.org/sig/ont/fma/fma74412"},{"id":"A68","pred":"fma_id","subj":"T68","obj":"http://purl.org/sig/ont/fma/fma74412"},{"id":"A69","pred":"fma_id","subj":"T69","obj":"http://purl.org/sig/ont/fma/fma66599"},{"id":"A70","pred":"fma_id","subj":"T70","obj":"http://purl.org/sig/ont/fma/fma14542"},{"id":"A71","pred":"fma_id","subj":"T71","obj":"http://purl.org/sig/ont/fma/fma74412"},{"id":"A72","pred":"fma_id","subj":"T72","obj":"http://purl.org/sig/ont/fma/fma14542"},{"id":"A73","pred":"fma_id","subj":"T73","obj":"http://purl.org/sig/ont/fma/fma74412"},{"id":"A74","pred":"fma_id","subj":"T74","obj":"http://purl.org/sig/ont/fma/fma74412"},{"id":"A75","pred":"fma_id","subj":"T75","obj":"http://purl.org/sig/ont/fma/fma74412"}],"text":"3. Results and Discussion\n\n3.1. COMSOL MultiPhysics Simulation Results\nIn Figure 5, the results of heat transfer simulations of two different heater spacings are shown. The heater width for both geometries is 0.3 mm, while the heater spacing in Figure 5b,c are 0.3 mm and 2.0 mm, respectively. In Figure 6a–d, tables with the results of the full parametric sweep for different heater widths and heater spacings are shown. Figure 6a shows the temperature deviation between the highest and lowest temperature at the top of the chamber, i.e., the second H2O and COC interface (ΔTtopofchamber=Ttop,max−Ttop,min). Figure 6b shows the deviation between the highest and lowest temperature inside the chamber, i.e., between the two COC and H2O interfaces (ΔTacrosschamber=Tbottom,max−Ttop,min). Figure 6c shows the temperature deviation between the highest and lowest temperature at the bottom of the chamber, i.e., the first COC and H2O interface (ΔTbottomofchamber=Tbot,max−Tbot,min). Figure 6d shows the deviation between the set heater temperature of 30 °C and the lowest temperature at the top of the chamber, i.e., the second H2O and COC interface (ΔTdeviationfromsetT=Theater−Ttop,min). As can be seen from the results in Figure 6, a combination of small heater widths and heater spacings will result in smaller temperature differences inside the reaction mixture. This is evident as smaller heater spacings will result in a better coverage of the heated area by heater material. The smaller heater widths will result in a smaller heater cross-sectional area, and thus can be operated at lower powers, as is evident from Equation (1). Resulting in the fact that a densely packed meander structure with small heater widths and small heater spacings can dissipate more heat into the system.\nBased on these results and its simplicity, a meandering heater pattern of a heater with a width of 0.3 mm and a spacing of 0.3 mm in between the lines is designed. A side note on the chosen heater width and heater spacing is that according to the simulations, the temperature differences within the chamber are less than ±0.3 °C for the most unfavorable dimensions. This temperature difference is still well-accepted in the temperature window in which the MDA reaction takes place (25 °C to 35 °C). However, as pointed out, a smaller cross-sectional area will result in a lower power consumption and therefore these dimensions are chosen. It is known that a meandering heater structure does not give the optimal temperature distribution over the device [26]. Therefore, the heater lines are longer than the width of the reaction chamber, and thus also covering the bulk material outside the chamber in order to improve the temperature uniformity inside the reaction mixture.\nThe heater pattern is divided over two shadow masks to minimize the length of the narrow Mo tracks in between the meandering structure. This prevents curvature due to intrinsic stresses. See Figure 7 for the outlines of both shadow masks, together with the resulting pattern on COC. The use of two shadow masks will give a metal track in which small parts has the double thickness. Here, the temperature will be lower. The system is designed such that these thicker parts are outside the reaction chamber and temperature control chamber region.\n\n3.2. Fabrication\n\nMilling and Optical Transparency\nThe milling increased the surface roughness of the COC plates also increases the surface area. Inhibition of the amplification can be caused by large surface areas as the used chemicals have more surface to have interaction with [44]. The created surface roughness is visualized using a FEI Sirion high resolution scanning electron microscope (HR-SEM) (FEI Company, Hillsboro, OR, USA) and measured using a Bruker Icon Dimension AFM in tapping mode with Bruker Tespa-V2 cantilevers (Bruker Nano Surfaces, Santa Barbara, CA, USA) and Gwyddion 2.52 open source freeware [62]. The results are shown in Figure 8. The surface roughness of pristine COC had a RRMS of 3.5 nm. This increased two orders of magnitude after milling (RRMS of 310.1 nm). With the reported surface treatment [44,59] we were capable of decreasing the surface roughness to a value even lower than that of pristine COC and the lowest reported in literature (RRMS of 0.9 nm). For this grade of COC (TOPAS 6017) it worked the best to do four short exposures of 5 s, with N2 blow drying after each exposure, instead of one longer exposure, as is more common in other grades of COC [44,59]. The difference in duration for the cyclohexane vapor post-treatment can be explained by the different ratios of the copolymers present in each grade. As the grade number increase, the ratio changes towards more norbornene monomers and less linear ethene monomers. The norbornene is more apolar due to the bridged cyclic hydrocarbon present in its molecular structure and therefore, will dissolve faster in non-polar solvents, like cyclohexane (vapor).\nLowering the surface roughness also increased the optical transmittance fivefold. Transmittance measurements in the visible range are done using a Woollam M-2000UI ellipsometer (J.A. Woollam Co., Lincoln, NE, USA). The results can be seen in Figure 9 and Figure 10. Having a high optical transparency in the visible range can be desired when in situ fluorescence detection will be implemented (e.g., EvaGreen fluorescence dye has an excitation wavelength of 500 nm and emission wavelength of 525 nm [63]). However, as in situ fluorescence detection is not used yet in this system and can also be done through the transparent PCR plate sealing foil, no further effort is put into optimizing this procedure to get even better optical transmittance.\n\n3.3. Metal Adhesion\nTo get reliable heaters, four possible options are investigated for their adhesion properties to the COC substrate. The adhesion of Au and Pt deposited by either evaporation or DC magnetron sputtering is investigated using the Scotch tape test [60,61] before and after temperature cycling up to 100 °C. Test patterns consisting of rectangular metal strips of 2 mm by 14 mm are fabricated by depositing 100 nm of metal using a hand-made shadow mask made out of DuPont Kapton® HN polyimide film of 0.05 mm thickness (RS Components B.V., Haarlem, The Netherlands). See Table 4 for the results of the Scotch tape test.\nNormally, heating up a glass or Si substrate with thin metal strips while measuring the resistance (RT) in these metal strips at certain temperature intervals (T) yields directly a linear relation, which can be fitted with RT/R0=1+αT−T0 [64], in which α is the the temperature coefficient of resistance (TCR) value. The thin-film TCR values have to be measured as they differ from the bulk TCR values due to its dependency on layer purity, grain size, and deposition method [65,66]. Belser and Hicklin also lists other attributes, such as surface roughness, porosity, and adsorbed materials present in or on the substrate which could influence the TCR value [64]. The bulk TCR values are 0.0034 K−1 and 0.0037 K−1 for Au and Pt [67].\nThe TCR characterizations of the metal strips on a COC substrate did not yield trustworthy TCR values at the first cycle. The first temperature cycle can be seen as a kind of thermal annealing, and therefore gives an hysteresis in the graphs, as can be seen in Figure A2 in Appendix C.1. After this first cycle, the values more or less show the linear behavior. The resulting TCR of this linear part is in agreement with the TCR ranges of Belser and Hicklin [64] and is given in Table 4. Belser and Hicklin used for their experiments substrates with coefficients of linear thermal expansion lower than 1.2 × 10−5 °C−1 [64]. The coefficient of linear thermal expansion for Au and Pt are 1.42 × 10−5 K−1 and 0.88 × 10−5 K−1, respectively [68]. COC of the grade TOPAS 6017 has a coefficient of linear thermal expansion of 6.0 × 10−5 K−1 [42]. This mismatch in coefficients of linear thermal expansion can give strain in the metal layers. Both Au [69,70,71] and Pt [72,73,74] are used as strain-sensitive gauges, and thus are sensitive to strain-induced geometry changes due to thermal expansion.\nAnother effect influencing the TCR value of the metal layer is aging. As can be seen in Figure A3 in Appendix C.2, the TCR value already changes after two weeks storing in ambient conditions. This could be due to adsorbed materials present on the surface [64].\nHowever, in this device, the TCR is not of importance as the metal structure will not be used as temperature sensor. Real-time temperature sensing is done using a thermocouple in the temperature monitor chamber. The resistance of the heater structure changes with temperature; thus, the dissipated power changes when a fixed voltage or current is used. However, the results in Section 3.4 show a 25 h stability test with a constant input potential and only a ±1.5 °C deviation. The TCR can become more important when other (higher) temperatures are required for the amplification.\nBased on the results in Table 4, the choice of heater material and deposition method to be used in the actual device is Au deposited using sputtering. Sputtering is an industrial-scale technique that is already being used in, for example, the car mirror and headlight industry [75].\n\n3.4. Chip Functioning\nCharacterization of the actual heat distribution is done using a FLIR One Pro iOS thermal camera (FLIR Systems, Inc., Wilsonville, OR, USA). Thermal images of the heat distribution are made at the side of the substrate without the resistor, whereas different input powers are used to heat up the heater. Au reflects the infrared radiation of the environment directly, therefore an image with the resistor facing the camera would give a heat map of the surrounding and not of the real temperature of the heater. These measurements also gives a better insight of the heat distribution inside the reaction chamber. The images are processed using the FLIR postprocessing freeware. Results of these measurements are shown in Figure 11a,b. The results are in good agreement with the estimations in Table 1. The slight deviation between the values can be explained by the fact that the heated area in the calculations had an assumed value, the thermal camera measurements used 1.5 mm thick COC substrates without a water-filled chamber, the actual resistors have small parts wich have a double thickness due to the two used shadow masks, and rounding of the values used in the calculations.\nThe reliability of the heater is tested by inserting the thermocouple into the temperature control chamber (see Figure 3a). A constant input potential of 4 V is applied using the Keithley source and the temperature is measured for 25 h. This exceeds the required operation time at least twelve-fold, meaning that it is a good indication for the reliability of the heater and thermocouple. The results are shown in Figure 11c.\nTo perform on-chip amplifications, the resistive heater on the chip is connected to the Keithley source using crocodile connections and the thermocouple is inserted in the temperature control chamber and connected to a Tenma 72-7715 Thermometer (see Figure 12).\n\n3.5. DNA Amplification\nFirst, to determine the temperature window of operation, MDA reactions are performed at 25 °C and 30 °C using the Illustra GenomiPhi V2 DNA amplification kit and EvaGreen fluorescence dye. From the literature, we know that this reaction does not work above 35 °C due to degradation of the protein activity in presence of a substrate [44]. In Figure 13, a graph of the fluorescence signal during MDA reactions at 25 °C and 30 °C, together with their non template control (NTC) is shown. These reactions are carried out in a conventional Bio-Rad CFX96 Touch Real-Time PCR machine (Bio-Rad Laboratories, Inc., Hercules, CA, USA) and the results show that the chosen proof-of-principle DNA amplification reaction is temperature dependent to some extent, but that there is a wide range of temperatures at which the amplification can be performed, i.e., 25°C to 35°C. This makes the functioning of the integrated resistive heater less critical than the stability shown in Figure 11c.\nMDA reactions are also performed inside an Eppendorf tube (Eppendorf AG, Hamburg, Germany) and inside the chip, again using the Illustra GenomiPhi V2 DNA amplification kit and EvaGreen fluorescence dye. As heat supply the water bath of an IKA Rotary Evaporator RV 8V (IKA-Werke, Staufen im Breisgau, Germany) is used. This water bath is according to its specification stable within a range of the set temperature ±0.1 °C. The chip and an Eppendorf tube are loaded with the reaction mixture containing the DNA sample and the EvaGreen dye solution. Here, the Eppendorf tube is serving as a control to show that the fabrication steps of the chips are not inhibiting the MDA reaction. The inlet and outlet of the chip are sealed with the Microseal “B” PCR plate sealing foil. The closed chip and tube are heated up in a separate water bath to 95 °C and kept at that temperature for 3 min to denaturate the dsDNA. Subsequently, the chip and tube are cooled down by placing it in an ice bath for 5 min after which the rest of the reagents are added. The complete mixtures are according to Table A3 in Appendix D. After closing the chip and tube again, they are placed in the water bath of the rotary evaporater and left there for 90 min, after which the reaction is terminated at 65 °C.\nThe MDA is also performed inside the chip, but with the integrated Au resistive heater serving as heat source. The set up shown schematically in Figure 12. The same procedure is followed as with the water bath heated test. Denaturation is done in a separate water bath. The heater is driven by an input potential of 3.2 V to get to a temperature of 30 °C and at the end of the reaction, the system is heated up to 65 °C by applying a potential of 9.2 V in order to terminate the amplification. In Figure 14 the logged temperature during the amplification is shown.\nAfter the amplifications, the reaction mixtures are pipetted out of the chips and tubes and into 1 mL quartz cuvettes containing 55 μL MilliQ DI water (Merck Millipore, Burlington, MA, USA). Fluorescence measurements are done in a Horiba Scientific FluoroMax+ spectrofluorometer to verify each amplification. The mixture is excitated at a wavelength of 500 nm and the emission spectrum is measured at wavelengths from 510 nm to 550 nm (bounded EvaGreen dye has a peak at 525 nm [63]). The measured spectra are normalized by subtracting the background signal of a mixture containing only the reaction buffer, the sample buffer, EvaGreen, and DNA. No Enzyme was added to this mixture, therefore no amplification could take place. See Figure 15 for the results obtained in the Eppendorf tube and chips. Figure A4 in Appendix E shows the background signal which is subtracted from all measurements.\nAs can be seen in Figure 15, the spectra of the amplification performed inside the chip, and by applying heat with the water bath as well as with the integrated Au-resistive heater, show the same trend as the amplification performed in the Eppendorf and heated by water bath. There is an order of magnitude difference in the fluorescence signal. However, the fluorescence intensity cannot be used as a value to quantify the amount of DNA. EvaGreen is a bis-intercalating cyanine fluorescence dye consisting of two monomeric DNA-binding dyes which are linked by a flexible spacer. These two DNA-binding dyes bind each in between two base pairs, which make them simple and fast, but also nonuniform and non-specific [44,63]. However, with this dye, a simple yes-or-no answer can be obtained if the amplification took place, as can be seen in Figure 15."}
LitCovid-PD-UBERON
{"project":"LitCovid-PD-UBERON","denotations":[{"id":"T5","span":{"begin":6160,"end":6164},"obj":"Body_part"},{"id":"T6","span":{"begin":9197,"end":9202},"obj":"Body_part"},{"id":"T7","span":{"begin":12251,"end":12255},"obj":"Body_part"},{"id":"T8","span":{"begin":12646,"end":12650},"obj":"Body_part"},{"id":"T9","span":{"begin":12765,"end":12769},"obj":"Body_part"},{"id":"T10","span":{"begin":12990,"end":12994},"obj":"Body_part"},{"id":"T11","span":{"begin":13134,"end":13138},"obj":"Body_part"},{"id":"T12","span":{"begin":13332,"end":13336},"obj":"Body_part"},{"id":"T13","span":{"begin":14828,"end":14832},"obj":"Body_part"}],"attributes":[{"id":"A5","pred":"uberon_id","subj":"T5","obj":"http://purl.obolibrary.org/obo/UBERON_0002398"},{"id":"A6","pred":"uberon_id","subj":"T6","obj":"http://purl.obolibrary.org/obo/UBERON_0002542"},{"id":"A7","pred":"uberon_id","subj":"T7","obj":"http://purl.obolibrary.org/obo/UBERON_0000025"},{"id":"A8","pred":"uberon_id","subj":"T8","obj":"http://purl.obolibrary.org/obo/UBERON_0000025"},{"id":"A9","pred":"uberon_id","subj":"T9","obj":"http://purl.obolibrary.org/obo/UBERON_0000025"},{"id":"A10","pred":"uberon_id","subj":"T10","obj":"http://purl.obolibrary.org/obo/UBERON_0000025"},{"id":"A11","pred":"uberon_id","subj":"T11","obj":"http://purl.obolibrary.org/obo/UBERON_0000025"},{"id":"A12","pred":"uberon_id","subj":"T12","obj":"http://purl.obolibrary.org/obo/UBERON_0000025"},{"id":"A13","pred":"uberon_id","subj":"T13","obj":"http://purl.obolibrary.org/obo/UBERON_0000025"}],"text":"3. Results and Discussion\n\n3.1. COMSOL MultiPhysics Simulation Results\nIn Figure 5, the results of heat transfer simulations of two different heater spacings are shown. The heater width for both geometries is 0.3 mm, while the heater spacing in Figure 5b,c are 0.3 mm and 2.0 mm, respectively. In Figure 6a–d, tables with the results of the full parametric sweep for different heater widths and heater spacings are shown. Figure 6a shows the temperature deviation between the highest and lowest temperature at the top of the chamber, i.e., the second H2O and COC interface (ΔTtopofchamber=Ttop,max−Ttop,min). Figure 6b shows the deviation between the highest and lowest temperature inside the chamber, i.e., between the two COC and H2O interfaces (ΔTacrosschamber=Tbottom,max−Ttop,min). Figure 6c shows the temperature deviation between the highest and lowest temperature at the bottom of the chamber, i.e., the first COC and H2O interface (ΔTbottomofchamber=Tbot,max−Tbot,min). Figure 6d shows the deviation between the set heater temperature of 30 °C and the lowest temperature at the top of the chamber, i.e., the second H2O and COC interface (ΔTdeviationfromsetT=Theater−Ttop,min). As can be seen from the results in Figure 6, a combination of small heater widths and heater spacings will result in smaller temperature differences inside the reaction mixture. This is evident as smaller heater spacings will result in a better coverage of the heated area by heater material. The smaller heater widths will result in a smaller heater cross-sectional area, and thus can be operated at lower powers, as is evident from Equation (1). Resulting in the fact that a densely packed meander structure with small heater widths and small heater spacings can dissipate more heat into the system.\nBased on these results and its simplicity, a meandering heater pattern of a heater with a width of 0.3 mm and a spacing of 0.3 mm in between the lines is designed. A side note on the chosen heater width and heater spacing is that according to the simulations, the temperature differences within the chamber are less than ±0.3 °C for the most unfavorable dimensions. This temperature difference is still well-accepted in the temperature window in which the MDA reaction takes place (25 °C to 35 °C). However, as pointed out, a smaller cross-sectional area will result in a lower power consumption and therefore these dimensions are chosen. It is known that a meandering heater structure does not give the optimal temperature distribution over the device [26]. Therefore, the heater lines are longer than the width of the reaction chamber, and thus also covering the bulk material outside the chamber in order to improve the temperature uniformity inside the reaction mixture.\nThe heater pattern is divided over two shadow masks to minimize the length of the narrow Mo tracks in between the meandering structure. This prevents curvature due to intrinsic stresses. See Figure 7 for the outlines of both shadow masks, together with the resulting pattern on COC. The use of two shadow masks will give a metal track in which small parts has the double thickness. Here, the temperature will be lower. The system is designed such that these thicker parts are outside the reaction chamber and temperature control chamber region.\n\n3.2. Fabrication\n\nMilling and Optical Transparency\nThe milling increased the surface roughness of the COC plates also increases the surface area. Inhibition of the amplification can be caused by large surface areas as the used chemicals have more surface to have interaction with [44]. The created surface roughness is visualized using a FEI Sirion high resolution scanning electron microscope (HR-SEM) (FEI Company, Hillsboro, OR, USA) and measured using a Bruker Icon Dimension AFM in tapping mode with Bruker Tespa-V2 cantilevers (Bruker Nano Surfaces, Santa Barbara, CA, USA) and Gwyddion 2.52 open source freeware [62]. The results are shown in Figure 8. The surface roughness of pristine COC had a RRMS of 3.5 nm. This increased two orders of magnitude after milling (RRMS of 310.1 nm). With the reported surface treatment [44,59] we were capable of decreasing the surface roughness to a value even lower than that of pristine COC and the lowest reported in literature (RRMS of 0.9 nm). For this grade of COC (TOPAS 6017) it worked the best to do four short exposures of 5 s, with N2 blow drying after each exposure, instead of one longer exposure, as is more common in other grades of COC [44,59]. The difference in duration for the cyclohexane vapor post-treatment can be explained by the different ratios of the copolymers present in each grade. As the grade number increase, the ratio changes towards more norbornene monomers and less linear ethene monomers. The norbornene is more apolar due to the bridged cyclic hydrocarbon present in its molecular structure and therefore, will dissolve faster in non-polar solvents, like cyclohexane (vapor).\nLowering the surface roughness also increased the optical transmittance fivefold. Transmittance measurements in the visible range are done using a Woollam M-2000UI ellipsometer (J.A. Woollam Co., Lincoln, NE, USA). The results can be seen in Figure 9 and Figure 10. Having a high optical transparency in the visible range can be desired when in situ fluorescence detection will be implemented (e.g., EvaGreen fluorescence dye has an excitation wavelength of 500 nm and emission wavelength of 525 nm [63]). However, as in situ fluorescence detection is not used yet in this system and can also be done through the transparent PCR plate sealing foil, no further effort is put into optimizing this procedure to get even better optical transmittance.\n\n3.3. Metal Adhesion\nTo get reliable heaters, four possible options are investigated for their adhesion properties to the COC substrate. The adhesion of Au and Pt deposited by either evaporation or DC magnetron sputtering is investigated using the Scotch tape test [60,61] before and after temperature cycling up to 100 °C. Test patterns consisting of rectangular metal strips of 2 mm by 14 mm are fabricated by depositing 100 nm of metal using a hand-made shadow mask made out of DuPont Kapton® HN polyimide film of 0.05 mm thickness (RS Components B.V., Haarlem, The Netherlands). See Table 4 for the results of the Scotch tape test.\nNormally, heating up a glass or Si substrate with thin metal strips while measuring the resistance (RT) in these metal strips at certain temperature intervals (T) yields directly a linear relation, which can be fitted with RT/R0=1+αT−T0 [64], in which α is the the temperature coefficient of resistance (TCR) value. The thin-film TCR values have to be measured as they differ from the bulk TCR values due to its dependency on layer purity, grain size, and deposition method [65,66]. Belser and Hicklin also lists other attributes, such as surface roughness, porosity, and adsorbed materials present in or on the substrate which could influence the TCR value [64]. The bulk TCR values are 0.0034 K−1 and 0.0037 K−1 for Au and Pt [67].\nThe TCR characterizations of the metal strips on a COC substrate did not yield trustworthy TCR values at the first cycle. The first temperature cycle can be seen as a kind of thermal annealing, and therefore gives an hysteresis in the graphs, as can be seen in Figure A2 in Appendix C.1. After this first cycle, the values more or less show the linear behavior. The resulting TCR of this linear part is in agreement with the TCR ranges of Belser and Hicklin [64] and is given in Table 4. Belser and Hicklin used for their experiments substrates with coefficients of linear thermal expansion lower than 1.2 × 10−5 °C−1 [64]. The coefficient of linear thermal expansion for Au and Pt are 1.42 × 10−5 K−1 and 0.88 × 10−5 K−1, respectively [68]. COC of the grade TOPAS 6017 has a coefficient of linear thermal expansion of 6.0 × 10−5 K−1 [42]. This mismatch in coefficients of linear thermal expansion can give strain in the metal layers. Both Au [69,70,71] and Pt [72,73,74] are used as strain-sensitive gauges, and thus are sensitive to strain-induced geometry changes due to thermal expansion.\nAnother effect influencing the TCR value of the metal layer is aging. As can be seen in Figure A3 in Appendix C.2, the TCR value already changes after two weeks storing in ambient conditions. This could be due to adsorbed materials present on the surface [64].\nHowever, in this device, the TCR is not of importance as the metal structure will not be used as temperature sensor. Real-time temperature sensing is done using a thermocouple in the temperature monitor chamber. The resistance of the heater structure changes with temperature; thus, the dissipated power changes when a fixed voltage or current is used. However, the results in Section 3.4 show a 25 h stability test with a constant input potential and only a ±1.5 °C deviation. The TCR can become more important when other (higher) temperatures are required for the amplification.\nBased on the results in Table 4, the choice of heater material and deposition method to be used in the actual device is Au deposited using sputtering. Sputtering is an industrial-scale technique that is already being used in, for example, the car mirror and headlight industry [75].\n\n3.4. Chip Functioning\nCharacterization of the actual heat distribution is done using a FLIR One Pro iOS thermal camera (FLIR Systems, Inc., Wilsonville, OR, USA). Thermal images of the heat distribution are made at the side of the substrate without the resistor, whereas different input powers are used to heat up the heater. Au reflects the infrared radiation of the environment directly, therefore an image with the resistor facing the camera would give a heat map of the surrounding and not of the real temperature of the heater. These measurements also gives a better insight of the heat distribution inside the reaction chamber. The images are processed using the FLIR postprocessing freeware. Results of these measurements are shown in Figure 11a,b. The results are in good agreement with the estimations in Table 1. The slight deviation between the values can be explained by the fact that the heated area in the calculations had an assumed value, the thermal camera measurements used 1.5 mm thick COC substrates without a water-filled chamber, the actual resistors have small parts wich have a double thickness due to the two used shadow masks, and rounding of the values used in the calculations.\nThe reliability of the heater is tested by inserting the thermocouple into the temperature control chamber (see Figure 3a). A constant input potential of 4 V is applied using the Keithley source and the temperature is measured for 25 h. This exceeds the required operation time at least twelve-fold, meaning that it is a good indication for the reliability of the heater and thermocouple. The results are shown in Figure 11c.\nTo perform on-chip amplifications, the resistive heater on the chip is connected to the Keithley source using crocodile connections and the thermocouple is inserted in the temperature control chamber and connected to a Tenma 72-7715 Thermometer (see Figure 12).\n\n3.5. DNA Amplification\nFirst, to determine the temperature window of operation, MDA reactions are performed at 25 °C and 30 °C using the Illustra GenomiPhi V2 DNA amplification kit and EvaGreen fluorescence dye. From the literature, we know that this reaction does not work above 35 °C due to degradation of the protein activity in presence of a substrate [44]. In Figure 13, a graph of the fluorescence signal during MDA reactions at 25 °C and 30 °C, together with their non template control (NTC) is shown. These reactions are carried out in a conventional Bio-Rad CFX96 Touch Real-Time PCR machine (Bio-Rad Laboratories, Inc., Hercules, CA, USA) and the results show that the chosen proof-of-principle DNA amplification reaction is temperature dependent to some extent, but that there is a wide range of temperatures at which the amplification can be performed, i.e., 25°C to 35°C. This makes the functioning of the integrated resistive heater less critical than the stability shown in Figure 11c.\nMDA reactions are also performed inside an Eppendorf tube (Eppendorf AG, Hamburg, Germany) and inside the chip, again using the Illustra GenomiPhi V2 DNA amplification kit and EvaGreen fluorescence dye. As heat supply the water bath of an IKA Rotary Evaporator RV 8V (IKA-Werke, Staufen im Breisgau, Germany) is used. This water bath is according to its specification stable within a range of the set temperature ±0.1 °C. The chip and an Eppendorf tube are loaded with the reaction mixture containing the DNA sample and the EvaGreen dye solution. Here, the Eppendorf tube is serving as a control to show that the fabrication steps of the chips are not inhibiting the MDA reaction. The inlet and outlet of the chip are sealed with the Microseal “B” PCR plate sealing foil. The closed chip and tube are heated up in a separate water bath to 95 °C and kept at that temperature for 3 min to denaturate the dsDNA. Subsequently, the chip and tube are cooled down by placing it in an ice bath for 5 min after which the rest of the reagents are added. The complete mixtures are according to Table A3 in Appendix D. After closing the chip and tube again, they are placed in the water bath of the rotary evaporater and left there for 90 min, after which the reaction is terminated at 65 °C.\nThe MDA is also performed inside the chip, but with the integrated Au resistive heater serving as heat source. The set up shown schematically in Figure 12. The same procedure is followed as with the water bath heated test. Denaturation is done in a separate water bath. The heater is driven by an input potential of 3.2 V to get to a temperature of 30 °C and at the end of the reaction, the system is heated up to 65 °C by applying a potential of 9.2 V in order to terminate the amplification. In Figure 14 the logged temperature during the amplification is shown.\nAfter the amplifications, the reaction mixtures are pipetted out of the chips and tubes and into 1 mL quartz cuvettes containing 55 μL MilliQ DI water (Merck Millipore, Burlington, MA, USA). Fluorescence measurements are done in a Horiba Scientific FluoroMax+ spectrofluorometer to verify each amplification. The mixture is excitated at a wavelength of 500 nm and the emission spectrum is measured at wavelengths from 510 nm to 550 nm (bounded EvaGreen dye has a peak at 525 nm [63]). The measured spectra are normalized by subtracting the background signal of a mixture containing only the reaction buffer, the sample buffer, EvaGreen, and DNA. No Enzyme was added to this mixture, therefore no amplification could take place. See Figure 15 for the results obtained in the Eppendorf tube and chips. Figure A4 in Appendix E shows the background signal which is subtracted from all measurements.\nAs can be seen in Figure 15, the spectra of the amplification performed inside the chip, and by applying heat with the water bath as well as with the integrated Au-resistive heater, show the same trend as the amplification performed in the Eppendorf and heated by water bath. There is an order of magnitude difference in the fluorescence signal. However, the fluorescence intensity cannot be used as a value to quantify the amount of DNA. EvaGreen is a bis-intercalating cyanine fluorescence dye consisting of two monomeric DNA-binding dyes which are linked by a flexible spacer. These two DNA-binding dyes bind each in between two base pairs, which make them simple and fast, but also nonuniform and non-specific [44,63]. However, with this dye, a simple yes-or-no answer can be obtained if the amplification took place, as can be seen in Figure 15."}
LitCovid-PD-MONDO
{"project":"LitCovid-PD-MONDO","denotations":[{"id":"T31","span":{"begin":4013,"end":4017},"obj":"Disease"},{"id":"T32","span":{"begin":4083,"end":4087},"obj":"Disease"},{"id":"T33","span":{"begin":4285,"end":4289},"obj":"Disease"},{"id":"T34","span":{"begin":6249,"end":6251},"obj":"Disease"},{"id":"T35","span":{"begin":14186,"end":14188},"obj":"Disease"}],"attributes":[{"id":"A31","pred":"mondo_id","subj":"T31","obj":"http://purl.obolibrary.org/obo/MONDO_0005314"},{"id":"A32","pred":"mondo_id","subj":"T32","obj":"http://purl.obolibrary.org/obo/MONDO_0005314"},{"id":"A33","pred":"mondo_id","subj":"T33","obj":"http://purl.obolibrary.org/obo/MONDO_0005314"},{"id":"A34","pred":"mondo_id","subj":"T34","obj":"http://purl.obolibrary.org/obo/MONDO_0010725"},{"id":"A35","pred":"mondo_id","subj":"T35","obj":"http://purl.obolibrary.org/obo/MONDO_0018849"}],"text":"3. Results and Discussion\n\n3.1. COMSOL MultiPhysics Simulation Results\nIn Figure 5, the results of heat transfer simulations of two different heater spacings are shown. The heater width for both geometries is 0.3 mm, while the heater spacing in Figure 5b,c are 0.3 mm and 2.0 mm, respectively. In Figure 6a–d, tables with the results of the full parametric sweep for different heater widths and heater spacings are shown. Figure 6a shows the temperature deviation between the highest and lowest temperature at the top of the chamber, i.e., the second H2O and COC interface (ΔTtopofchamber=Ttop,max−Ttop,min). Figure 6b shows the deviation between the highest and lowest temperature inside the chamber, i.e., between the two COC and H2O interfaces (ΔTacrosschamber=Tbottom,max−Ttop,min). Figure 6c shows the temperature deviation between the highest and lowest temperature at the bottom of the chamber, i.e., the first COC and H2O interface (ΔTbottomofchamber=Tbot,max−Tbot,min). Figure 6d shows the deviation between the set heater temperature of 30 °C and the lowest temperature at the top of the chamber, i.e., the second H2O and COC interface (ΔTdeviationfromsetT=Theater−Ttop,min). As can be seen from the results in Figure 6, a combination of small heater widths and heater spacings will result in smaller temperature differences inside the reaction mixture. This is evident as smaller heater spacings will result in a better coverage of the heated area by heater material. The smaller heater widths will result in a smaller heater cross-sectional area, and thus can be operated at lower powers, as is evident from Equation (1). Resulting in the fact that a densely packed meander structure with small heater widths and small heater spacings can dissipate more heat into the system.\nBased on these results and its simplicity, a meandering heater pattern of a heater with a width of 0.3 mm and a spacing of 0.3 mm in between the lines is designed. A side note on the chosen heater width and heater spacing is that according to the simulations, the temperature differences within the chamber are less than ±0.3 °C for the most unfavorable dimensions. This temperature difference is still well-accepted in the temperature window in which the MDA reaction takes place (25 °C to 35 °C). However, as pointed out, a smaller cross-sectional area will result in a lower power consumption and therefore these dimensions are chosen. It is known that a meandering heater structure does not give the optimal temperature distribution over the device [26]. Therefore, the heater lines are longer than the width of the reaction chamber, and thus also covering the bulk material outside the chamber in order to improve the temperature uniformity inside the reaction mixture.\nThe heater pattern is divided over two shadow masks to minimize the length of the narrow Mo tracks in between the meandering structure. This prevents curvature due to intrinsic stresses. See Figure 7 for the outlines of both shadow masks, together with the resulting pattern on COC. The use of two shadow masks will give a metal track in which small parts has the double thickness. Here, the temperature will be lower. The system is designed such that these thicker parts are outside the reaction chamber and temperature control chamber region.\n\n3.2. Fabrication\n\nMilling and Optical Transparency\nThe milling increased the surface roughness of the COC plates also increases the surface area. Inhibition of the amplification can be caused by large surface areas as the used chemicals have more surface to have interaction with [44]. The created surface roughness is visualized using a FEI Sirion high resolution scanning electron microscope (HR-SEM) (FEI Company, Hillsboro, OR, USA) and measured using a Bruker Icon Dimension AFM in tapping mode with Bruker Tespa-V2 cantilevers (Bruker Nano Surfaces, Santa Barbara, CA, USA) and Gwyddion 2.52 open source freeware [62]. The results are shown in Figure 8. The surface roughness of pristine COC had a RRMS of 3.5 nm. This increased two orders of magnitude after milling (RRMS of 310.1 nm). With the reported surface treatment [44,59] we were capable of decreasing the surface roughness to a value even lower than that of pristine COC and the lowest reported in literature (RRMS of 0.9 nm). For this grade of COC (TOPAS 6017) it worked the best to do four short exposures of 5 s, with N2 blow drying after each exposure, instead of one longer exposure, as is more common in other grades of COC [44,59]. The difference in duration for the cyclohexane vapor post-treatment can be explained by the different ratios of the copolymers present in each grade. As the grade number increase, the ratio changes towards more norbornene monomers and less linear ethene monomers. The norbornene is more apolar due to the bridged cyclic hydrocarbon present in its molecular structure and therefore, will dissolve faster in non-polar solvents, like cyclohexane (vapor).\nLowering the surface roughness also increased the optical transmittance fivefold. Transmittance measurements in the visible range are done using a Woollam M-2000UI ellipsometer (J.A. Woollam Co., Lincoln, NE, USA). The results can be seen in Figure 9 and Figure 10. Having a high optical transparency in the visible range can be desired when in situ fluorescence detection will be implemented (e.g., EvaGreen fluorescence dye has an excitation wavelength of 500 nm and emission wavelength of 525 nm [63]). However, as in situ fluorescence detection is not used yet in this system and can also be done through the transparent PCR plate sealing foil, no further effort is put into optimizing this procedure to get even better optical transmittance.\n\n3.3. Metal Adhesion\nTo get reliable heaters, four possible options are investigated for their adhesion properties to the COC substrate. The adhesion of Au and Pt deposited by either evaporation or DC magnetron sputtering is investigated using the Scotch tape test [60,61] before and after temperature cycling up to 100 °C. Test patterns consisting of rectangular metal strips of 2 mm by 14 mm are fabricated by depositing 100 nm of metal using a hand-made shadow mask made out of DuPont Kapton® HN polyimide film of 0.05 mm thickness (RS Components B.V., Haarlem, The Netherlands). See Table 4 for the results of the Scotch tape test.\nNormally, heating up a glass or Si substrate with thin metal strips while measuring the resistance (RT) in these metal strips at certain temperature intervals (T) yields directly a linear relation, which can be fitted with RT/R0=1+αT−T0 [64], in which α is the the temperature coefficient of resistance (TCR) value. The thin-film TCR values have to be measured as they differ from the bulk TCR values due to its dependency on layer purity, grain size, and deposition method [65,66]. Belser and Hicklin also lists other attributes, such as surface roughness, porosity, and adsorbed materials present in or on the substrate which could influence the TCR value [64]. The bulk TCR values are 0.0034 K−1 and 0.0037 K−1 for Au and Pt [67].\nThe TCR characterizations of the metal strips on a COC substrate did not yield trustworthy TCR values at the first cycle. The first temperature cycle can be seen as a kind of thermal annealing, and therefore gives an hysteresis in the graphs, as can be seen in Figure A2 in Appendix C.1. After this first cycle, the values more or less show the linear behavior. The resulting TCR of this linear part is in agreement with the TCR ranges of Belser and Hicklin [64] and is given in Table 4. Belser and Hicklin used for their experiments substrates with coefficients of linear thermal expansion lower than 1.2 × 10−5 °C−1 [64]. The coefficient of linear thermal expansion for Au and Pt are 1.42 × 10−5 K−1 and 0.88 × 10−5 K−1, respectively [68]. COC of the grade TOPAS 6017 has a coefficient of linear thermal expansion of 6.0 × 10−5 K−1 [42]. This mismatch in coefficients of linear thermal expansion can give strain in the metal layers. Both Au [69,70,71] and Pt [72,73,74] are used as strain-sensitive gauges, and thus are sensitive to strain-induced geometry changes due to thermal expansion.\nAnother effect influencing the TCR value of the metal layer is aging. As can be seen in Figure A3 in Appendix C.2, the TCR value already changes after two weeks storing in ambient conditions. This could be due to adsorbed materials present on the surface [64].\nHowever, in this device, the TCR is not of importance as the metal structure will not be used as temperature sensor. Real-time temperature sensing is done using a thermocouple in the temperature monitor chamber. The resistance of the heater structure changes with temperature; thus, the dissipated power changes when a fixed voltage or current is used. However, the results in Section 3.4 show a 25 h stability test with a constant input potential and only a ±1.5 °C deviation. The TCR can become more important when other (higher) temperatures are required for the amplification.\nBased on the results in Table 4, the choice of heater material and deposition method to be used in the actual device is Au deposited using sputtering. Sputtering is an industrial-scale technique that is already being used in, for example, the car mirror and headlight industry [75].\n\n3.4. Chip Functioning\nCharacterization of the actual heat distribution is done using a FLIR One Pro iOS thermal camera (FLIR Systems, Inc., Wilsonville, OR, USA). Thermal images of the heat distribution are made at the side of the substrate without the resistor, whereas different input powers are used to heat up the heater. Au reflects the infrared radiation of the environment directly, therefore an image with the resistor facing the camera would give a heat map of the surrounding and not of the real temperature of the heater. These measurements also gives a better insight of the heat distribution inside the reaction chamber. The images are processed using the FLIR postprocessing freeware. Results of these measurements are shown in Figure 11a,b. The results are in good agreement with the estimations in Table 1. The slight deviation between the values can be explained by the fact that the heated area in the calculations had an assumed value, the thermal camera measurements used 1.5 mm thick COC substrates without a water-filled chamber, the actual resistors have small parts wich have a double thickness due to the two used shadow masks, and rounding of the values used in the calculations.\nThe reliability of the heater is tested by inserting the thermocouple into the temperature control chamber (see Figure 3a). A constant input potential of 4 V is applied using the Keithley source and the temperature is measured for 25 h. This exceeds the required operation time at least twelve-fold, meaning that it is a good indication for the reliability of the heater and thermocouple. The results are shown in Figure 11c.\nTo perform on-chip amplifications, the resistive heater on the chip is connected to the Keithley source using crocodile connections and the thermocouple is inserted in the temperature control chamber and connected to a Tenma 72-7715 Thermometer (see Figure 12).\n\n3.5. DNA Amplification\nFirst, to determine the temperature window of operation, MDA reactions are performed at 25 °C and 30 °C using the Illustra GenomiPhi V2 DNA amplification kit and EvaGreen fluorescence dye. From the literature, we know that this reaction does not work above 35 °C due to degradation of the protein activity in presence of a substrate [44]. In Figure 13, a graph of the fluorescence signal during MDA reactions at 25 °C and 30 °C, together with their non template control (NTC) is shown. These reactions are carried out in a conventional Bio-Rad CFX96 Touch Real-Time PCR machine (Bio-Rad Laboratories, Inc., Hercules, CA, USA) and the results show that the chosen proof-of-principle DNA amplification reaction is temperature dependent to some extent, but that there is a wide range of temperatures at which the amplification can be performed, i.e., 25°C to 35°C. This makes the functioning of the integrated resistive heater less critical than the stability shown in Figure 11c.\nMDA reactions are also performed inside an Eppendorf tube (Eppendorf AG, Hamburg, Germany) and inside the chip, again using the Illustra GenomiPhi V2 DNA amplification kit and EvaGreen fluorescence dye. As heat supply the water bath of an IKA Rotary Evaporator RV 8V (IKA-Werke, Staufen im Breisgau, Germany) is used. This water bath is according to its specification stable within a range of the set temperature ±0.1 °C. The chip and an Eppendorf tube are loaded with the reaction mixture containing the DNA sample and the EvaGreen dye solution. Here, the Eppendorf tube is serving as a control to show that the fabrication steps of the chips are not inhibiting the MDA reaction. The inlet and outlet of the chip are sealed with the Microseal “B” PCR plate sealing foil. The closed chip and tube are heated up in a separate water bath to 95 °C and kept at that temperature for 3 min to denaturate the dsDNA. Subsequently, the chip and tube are cooled down by placing it in an ice bath for 5 min after which the rest of the reagents are added. The complete mixtures are according to Table A3 in Appendix D. After closing the chip and tube again, they are placed in the water bath of the rotary evaporater and left there for 90 min, after which the reaction is terminated at 65 °C.\nThe MDA is also performed inside the chip, but with the integrated Au resistive heater serving as heat source. The set up shown schematically in Figure 12. The same procedure is followed as with the water bath heated test. Denaturation is done in a separate water bath. The heater is driven by an input potential of 3.2 V to get to a temperature of 30 °C and at the end of the reaction, the system is heated up to 65 °C by applying a potential of 9.2 V in order to terminate the amplification. In Figure 14 the logged temperature during the amplification is shown.\nAfter the amplifications, the reaction mixtures are pipetted out of the chips and tubes and into 1 mL quartz cuvettes containing 55 μL MilliQ DI water (Merck Millipore, Burlington, MA, USA). Fluorescence measurements are done in a Horiba Scientific FluoroMax+ spectrofluorometer to verify each amplification. The mixture is excitated at a wavelength of 500 nm and the emission spectrum is measured at wavelengths from 510 nm to 550 nm (bounded EvaGreen dye has a peak at 525 nm [63]). The measured spectra are normalized by subtracting the background signal of a mixture containing only the reaction buffer, the sample buffer, EvaGreen, and DNA. No Enzyme was added to this mixture, therefore no amplification could take place. See Figure 15 for the results obtained in the Eppendorf tube and chips. Figure A4 in Appendix E shows the background signal which is subtracted from all measurements.\nAs can be seen in Figure 15, the spectra of the amplification performed inside the chip, and by applying heat with the water bath as well as with the integrated Au-resistive heater, show the same trend as the amplification performed in the Eppendorf and heated by water bath. There is an order of magnitude difference in the fluorescence signal. However, the fluorescence intensity cannot be used as a value to quantify the amount of DNA. EvaGreen is a bis-intercalating cyanine fluorescence dye consisting of two monomeric DNA-binding dyes which are linked by a flexible spacer. These two DNA-binding dyes bind each in between two base pairs, which make them simple and fast, but also nonuniform and non-specific [44,63]. However, with this dye, a simple yes-or-no answer can be obtained if the amplification took place, as can be seen in Figure 15."}
LitCovid-PD-CLO
{"project":"LitCovid-PD-CLO","denotations":[{"id":"T189","span":{"begin":1231,"end":1232},"obj":"http://purl.obolibrary.org/obo/CLO_0001020"},{"id":"T190","span":{"begin":1422,"end":1423},"obj":"http://purl.obolibrary.org/obo/CLO_0001020"},{"id":"T191","span":{"begin":1520,"end":1521},"obj":"http://purl.obolibrary.org/obo/CLO_0001020"},{"id":"T192","span":{"begin":1661,"end":1662},"obj":"http://purl.obolibrary.org/obo/CLO_0001020"},{"id":"T193","span":{"begin":1831,"end":1832},"obj":"http://purl.obolibrary.org/obo/CLO_0001020"},{"id":"T194","span":{"begin":1862,"end":1863},"obj":"http://purl.obolibrary.org/obo/CLO_0001020"},{"id":"T195","span":{"begin":1876,"end":1877},"obj":"http://purl.obolibrary.org/obo/CLO_0001020"},{"id":"T196","span":{"begin":1898,"end":1899},"obj":"http://purl.obolibrary.org/obo/CLO_0001020"},{"id":"T197","span":{"begin":1952,"end":1953},"obj":"http://purl.obolibrary.org/obo/CLO_0001020"},{"id":"T198","span":{"begin":2279,"end":2281},"obj":"http://purl.obolibrary.org/obo/CLO_0001000"},{"id":"T199","span":{"begin":2312,"end":2313},"obj":"http://purl.obolibrary.org/obo/CLO_0001020"},{"id":"T200","span":{"begin":2358,"end":2359},"obj":"http://purl.obolibrary.org/obo/CLO_0001020"},{"id":"T201","span":{"begin":2444,"end":2445},"obj":"http://purl.obolibrary.org/obo/CLO_0001020"},{"id":"T202","span":{"begin":2534,"end":2540},"obj":"http://purl.obolibrary.org/obo/OBI_0000968"},{"id":"T203","span":{"begin":2852,"end":2854},"obj":"http://purl.obolibrary.org/obo/CLO_0007815"},{"id":"T204","span":{"begin":3084,"end":3085},"obj":"http://purl.obolibrary.org/obo/CLO_0001020"},{"id":"T205","span":{"begin":3119,"end":3122},"obj":"http://purl.obolibrary.org/obo/CLO_0051582"},{"id":"T206","span":{"begin":3645,"end":3646},"obj":"http://purl.obolibrary.org/obo/CLO_0001020"},{"id":"T207","span":{"begin":3765,"end":3766},"obj":"http://purl.obolibrary.org/obo/CLO_0001020"},{"id":"T208","span":{"begin":4011,"end":4012},"obj":"http://purl.obolibrary.org/obo/CLO_0001020"},{"id":"T209","span":{"begin":4201,"end":4202},"obj":"http://purl.obolibrary.org/obo/CLO_0001020"},{"id":"T210","span":{"begin":5111,"end":5112},"obj":"http://purl.obolibrary.org/obo/CLO_0001020"},{"id":"T211","span":{"begin":5171,"end":5173},"obj":"http://purl.obolibrary.org/obo/CLO_0008149"},{"id":"T212","span":{"begin":5239,"end":5240},"obj":"http://purl.obolibrary.org/obo/CLO_0001020"},{"id":"T213","span":{"begin":5392,"end":5395},"obj":"http://purl.obolibrary.org/obo/CLO_0051582"},{"id":"T214","span":{"begin":5973,"end":5977},"obj":"http://purl.obolibrary.org/obo/UBERON_0000473"},{"id":"T215","span":{"begin":6037,"end":6041},"obj":"http://purl.obolibrary.org/obo/UBERON_0000473"},{"id":"T216","span":{"begin":6158,"end":6159},"obj":"http://purl.obolibrary.org/obo/CLO_0001020"},{"id":"T217","span":{"begin":6209,"end":6211},"obj":"http://purl.obolibrary.org/obo/CLO_0003788"},{"id":"T218","span":{"begin":6249,"end":6251},"obj":"http://purl.obolibrary.org/obo/CLO_0008882"},{"id":"T219","span":{"begin":6343,"end":6347},"obj":"http://purl.obolibrary.org/obo/UBERON_0000473"},{"id":"T220","span":{"begin":6370,"end":6371},"obj":"http://purl.obolibrary.org/obo/CLO_0001020"},{"id":"T221","span":{"begin":6528,"end":6529},"obj":"http://purl.obolibrary.org/obo/CLO_0001020"},{"id":"T222","span":{"begin":7044,"end":7047},"obj":"http://purl.obolibrary.org/obo/CLO_0007052"},{"id":"T223","span":{"begin":7059,"end":7062},"obj":"http://purl.obolibrary.org/obo/CLO_0007052"},{"id":"T224","span":{"begin":7074,"end":7080},"obj":"http://purl.obolibrary.org/obo/CLO_0008516"},{"id":"T225","span":{"begin":7132,"end":7133},"obj":"http://purl.obolibrary.org/obo/CLO_0001020"},{"id":"T226","span":{"begin":7248,"end":7249},"obj":"http://purl.obolibrary.org/obo/CLO_0001020"},{"id":"T227","span":{"begin":7351,"end":7353},"obj":"http://purl.obolibrary.org/obo/CLO_0001562"},{"id":"T228","span":{"begin":7366,"end":7369},"obj":"http://purl.obolibrary.org/obo/CLO_0051741"},{"id":"T229","span":{"begin":7697,"end":7700},"obj":"http://purl.obolibrary.org/obo/CLO_0051741"},{"id":"T230","span":{"begin":7781,"end":7784},"obj":"http://purl.obolibrary.org/obo/CLO_0007052"},{"id":"T231","span":{"begin":7801,"end":7804},"obj":"http://purl.obolibrary.org/obo/CLO_0007052"},{"id":"T232","span":{"begin":7853,"end":7856},"obj":"http://purl.obolibrary.org/obo/CLO_0051582"},{"id":"T233","span":{"begin":7857,"end":7858},"obj":"http://purl.obolibrary.org/obo/CLO_0001020"},{"id":"T234","span":{"begin":7913,"end":7916},"obj":"http://purl.obolibrary.org/obo/CLO_0007052"},{"id":"T235","span":{"begin":8271,"end":8273},"obj":"http://purl.obolibrary.org/obo/CLO_0001577"},{"id":"T236","span":{"begin":8286,"end":8289},"obj":"http://purl.obolibrary.org/obo/CLO_0002105"},{"id":"T237","span":{"begin":8286,"end":8289},"obj":"http://purl.obolibrary.org/obo/CLO_0051742"},{"id":"T238","span":{"begin":8454,"end":8460},"obj":"http://purl.obolibrary.org/obo/OBI_0000968"},{"id":"T239","span":{"begin":8598,"end":8599},"obj":"http://purl.obolibrary.org/obo/CLO_0001020"},{"id":"T240","span":{"begin":8754,"end":8755},"obj":"http://purl.obolibrary.org/obo/CLO_0001020"},{"id":"T241","span":{"begin":8831,"end":8832},"obj":"http://purl.obolibrary.org/obo/CLO_0001020"},{"id":"T242","span":{"begin":8848,"end":8852},"obj":"http://purl.obolibrary.org/obo/UBERON_0000473"},{"id":"T243","span":{"begin":8858,"end":8859},"obj":"http://purl.obolibrary.org/obo/CLO_0001020"},{"id":"T244","span":{"begin":8894,"end":8895},"obj":"http://purl.obolibrary.org/obo/CLO_0001020"},{"id":"T245","span":{"begin":9128,"end":9134},"obj":"http://purl.obolibrary.org/obo/OBI_0000968"},{"id":"T246","span":{"begin":9261,"end":9264},"obj":"http://purl.obolibrary.org/obo/CLO_0002199"},{"id":"T247","span":{"begin":9387,"end":9388},"obj":"http://purl.obolibrary.org/obo/CLO_0001020"},{"id":"T248","span":{"begin":9729,"end":9739},"obj":"http://purl.obolibrary.org/obo/UBERON_0001456"},{"id":"T249","span":{"begin":9758,"end":9759},"obj":"http://purl.obolibrary.org/obo/CLO_0001020"},{"id":"T250","span":{"begin":9865,"end":9866},"obj":"http://purl.obolibrary.org/obo/CLO_0001020"},{"id":"T251","span":{"begin":10055,"end":10056},"obj":"http://purl.obolibrary.org/obo/CLO_0001021"},{"id":"T252","span":{"begin":10330,"end":10331},"obj":"http://purl.obolibrary.org/obo/CLO_0001020"},{"id":"T253","span":{"begin":10402,"end":10403},"obj":"http://purl.obolibrary.org/obo/CLO_0001020"},{"id":"T254","span":{"begin":10541,"end":10547},"obj":"http://purl.obolibrary.org/obo/UBERON_0000473"},{"id":"T255","span":{"begin":10632,"end":10633},"obj":"http://purl.obolibrary.org/obo/CLO_0001020"},{"id":"T256","span":{"begin":10827,"end":10828},"obj":"http://purl.obolibrary.org/obo/CLO_0001020"},{"id":"T257","span":{"begin":11151,"end":11152},"obj":"http://purl.obolibrary.org/obo/CLO_0001020"},{"id":"T258","span":{"begin":11477,"end":11479},"obj":"http://purl.obolibrary.org/obo/CLO_0001000"},{"id":"T259","span":{"begin":11517,"end":11525},"obj":"http://purl.obolibrary.org/obo/CLO_0001658"},{"id":"T260","span":{"begin":11541,"end":11542},"obj":"http://purl.obolibrary.org/obo/CLO_0001020"},{"id":"T261","span":{"begin":11573,"end":11574},"obj":"http://purl.obolibrary.org/obo/CLO_0001020"},{"id":"T262","span":{"begin":11601,"end":11607},"obj":"http://purl.obolibrary.org/obo/SO_0000418"},{"id":"T263","span":{"begin":11741,"end":11742},"obj":"http://purl.obolibrary.org/obo/CLO_0001020"},{"id":"T264","span":{"begin":11988,"end":11989},"obj":"http://purl.obolibrary.org/obo/CLO_0001020"},{"id":"T265","span":{"begin":12076,"end":12078},"obj":"http://purl.obolibrary.org/obo/CLO_0001000"},{"id":"T266","span":{"begin":12251,"end":12255},"obj":"http://purl.obolibrary.org/obo/UBERON_0000025"},{"id":"T267","span":{"begin":12485,"end":12487},"obj":"http://purl.obolibrary.org/obo/UBERON_0003064"},{"id":"T268","span":{"begin":12580,"end":12581},"obj":"http://purl.obolibrary.org/obo/CLO_0001020"},{"id":"T269","span":{"begin":12646,"end":12650},"obj":"http://purl.obolibrary.org/obo/UBERON_0000025"},{"id":"T270","span":{"begin":12765,"end":12769},"obj":"http://purl.obolibrary.org/obo/UBERON_0000025"},{"id":"T271","span":{"begin":12784,"end":12785},"obj":"http://purl.obolibrary.org/obo/CLO_0001020"},{"id":"T272","span":{"begin":12943,"end":12944},"obj":"http://purl.obolibrary.org/obo/CLO_0001021"},{"id":"T273","span":{"begin":12990,"end":12994},"obj":"http://purl.obolibrary.org/obo/UBERON_0000025"},{"id":"T274","span":{"begin":13012,"end":13013},"obj":"http://purl.obolibrary.org/obo/CLO_0001020"},{"id":"T275","span":{"begin":13134,"end":13138},"obj":"http://purl.obolibrary.org/obo/UBERON_0000025"},{"id":"T276","span":{"begin":13287,"end":13289},"obj":"http://purl.obolibrary.org/obo/CLO_0001577"},{"id":"T277","span":{"begin":13332,"end":13336},"obj":"http://purl.obolibrary.org/obo/UBERON_0000025"},{"id":"T278","span":{"begin":13696,"end":13700},"obj":"http://purl.obolibrary.org/obo/UBERON_0000473"},{"id":"T279","span":{"begin":13726,"end":13727},"obj":"http://purl.obolibrary.org/obo/CLO_0001020"},{"id":"T280","span":{"begin":13811,"end":13812},"obj":"http://purl.obolibrary.org/obo/CLO_0001020"},{"id":"T281","span":{"begin":13911,"end":13912},"obj":"http://purl.obolibrary.org/obo/CLO_0001020"},{"id":"T282","span":{"begin":14126,"end":14131},"obj":"http://purl.obolibrary.org/obo/UBERON_0000025"},{"id":"T283","span":{"begin":14273,"end":14274},"obj":"http://purl.obolibrary.org/obo/CLO_0001020"},{"id":"T284","span":{"begin":14381,"end":14382},"obj":"http://purl.obolibrary.org/obo/CLO_0001020"},{"id":"T285","span":{"begin":14501,"end":14504},"obj":"http://purl.obolibrary.org/obo/CLO_0051582"},{"id":"T286","span":{"begin":14505,"end":14506},"obj":"http://purl.obolibrary.org/obo/CLO_0001020"},{"id":"T287","span":{"begin":14595,"end":14601},"obj":"http://purl.obolibrary.org/obo/SO_0000418"},{"id":"T288","span":{"begin":14605,"end":14606},"obj":"http://purl.obolibrary.org/obo/CLO_0001020"},{"id":"T289","span":{"begin":14828,"end":14832},"obj":"http://purl.obolibrary.org/obo/UBERON_0000025"},{"id":"T290","span":{"begin":14889,"end":14895},"obj":"http://purl.obolibrary.org/obo/SO_0000418"},{"id":"T291","span":{"begin":15277,"end":15283},"obj":"http://purl.obolibrary.org/obo/SO_0000418"},{"id":"T292","span":{"begin":15339,"end":15340},"obj":"http://purl.obolibrary.org/obo/CLO_0001020"},{"id":"T293","span":{"begin":15390,"end":15391},"obj":"http://purl.obolibrary.org/obo/CLO_0001020"},{"id":"T294","span":{"begin":15500,"end":15501},"obj":"http://purl.obolibrary.org/obo/CLO_0001020"},{"id":"T295","span":{"begin":15686,"end":15687},"obj":"http://purl.obolibrary.org/obo/CLO_0001020"}],"text":"3. Results and Discussion\n\n3.1. COMSOL MultiPhysics Simulation Results\nIn Figure 5, the results of heat transfer simulations of two different heater spacings are shown. The heater width for both geometries is 0.3 mm, while the heater spacing in Figure 5b,c are 0.3 mm and 2.0 mm, respectively. In Figure 6a–d, tables with the results of the full parametric sweep for different heater widths and heater spacings are shown. Figure 6a shows the temperature deviation between the highest and lowest temperature at the top of the chamber, i.e., the second H2O and COC interface (ΔTtopofchamber=Ttop,max−Ttop,min). Figure 6b shows the deviation between the highest and lowest temperature inside the chamber, i.e., between the two COC and H2O interfaces (ΔTacrosschamber=Tbottom,max−Ttop,min). Figure 6c shows the temperature deviation between the highest and lowest temperature at the bottom of the chamber, i.e., the first COC and H2O interface (ΔTbottomofchamber=Tbot,max−Tbot,min). Figure 6d shows the deviation between the set heater temperature of 30 °C and the lowest temperature at the top of the chamber, i.e., the second H2O and COC interface (ΔTdeviationfromsetT=Theater−Ttop,min). As can be seen from the results in Figure 6, a combination of small heater widths and heater spacings will result in smaller temperature differences inside the reaction mixture. This is evident as smaller heater spacings will result in a better coverage of the heated area by heater material. The smaller heater widths will result in a smaller heater cross-sectional area, and thus can be operated at lower powers, as is evident from Equation (1). Resulting in the fact that a densely packed meander structure with small heater widths and small heater spacings can dissipate more heat into the system.\nBased on these results and its simplicity, a meandering heater pattern of a heater with a width of 0.3 mm and a spacing of 0.3 mm in between the lines is designed. A side note on the chosen heater width and heater spacing is that according to the simulations, the temperature differences within the chamber are less than ±0.3 °C for the most unfavorable dimensions. This temperature difference is still well-accepted in the temperature window in which the MDA reaction takes place (25 °C to 35 °C). However, as pointed out, a smaller cross-sectional area will result in a lower power consumption and therefore these dimensions are chosen. It is known that a meandering heater structure does not give the optimal temperature distribution over the device [26]. Therefore, the heater lines are longer than the width of the reaction chamber, and thus also covering the bulk material outside the chamber in order to improve the temperature uniformity inside the reaction mixture.\nThe heater pattern is divided over two shadow masks to minimize the length of the narrow Mo tracks in between the meandering structure. This prevents curvature due to intrinsic stresses. See Figure 7 for the outlines of both shadow masks, together with the resulting pattern on COC. The use of two shadow masks will give a metal track in which small parts has the double thickness. Here, the temperature will be lower. The system is designed such that these thicker parts are outside the reaction chamber and temperature control chamber region.\n\n3.2. Fabrication\n\nMilling and Optical Transparency\nThe milling increased the surface roughness of the COC plates also increases the surface area. Inhibition of the amplification can be caused by large surface areas as the used chemicals have more surface to have interaction with [44]. The created surface roughness is visualized using a FEI Sirion high resolution scanning electron microscope (HR-SEM) (FEI Company, Hillsboro, OR, USA) and measured using a Bruker Icon Dimension AFM in tapping mode with Bruker Tespa-V2 cantilevers (Bruker Nano Surfaces, Santa Barbara, CA, USA) and Gwyddion 2.52 open source freeware [62]. The results are shown in Figure 8. The surface roughness of pristine COC had a RRMS of 3.5 nm. This increased two orders of magnitude after milling (RRMS of 310.1 nm). With the reported surface treatment [44,59] we were capable of decreasing the surface roughness to a value even lower than that of pristine COC and the lowest reported in literature (RRMS of 0.9 nm). For this grade of COC (TOPAS 6017) it worked the best to do four short exposures of 5 s, with N2 blow drying after each exposure, instead of one longer exposure, as is more common in other grades of COC [44,59]. The difference in duration for the cyclohexane vapor post-treatment can be explained by the different ratios of the copolymers present in each grade. As the grade number increase, the ratio changes towards more norbornene monomers and less linear ethene monomers. The norbornene is more apolar due to the bridged cyclic hydrocarbon present in its molecular structure and therefore, will dissolve faster in non-polar solvents, like cyclohexane (vapor).\nLowering the surface roughness also increased the optical transmittance fivefold. Transmittance measurements in the visible range are done using a Woollam M-2000UI ellipsometer (J.A. Woollam Co., Lincoln, NE, USA). The results can be seen in Figure 9 and Figure 10. Having a high optical transparency in the visible range can be desired when in situ fluorescence detection will be implemented (e.g., EvaGreen fluorescence dye has an excitation wavelength of 500 nm and emission wavelength of 525 nm [63]). However, as in situ fluorescence detection is not used yet in this system and can also be done through the transparent PCR plate sealing foil, no further effort is put into optimizing this procedure to get even better optical transmittance.\n\n3.3. Metal Adhesion\nTo get reliable heaters, four possible options are investigated for their adhesion properties to the COC substrate. The adhesion of Au and Pt deposited by either evaporation or DC magnetron sputtering is investigated using the Scotch tape test [60,61] before and after temperature cycling up to 100 °C. Test patterns consisting of rectangular metal strips of 2 mm by 14 mm are fabricated by depositing 100 nm of metal using a hand-made shadow mask made out of DuPont Kapton® HN polyimide film of 0.05 mm thickness (RS Components B.V., Haarlem, The Netherlands). See Table 4 for the results of the Scotch tape test.\nNormally, heating up a glass or Si substrate with thin metal strips while measuring the resistance (RT) in these metal strips at certain temperature intervals (T) yields directly a linear relation, which can be fitted with RT/R0=1+αT−T0 [64], in which α is the the temperature coefficient of resistance (TCR) value. The thin-film TCR values have to be measured as they differ from the bulk TCR values due to its dependency on layer purity, grain size, and deposition method [65,66]. Belser and Hicklin also lists other attributes, such as surface roughness, porosity, and adsorbed materials present in or on the substrate which could influence the TCR value [64]. The bulk TCR values are 0.0034 K−1 and 0.0037 K−1 for Au and Pt [67].\nThe TCR characterizations of the metal strips on a COC substrate did not yield trustworthy TCR values at the first cycle. The first temperature cycle can be seen as a kind of thermal annealing, and therefore gives an hysteresis in the graphs, as can be seen in Figure A2 in Appendix C.1. After this first cycle, the values more or less show the linear behavior. The resulting TCR of this linear part is in agreement with the TCR ranges of Belser and Hicklin [64] and is given in Table 4. Belser and Hicklin used for their experiments substrates with coefficients of linear thermal expansion lower than 1.2 × 10−5 °C−1 [64]. The coefficient of linear thermal expansion for Au and Pt are 1.42 × 10−5 K−1 and 0.88 × 10−5 K−1, respectively [68]. COC of the grade TOPAS 6017 has a coefficient of linear thermal expansion of 6.0 × 10−5 K−1 [42]. This mismatch in coefficients of linear thermal expansion can give strain in the metal layers. Both Au [69,70,71] and Pt [72,73,74] are used as strain-sensitive gauges, and thus are sensitive to strain-induced geometry changes due to thermal expansion.\nAnother effect influencing the TCR value of the metal layer is aging. As can be seen in Figure A3 in Appendix C.2, the TCR value already changes after two weeks storing in ambient conditions. This could be due to adsorbed materials present on the surface [64].\nHowever, in this device, the TCR is not of importance as the metal structure will not be used as temperature sensor. Real-time temperature sensing is done using a thermocouple in the temperature monitor chamber. The resistance of the heater structure changes with temperature; thus, the dissipated power changes when a fixed voltage or current is used. However, the results in Section 3.4 show a 25 h stability test with a constant input potential and only a ±1.5 °C deviation. The TCR can become more important when other (higher) temperatures are required for the amplification.\nBased on the results in Table 4, the choice of heater material and deposition method to be used in the actual device is Au deposited using sputtering. Sputtering is an industrial-scale technique that is already being used in, for example, the car mirror and headlight industry [75].\n\n3.4. Chip Functioning\nCharacterization of the actual heat distribution is done using a FLIR One Pro iOS thermal camera (FLIR Systems, Inc., Wilsonville, OR, USA). Thermal images of the heat distribution are made at the side of the substrate without the resistor, whereas different input powers are used to heat up the heater. Au reflects the infrared radiation of the environment directly, therefore an image with the resistor facing the camera would give a heat map of the surrounding and not of the real temperature of the heater. These measurements also gives a better insight of the heat distribution inside the reaction chamber. The images are processed using the FLIR postprocessing freeware. Results of these measurements are shown in Figure 11a,b. The results are in good agreement with the estimations in Table 1. The slight deviation between the values can be explained by the fact that the heated area in the calculations had an assumed value, the thermal camera measurements used 1.5 mm thick COC substrates without a water-filled chamber, the actual resistors have small parts wich have a double thickness due to the two used shadow masks, and rounding of the values used in the calculations.\nThe reliability of the heater is tested by inserting the thermocouple into the temperature control chamber (see Figure 3a). A constant input potential of 4 V is applied using the Keithley source and the temperature is measured for 25 h. This exceeds the required operation time at least twelve-fold, meaning that it is a good indication for the reliability of the heater and thermocouple. The results are shown in Figure 11c.\nTo perform on-chip amplifications, the resistive heater on the chip is connected to the Keithley source using crocodile connections and the thermocouple is inserted in the temperature control chamber and connected to a Tenma 72-7715 Thermometer (see Figure 12).\n\n3.5. DNA Amplification\nFirst, to determine the temperature window of operation, MDA reactions are performed at 25 °C and 30 °C using the Illustra GenomiPhi V2 DNA amplification kit and EvaGreen fluorescence dye. From the literature, we know that this reaction does not work above 35 °C due to degradation of the protein activity in presence of a substrate [44]. In Figure 13, a graph of the fluorescence signal during MDA reactions at 25 °C and 30 °C, together with their non template control (NTC) is shown. These reactions are carried out in a conventional Bio-Rad CFX96 Touch Real-Time PCR machine (Bio-Rad Laboratories, Inc., Hercules, CA, USA) and the results show that the chosen proof-of-principle DNA amplification reaction is temperature dependent to some extent, but that there is a wide range of temperatures at which the amplification can be performed, i.e., 25°C to 35°C. This makes the functioning of the integrated resistive heater less critical than the stability shown in Figure 11c.\nMDA reactions are also performed inside an Eppendorf tube (Eppendorf AG, Hamburg, Germany) and inside the chip, again using the Illustra GenomiPhi V2 DNA amplification kit and EvaGreen fluorescence dye. As heat supply the water bath of an IKA Rotary Evaporator RV 8V (IKA-Werke, Staufen im Breisgau, Germany) is used. This water bath is according to its specification stable within a range of the set temperature ±0.1 °C. The chip and an Eppendorf tube are loaded with the reaction mixture containing the DNA sample and the EvaGreen dye solution. Here, the Eppendorf tube is serving as a control to show that the fabrication steps of the chips are not inhibiting the MDA reaction. The inlet and outlet of the chip are sealed with the Microseal “B” PCR plate sealing foil. The closed chip and tube are heated up in a separate water bath to 95 °C and kept at that temperature for 3 min to denaturate the dsDNA. Subsequently, the chip and tube are cooled down by placing it in an ice bath for 5 min after which the rest of the reagents are added. The complete mixtures are according to Table A3 in Appendix D. After closing the chip and tube again, they are placed in the water bath of the rotary evaporater and left there for 90 min, after which the reaction is terminated at 65 °C.\nThe MDA is also performed inside the chip, but with the integrated Au resistive heater serving as heat source. The set up shown schematically in Figure 12. The same procedure is followed as with the water bath heated test. Denaturation is done in a separate water bath. The heater is driven by an input potential of 3.2 V to get to a temperature of 30 °C and at the end of the reaction, the system is heated up to 65 °C by applying a potential of 9.2 V in order to terminate the amplification. In Figure 14 the logged temperature during the amplification is shown.\nAfter the amplifications, the reaction mixtures are pipetted out of the chips and tubes and into 1 mL quartz cuvettes containing 55 μL MilliQ DI water (Merck Millipore, Burlington, MA, USA). Fluorescence measurements are done in a Horiba Scientific FluoroMax+ spectrofluorometer to verify each amplification. The mixture is excitated at a wavelength of 500 nm and the emission spectrum is measured at wavelengths from 510 nm to 550 nm (bounded EvaGreen dye has a peak at 525 nm [63]). The measured spectra are normalized by subtracting the background signal of a mixture containing only the reaction buffer, the sample buffer, EvaGreen, and DNA. No Enzyme was added to this mixture, therefore no amplification could take place. See Figure 15 for the results obtained in the Eppendorf tube and chips. Figure A4 in Appendix E shows the background signal which is subtracted from all measurements.\nAs can be seen in Figure 15, the spectra of the amplification performed inside the chip, and by applying heat with the water bath as well as with the integrated Au-resistive heater, show the same trend as the amplification performed in the Eppendorf and heated by water bath. There is an order of magnitude difference in the fluorescence signal. However, the fluorescence intensity cannot be used as a value to quantify the amount of DNA. EvaGreen is a bis-intercalating cyanine fluorescence dye consisting of two monomeric DNA-binding dyes which are linked by a flexible spacer. These two DNA-binding dyes bind each in between two base pairs, which make them simple and fast, but also nonuniform and non-specific [44,63]. However, with this dye, a simple yes-or-no answer can be obtained if the amplification took place, as can be seen in Figure 15."}
LitCovid-PD-CHEBI
{"project":"LitCovid-PD-CHEBI","denotations":[{"id":"T180","span":{"begin":551,"end":554},"obj":"Chemical"},{"id":"T181","span":{"begin":559,"end":562},"obj":"Chemical"},{"id":"T182","span":{"begin":724,"end":727},"obj":"Chemical"},{"id":"T183","span":{"begin":732,"end":735},"obj":"Chemical"},{"id":"T184","span":{"begin":918,"end":921},"obj":"Chemical"},{"id":"T185","span":{"begin":926,"end":929},"obj":"Chemical"},{"id":"T186","span":{"begin":1124,"end":1127},"obj":"Chemical"},{"id":"T187","span":{"begin":1132,"end":1135},"obj":"Chemical"},{"id":"T188","span":{"begin":1355,"end":1362},"obj":"Chemical"},{"id":"T189","span":{"begin":2244,"end":2247},"obj":"Chemical"},{"id":"T190","span":{"begin":2754,"end":2761},"obj":"Chemical"},{"id":"T191","span":{"begin":2852,"end":2854},"obj":"Chemical"},{"id":"T192","span":{"begin":3041,"end":3044},"obj":"Chemical"},{"id":"T193","span":{"begin":3411,"end":3414},"obj":"Chemical"},{"id":"T194","span":{"begin":3683,"end":3691},"obj":"Chemical"},{"id":"T195","span":{"begin":4003,"end":4006},"obj":"Chemical"},{"id":"T196","span":{"begin":4242,"end":4245},"obj":"Chemical"},{"id":"T197","span":{"begin":4320,"end":4323},"obj":"Chemical"},{"id":"T198","span":{"begin":4396,"end":4398},"obj":"Chemical"},{"id":"T199","span":{"begin":4501,"end":4504},"obj":"Chemical"},{"id":"T200","span":{"begin":4549,"end":4560},"obj":"Chemical"},{"id":"T201","span":{"begin":4630,"end":4640},"obj":"Chemical"},{"id":"T203","span":{"begin":4725,"end":4735},"obj":"Chemical"},{"id":"T204","span":{"begin":4761,"end":4767},"obj":"Chemical"},{"id":"T205","span":{"begin":4782,"end":4792},"obj":"Chemical"},{"id":"T206","span":{"begin":4827,"end":4845},"obj":"Chemical"},{"id":"T207","span":{"begin":4834,"end":4845},"obj":"Chemical"},{"id":"T208","span":{"begin":4924,"end":4938},"obj":"Chemical"},{"id":"T209","span":{"begin":4930,"end":4938},"obj":"Chemical"},{"id":"T210","span":{"begin":4945,"end":4956},"obj":"Chemical"},{"id":"T211","span":{"begin":5157,"end":5159},"obj":"Chemical"},{"id":"T212","span":{"begin":5171,"end":5173},"obj":"Chemical"},{"id":"T213","span":{"begin":5388,"end":5391},"obj":"Chemical"},{"id":"T214","span":{"begin":5835,"end":5838},"obj":"Chemical"},{"id":"T215","span":{"begin":5866,"end":5868},"obj":"Chemical"},{"id":"T216","span":{"begin":5873,"end":5875},"obj":"Chemical"},{"id":"T218","span":{"begin":6212,"end":6221},"obj":"Chemical"},{"id":"T220","span":{"begin":6249,"end":6251},"obj":"Chemical"},{"id":"T221","span":{"begin":6381,"end":6383},"obj":"Chemical"},{"id":"T222","span":{"begin":7067,"end":7069},"obj":"Chemical"},{"id":"T223","span":{"begin":7074,"end":7076},"obj":"Chemical"},{"id":"T225","span":{"begin":7134,"end":7137},"obj":"Chemical"},{"id":"T226","span":{"begin":7755,"end":7757},"obj":"Chemical"},{"id":"T227","span":{"begin":7762,"end":7764},"obj":"Chemical"},{"id":"T229","span":{"begin":7825,"end":7828},"obj":"Chemical"},{"id":"T230","span":{"begin":8023,"end":8025},"obj":"Chemical"},{"id":"T231","span":{"begin":8041,"end":8043},"obj":"Chemical"},{"id":"T233","span":{"begin":9138,"end":9140},"obj":"Chemical"},{"id":"T234","span":{"begin":9398,"end":9401},"obj":"Chemical"},{"id":"T235","span":{"begin":9628,"end":9630},"obj":"Chemical"},{"id":"T236","span":{"begin":10307,"end":10310},"obj":"Chemical"},{"id":"T237","span":{"begin":10332,"end":10337},"obj":"Chemical"},{"id":"T238","span":{"begin":11202,"end":11205},"obj":"Chemical"},{"id":"T239","span":{"begin":11277,"end":11280},"obj":"Chemical"},{"id":"T240","span":{"begin":11356,"end":11359},"obj":"Chemical"},{"id":"T241","span":{"begin":11404,"end":11407},"obj":"Chemical"},{"id":"T242","span":{"begin":11509,"end":11516},"obj":"Chemical"},{"id":"T243","span":{"begin":11615,"end":11618},"obj":"Chemical"},{"id":"T244","span":{"begin":11902,"end":11905},"obj":"Chemical"},{"id":"T245","span":{"begin":12198,"end":12201},"obj":"Chemical"},{"id":"T246","span":{"begin":12267,"end":12269},"obj":"Chemical"},{"id":"T249","span":{"begin":12348,"end":12351},"obj":"Chemical"},{"id":"T250","span":{"begin":12396,"end":12399},"obj":"Chemical"},{"id":"T251","span":{"begin":12420,"end":12425},"obj":"Chemical"},{"id":"T252","span":{"begin":12459,"end":12461},"obj":"Chemical"},{"id":"T253","span":{"begin":12485,"end":12487},"obj":"Chemical"},{"id":"T254","span":{"begin":12521,"end":12526},"obj":"Chemical"},{"id":"T255","span":{"begin":12680,"end":12687},"obj":"Chemical"},{"id":"T256","span":{"begin":12703,"end":12706},"obj":"Chemical"},{"id":"T257","span":{"begin":12731,"end":12734},"obj":"Chemical"},{"id":"T258","span":{"begin":12735,"end":12743},"obj":"Chemical"},{"id":"T259","span":{"begin":12865,"end":12868},"obj":"Chemical"},{"id":"T260","span":{"begin":13023,"end":13028},"obj":"Chemical"},{"id":"T261","span":{"begin":13222,"end":13230},"obj":"Chemical"},{"id":"T262","span":{"begin":13367,"end":13372},"obj":"Chemical"},{"id":"T263","span":{"begin":13483,"end":13486},"obj":"Chemical"},{"id":"T264","span":{"begin":13546,"end":13548},"obj":"Chemical"},{"id":"T265","span":{"begin":13678,"end":13683},"obj":"Chemical"},{"id":"T266","span":{"begin":13737,"end":13742},"obj":"Chemical"},{"id":"T267","span":{"begin":14146,"end":14152},"obj":"Chemical"},{"id":"T268","span":{"begin":14189,"end":14194},"obj":"Chemical"},{"id":"T269","span":{"begin":14225,"end":14227},"obj":"Chemical"},{"id":"T272","span":{"begin":14357,"end":14364},"obj":"Chemical"},{"id":"T273","span":{"begin":14497,"end":14500},"obj":"Chemical"},{"id":"T274","span":{"begin":14607,"end":14614},"obj":"Chemical"},{"id":"T275","span":{"begin":14644,"end":14650},"obj":"Chemical"},{"id":"T276","span":{"begin":14663,"end":14669},"obj":"Chemical"},{"id":"T277","span":{"begin":14685,"end":14688},"obj":"Chemical"},{"id":"T278","span":{"begin":14718,"end":14725},"obj":"Chemical"},{"id":"T279","span":{"begin":15058,"end":15063},"obj":"Chemical"},{"id":"T280","span":{"begin":15100,"end":15102},"obj":"Chemical"},{"id":"T281","span":{"begin":15203,"end":15208},"obj":"Chemical"},{"id":"T282","span":{"begin":15373,"end":15376},"obj":"Chemical"},{"id":"T283","span":{"begin":15431,"end":15434},"obj":"Chemical"},{"id":"T284","span":{"begin":15463,"end":15466},"obj":"Chemical"},{"id":"T285","span":{"begin":15475,"end":15479},"obj":"Chemical"},{"id":"T286","span":{"begin":15529,"end":15532},"obj":"Chemical"},{"id":"T287","span":{"begin":15541,"end":15545},"obj":"Chemical"},{"id":"T288","span":{"begin":15571,"end":15575},"obj":"Chemical"},{"id":"T289","span":{"begin":15681,"end":15684},"obj":"Chemical"}],"attributes":[{"id":"A180","pred":"chebi_id","subj":"T180","obj":"http://purl.obolibrary.org/obo/CHEBI_15377"},{"id":"A181","pred":"chebi_id","subj":"T181","obj":"http://purl.obolibrary.org/obo/CHEBI_53310"},{"id":"A182","pred":"chebi_id","subj":"T182","obj":"http://purl.obolibrary.org/obo/CHEBI_53310"},{"id":"A183","pred":"chebi_id","subj":"T183","obj":"http://purl.obolibrary.org/obo/CHEBI_15377"},{"id":"A184","pred":"chebi_id","subj":"T184","obj":"http://purl.obolibrary.org/obo/CHEBI_53310"},{"id":"A185","pred":"chebi_id","subj":"T185","obj":"http://purl.obolibrary.org/obo/CHEBI_15377"},{"id":"A186","pred":"chebi_id","subj":"T186","obj":"http://purl.obolibrary.org/obo/CHEBI_15377"},{"id":"A187","pred":"chebi_id","subj":"T187","obj":"http://purl.obolibrary.org/obo/CHEBI_53310"},{"id":"A188","pred":"chebi_id","subj":"T188","obj":"http://purl.obolibrary.org/obo/CHEBI_60004"},{"id":"A189","pred":"chebi_id","subj":"T189","obj":"http://purl.obolibrary.org/obo/CHEBI_566274"},{"id":"A190","pred":"chebi_id","subj":"T190","obj":"http://purl.obolibrary.org/obo/CHEBI_60004"},{"id":"A191","pred":"chebi_id","subj":"T191","obj":"http://purl.obolibrary.org/obo/CHEBI_28685"},{"id":"A192","pred":"chebi_id","subj":"T192","obj":"http://purl.obolibrary.org/obo/CHEBI_53310"},{"id":"A193","pred":"chebi_id","subj":"T193","obj":"http://purl.obolibrary.org/obo/CHEBI_53310"},{"id":"A194","pred":"chebi_id","subj":"T194","obj":"http://purl.obolibrary.org/obo/CHEBI_10545"},{"id":"A195","pred":"chebi_id","subj":"T195","obj":"http://purl.obolibrary.org/obo/CHEBI_53310"},{"id":"A196","pred":"chebi_id","subj":"T196","obj":"http://purl.obolibrary.org/obo/CHEBI_53310"},{"id":"A197","pred":"chebi_id","subj":"T197","obj":"http://purl.obolibrary.org/obo/CHEBI_53310"},{"id":"A198","pred":"chebi_id","subj":"T198","obj":"http://purl.obolibrary.org/obo/CHEBI_17997"},{"id":"A199","pred":"chebi_id","subj":"T199","obj":"http://purl.obolibrary.org/obo/CHEBI_53310"},{"id":"A200","pred":"chebi_id","subj":"T200","obj":"http://purl.obolibrary.org/obo/CHEBI_29005"},{"id":"A201","pred":"chebi_id","subj":"T201","obj":"http://purl.obolibrary.org/obo/CHEBI_53310"},{"id":"A202","pred":"chebi_id","subj":"T201","obj":"http://purl.obolibrary.org/obo/CHEBI_60804"},{"id":"A203","pred":"chebi_id","subj":"T203","obj":"http://purl.obolibrary.org/obo/CHEBI_52286"},{"id":"A204","pred":"chebi_id","subj":"T204","obj":"http://purl.obolibrary.org/obo/CHEBI_18153"},{"id":"A205","pred":"chebi_id","subj":"T205","obj":"http://purl.obolibrary.org/obo/CHEBI_52286"},{"id":"A206","pred":"chebi_id","subj":"T206","obj":"http://purl.obolibrary.org/obo/CHEBI_33663"},{"id":"A207","pred":"chebi_id","subj":"T207","obj":"http://purl.obolibrary.org/obo/CHEBI_24632"},{"id":"A208","pred":"chebi_id","subj":"T208","obj":"http://purl.obolibrary.org/obo/CHEBI_48354"},{"id":"A209","pred":"chebi_id","subj":"T209","obj":"http://purl.obolibrary.org/obo/CHEBI_46787"},{"id":"A210","pred":"chebi_id","subj":"T210","obj":"http://purl.obolibrary.org/obo/CHEBI_29005"},{"id":"A211","pred":"chebi_id","subj":"T211","obj":"http://purl.obolibrary.org/obo/CHEBI_27638"},{"id":"A212","pred":"chebi_id","subj":"T212","obj":"http://purl.obolibrary.org/obo/CHEBI_73824"},{"id":"A213","pred":"chebi_id","subj":"T213","obj":"http://purl.obolibrary.org/obo/CHEBI_37958"},{"id":"A214","pred":"chebi_id","subj":"T214","obj":"http://purl.obolibrary.org/obo/CHEBI_53310"},{"id":"A215","pred":"chebi_id","subj":"T215","obj":"http://purl.obolibrary.org/obo/CHEBI_29287"},{"id":"A216","pred":"chebi_id","subj":"T216","obj":"http://purl.obolibrary.org/obo/CHEBI_33364"},{"id":"A217","pred":"chebi_id","subj":"T216","obj":"http://purl.obolibrary.org/obo/CHEBI_75318"},{"id":"A218","pred":"chebi_id","subj":"T218","obj":"http://purl.obolibrary.org/obo/CHEBI_53232"},{"id":"A219","pred":"chebi_id","subj":"T218","obj":"http://purl.obolibrary.org/obo/CHEBI_61484"},{"id":"A220","pred":"chebi_id","subj":"T220","obj":"http://purl.obolibrary.org/obo/CHEBI_73819"},{"id":"A221","pred":"chebi_id","subj":"T221","obj":"http://purl.obolibrary.org/obo/CHEBI_27573"},{"id":"A222","pred":"chebi_id","subj":"T222","obj":"http://purl.obolibrary.org/obo/CHEBI_29287"},{"id":"A223","pred":"chebi_id","subj":"T223","obj":"http://purl.obolibrary.org/obo/CHEBI_33364"},{"id":"A224","pred":"chebi_id","subj":"T223","obj":"http://purl.obolibrary.org/obo/CHEBI_75318"},{"id":"A225","pred":"chebi_id","subj":"T225","obj":"http://purl.obolibrary.org/obo/CHEBI_53310"},{"id":"A226","pred":"chebi_id","subj":"T226","obj":"http://purl.obolibrary.org/obo/CHEBI_29287"},{"id":"A227","pred":"chebi_id","subj":"T227","obj":"http://purl.obolibrary.org/obo/CHEBI_33364"},{"id":"A228","pred":"chebi_id","subj":"T227","obj":"http://purl.obolibrary.org/obo/CHEBI_75318"},{"id":"A229","pred":"chebi_id","subj":"T229","obj":"http://purl.obolibrary.org/obo/CHEBI_53310"},{"id":"A230","pred":"chebi_id","subj":"T230","obj":"http://purl.obolibrary.org/obo/CHEBI_29287"},{"id":"A231","pred":"chebi_id","subj":"T231","obj":"http://purl.obolibrary.org/obo/CHEBI_33364"},{"id":"A232","pred":"chebi_id","subj":"T231","obj":"http://purl.obolibrary.org/obo/CHEBI_75318"},{"id":"A233","pred":"chebi_id","subj":"T233","obj":"http://purl.obolibrary.org/obo/CHEBI_29287"},{"id":"A234","pred":"chebi_id","subj":"T234","obj":"http://purl.obolibrary.org/obo/CHEBI_50342"},{"id":"A235","pred":"chebi_id","subj":"T235","obj":"http://purl.obolibrary.org/obo/CHEBI_29287"},{"id":"A236","pred":"chebi_id","subj":"T236","obj":"http://purl.obolibrary.org/obo/CHEBI_53310"},{"id":"A237","pred":"chebi_id","subj":"T237","obj":"http://purl.obolibrary.org/obo/CHEBI_15377"},{"id":"A238","pred":"chebi_id","subj":"T238","obj":"http://purl.obolibrary.org/obo/CHEBI_16991"},{"id":"A239","pred":"chebi_id","subj":"T239","obj":"http://purl.obolibrary.org/obo/CHEBI_566274"},{"id":"A240","pred":"chebi_id","subj":"T240","obj":"http://purl.obolibrary.org/obo/CHEBI_16991"},{"id":"A241","pred":"chebi_id","subj":"T241","obj":"http://purl.obolibrary.org/obo/CHEBI_37958"},{"id":"A242","pred":"chebi_id","subj":"T242","obj":"http://purl.obolibrary.org/obo/CHEBI_36080"},{"id":"A243","pred":"chebi_id","subj":"T243","obj":"http://purl.obolibrary.org/obo/CHEBI_566274"},{"id":"A244","pred":"chebi_id","subj":"T244","obj":"http://purl.obolibrary.org/obo/CHEBI_16991"},{"id":"A245","pred":"chebi_id","subj":"T245","obj":"http://purl.obolibrary.org/obo/CHEBI_566274"},{"id":"A246","pred":"chebi_id","subj":"T246","obj":"http://purl.obolibrary.org/obo/CHEBI_27569"},{"id":"A247","pred":"chebi_id","subj":"T246","obj":"http://purl.obolibrary.org/obo/CHEBI_40618"},{"id":"A248","pred":"chebi_id","subj":"T246","obj":"http://purl.obolibrary.org/obo/CHEBI_73757"},{"id":"A249","pred":"chebi_id","subj":"T249","obj":"http://purl.obolibrary.org/obo/CHEBI_16991"},{"id":"A250","pred":"chebi_id","subj":"T250","obj":"http://purl.obolibrary.org/obo/CHEBI_37958"},{"id":"A251","pred":"chebi_id","subj":"T251","obj":"http://purl.obolibrary.org/obo/CHEBI_15377"},{"id":"A252","pred":"chebi_id","subj":"T252","obj":"http://purl.obolibrary.org/obo/CHEBI_73823"},{"id":"A253","pred":"chebi_id","subj":"T253","obj":"http://purl.obolibrary.org/obo/CHEBI_30366"},{"id":"A254","pred":"chebi_id","subj":"T254","obj":"http://purl.obolibrary.org/obo/CHEBI_15377"},{"id":"A255","pred":"chebi_id","subj":"T255","obj":"http://purl.obolibrary.org/obo/CHEBI_60004"},{"id":"A256","pred":"chebi_id","subj":"T256","obj":"http://purl.obolibrary.org/obo/CHEBI_16991"},{"id":"A257","pred":"chebi_id","subj":"T257","obj":"http://purl.obolibrary.org/obo/CHEBI_37958"},{"id":"A258","pred":"chebi_id","subj":"T258","obj":"http://purl.obolibrary.org/obo/CHEBI_75958"},{"id":"A259","pred":"chebi_id","subj":"T259","obj":"http://purl.obolibrary.org/obo/CHEBI_566274"},{"id":"A260","pred":"chebi_id","subj":"T260","obj":"http://purl.obolibrary.org/obo/CHEBI_15377"},{"id":"A261","pred":"chebi_id","subj":"T261","obj":"http://purl.obolibrary.org/obo/CHEBI_33893"},{"id":"A262","pred":"chebi_id","subj":"T262","obj":"http://purl.obolibrary.org/obo/CHEBI_15377"},{"id":"A263","pred":"chebi_id","subj":"T263","obj":"http://purl.obolibrary.org/obo/CHEBI_566274"},{"id":"A264","pred":"chebi_id","subj":"T264","obj":"http://purl.obolibrary.org/obo/CHEBI_29287"},{"id":"A265","pred":"chebi_id","subj":"T265","obj":"http://purl.obolibrary.org/obo/CHEBI_15377"},{"id":"A266","pred":"chebi_id","subj":"T266","obj":"http://purl.obolibrary.org/obo/CHEBI_15377"},{"id":"A267","pred":"chebi_id","subj":"T267","obj":"http://purl.obolibrary.org/obo/CHEBI_46727"},{"id":"A268","pred":"chebi_id","subj":"T268","obj":"http://purl.obolibrary.org/obo/CHEBI_15377"},{"id":"A269","pred":"chebi_id","subj":"T269","obj":"http://purl.obolibrary.org/obo/CHEBI_474859"},{"id":"A270","pred":"chebi_id","subj":"T269","obj":"http://purl.obolibrary.org/obo/CHEBI_73610"},{"id":"A271","pred":"chebi_id","subj":"T269","obj":"http://purl.obolibrary.org/obo/CHEBI_90325"},{"id":"A272","pred":"chebi_id","subj":"T272","obj":"http://purl.obolibrary.org/obo/CHEBI_60004"},{"id":"A273","pred":"chebi_id","subj":"T273","obj":"http://purl.obolibrary.org/obo/CHEBI_37958"},{"id":"A274","pred":"chebi_id","subj":"T274","obj":"http://purl.obolibrary.org/obo/CHEBI_60004"},{"id":"A275","pred":"chebi_id","subj":"T275","obj":"http://purl.obolibrary.org/obo/CHEBI_35225"},{"id":"A276","pred":"chebi_id","subj":"T276","obj":"http://purl.obolibrary.org/obo/CHEBI_35225"},{"id":"A277","pred":"chebi_id","subj":"T277","obj":"http://purl.obolibrary.org/obo/CHEBI_16991"},{"id":"A278","pred":"chebi_id","subj":"T278","obj":"http://purl.obolibrary.org/obo/CHEBI_60004"},{"id":"A279","pred":"chebi_id","subj":"T279","obj":"http://purl.obolibrary.org/obo/CHEBI_15377"},{"id":"A280","pred":"chebi_id","subj":"T280","obj":"http://purl.obolibrary.org/obo/CHEBI_29287"},{"id":"A281","pred":"chebi_id","subj":"T281","obj":"http://purl.obolibrary.org/obo/CHEBI_15377"},{"id":"A282","pred":"chebi_id","subj":"T282","obj":"http://purl.obolibrary.org/obo/CHEBI_16991"},{"id":"A283","pred":"chebi_id","subj":"T283","obj":"http://purl.obolibrary.org/obo/CHEBI_37958"},{"id":"A284","pred":"chebi_id","subj":"T284","obj":"http://purl.obolibrary.org/obo/CHEBI_16991"},{"id":"A285","pred":"chebi_id","subj":"T285","obj":"http://purl.obolibrary.org/obo/CHEBI_37958"},{"id":"A286","pred":"chebi_id","subj":"T286","obj":"http://purl.obolibrary.org/obo/CHEBI_16991"},{"id":"A287","pred":"chebi_id","subj":"T287","obj":"http://purl.obolibrary.org/obo/CHEBI_37958"},{"id":"A288","pred":"chebi_id","subj":"T288","obj":"http://purl.obolibrary.org/obo/CHEBI_22695"},{"id":"A289","pred":"chebi_id","subj":"T289","obj":"http://purl.obolibrary.org/obo/CHEBI_37958"}],"text":"3. Results and Discussion\n\n3.1. COMSOL MultiPhysics Simulation Results\nIn Figure 5, the results of heat transfer simulations of two different heater spacings are shown. The heater width for both geometries is 0.3 mm, while the heater spacing in Figure 5b,c are 0.3 mm and 2.0 mm, respectively. In Figure 6a–d, tables with the results of the full parametric sweep for different heater widths and heater spacings are shown. Figure 6a shows the temperature deviation between the highest and lowest temperature at the top of the chamber, i.e., the second H2O and COC interface (ΔTtopofchamber=Ttop,max−Ttop,min). Figure 6b shows the deviation between the highest and lowest temperature inside the chamber, i.e., between the two COC and H2O interfaces (ΔTacrosschamber=Tbottom,max−Ttop,min). Figure 6c shows the temperature deviation between the highest and lowest temperature at the bottom of the chamber, i.e., the first COC and H2O interface (ΔTbottomofchamber=Tbot,max−Tbot,min). Figure 6d shows the deviation between the set heater temperature of 30 °C and the lowest temperature at the top of the chamber, i.e., the second H2O and COC interface (ΔTdeviationfromsetT=Theater−Ttop,min). As can be seen from the results in Figure 6, a combination of small heater widths and heater spacings will result in smaller temperature differences inside the reaction mixture. This is evident as smaller heater spacings will result in a better coverage of the heated area by heater material. The smaller heater widths will result in a smaller heater cross-sectional area, and thus can be operated at lower powers, as is evident from Equation (1). Resulting in the fact that a densely packed meander structure with small heater widths and small heater spacings can dissipate more heat into the system.\nBased on these results and its simplicity, a meandering heater pattern of a heater with a width of 0.3 mm and a spacing of 0.3 mm in between the lines is designed. A side note on the chosen heater width and heater spacing is that according to the simulations, the temperature differences within the chamber are less than ±0.3 °C for the most unfavorable dimensions. This temperature difference is still well-accepted in the temperature window in which the MDA reaction takes place (25 °C to 35 °C). However, as pointed out, a smaller cross-sectional area will result in a lower power consumption and therefore these dimensions are chosen. It is known that a meandering heater structure does not give the optimal temperature distribution over the device [26]. Therefore, the heater lines are longer than the width of the reaction chamber, and thus also covering the bulk material outside the chamber in order to improve the temperature uniformity inside the reaction mixture.\nThe heater pattern is divided over two shadow masks to minimize the length of the narrow Mo tracks in between the meandering structure. This prevents curvature due to intrinsic stresses. See Figure 7 for the outlines of both shadow masks, together with the resulting pattern on COC. The use of two shadow masks will give a metal track in which small parts has the double thickness. Here, the temperature will be lower. The system is designed such that these thicker parts are outside the reaction chamber and temperature control chamber region.\n\n3.2. Fabrication\n\nMilling and Optical Transparency\nThe milling increased the surface roughness of the COC plates also increases the surface area. Inhibition of the amplification can be caused by large surface areas as the used chemicals have more surface to have interaction with [44]. The created surface roughness is visualized using a FEI Sirion high resolution scanning electron microscope (HR-SEM) (FEI Company, Hillsboro, OR, USA) and measured using a Bruker Icon Dimension AFM in tapping mode with Bruker Tespa-V2 cantilevers (Bruker Nano Surfaces, Santa Barbara, CA, USA) and Gwyddion 2.52 open source freeware [62]. The results are shown in Figure 8. The surface roughness of pristine COC had a RRMS of 3.5 nm. This increased two orders of magnitude after milling (RRMS of 310.1 nm). With the reported surface treatment [44,59] we were capable of decreasing the surface roughness to a value even lower than that of pristine COC and the lowest reported in literature (RRMS of 0.9 nm). For this grade of COC (TOPAS 6017) it worked the best to do four short exposures of 5 s, with N2 blow drying after each exposure, instead of one longer exposure, as is more common in other grades of COC [44,59]. The difference in duration for the cyclohexane vapor post-treatment can be explained by the different ratios of the copolymers present in each grade. As the grade number increase, the ratio changes towards more norbornene monomers and less linear ethene monomers. The norbornene is more apolar due to the bridged cyclic hydrocarbon present in its molecular structure and therefore, will dissolve faster in non-polar solvents, like cyclohexane (vapor).\nLowering the surface roughness also increased the optical transmittance fivefold. Transmittance measurements in the visible range are done using a Woollam M-2000UI ellipsometer (J.A. Woollam Co., Lincoln, NE, USA). The results can be seen in Figure 9 and Figure 10. Having a high optical transparency in the visible range can be desired when in situ fluorescence detection will be implemented (e.g., EvaGreen fluorescence dye has an excitation wavelength of 500 nm and emission wavelength of 525 nm [63]). However, as in situ fluorescence detection is not used yet in this system and can also be done through the transparent PCR plate sealing foil, no further effort is put into optimizing this procedure to get even better optical transmittance.\n\n3.3. Metal Adhesion\nTo get reliable heaters, four possible options are investigated for their adhesion properties to the COC substrate. The adhesion of Au and Pt deposited by either evaporation or DC magnetron sputtering is investigated using the Scotch tape test [60,61] before and after temperature cycling up to 100 °C. Test patterns consisting of rectangular metal strips of 2 mm by 14 mm are fabricated by depositing 100 nm of metal using a hand-made shadow mask made out of DuPont Kapton® HN polyimide film of 0.05 mm thickness (RS Components B.V., Haarlem, The Netherlands). See Table 4 for the results of the Scotch tape test.\nNormally, heating up a glass or Si substrate with thin metal strips while measuring the resistance (RT) in these metal strips at certain temperature intervals (T) yields directly a linear relation, which can be fitted with RT/R0=1+αT−T0 [64], in which α is the the temperature coefficient of resistance (TCR) value. The thin-film TCR values have to be measured as they differ from the bulk TCR values due to its dependency on layer purity, grain size, and deposition method [65,66]. Belser and Hicklin also lists other attributes, such as surface roughness, porosity, and adsorbed materials present in or on the substrate which could influence the TCR value [64]. The bulk TCR values are 0.0034 K−1 and 0.0037 K−1 for Au and Pt [67].\nThe TCR characterizations of the metal strips on a COC substrate did not yield trustworthy TCR values at the first cycle. The first temperature cycle can be seen as a kind of thermal annealing, and therefore gives an hysteresis in the graphs, as can be seen in Figure A2 in Appendix C.1. After this first cycle, the values more or less show the linear behavior. The resulting TCR of this linear part is in agreement with the TCR ranges of Belser and Hicklin [64] and is given in Table 4. Belser and Hicklin used for their experiments substrates with coefficients of linear thermal expansion lower than 1.2 × 10−5 °C−1 [64]. The coefficient of linear thermal expansion for Au and Pt are 1.42 × 10−5 K−1 and 0.88 × 10−5 K−1, respectively [68]. COC of the grade TOPAS 6017 has a coefficient of linear thermal expansion of 6.0 × 10−5 K−1 [42]. This mismatch in coefficients of linear thermal expansion can give strain in the metal layers. Both Au [69,70,71] and Pt [72,73,74] are used as strain-sensitive gauges, and thus are sensitive to strain-induced geometry changes due to thermal expansion.\nAnother effect influencing the TCR value of the metal layer is aging. As can be seen in Figure A3 in Appendix C.2, the TCR value already changes after two weeks storing in ambient conditions. This could be due to adsorbed materials present on the surface [64].\nHowever, in this device, the TCR is not of importance as the metal structure will not be used as temperature sensor. Real-time temperature sensing is done using a thermocouple in the temperature monitor chamber. The resistance of the heater structure changes with temperature; thus, the dissipated power changes when a fixed voltage or current is used. However, the results in Section 3.4 show a 25 h stability test with a constant input potential and only a ±1.5 °C deviation. The TCR can become more important when other (higher) temperatures are required for the amplification.\nBased on the results in Table 4, the choice of heater material and deposition method to be used in the actual device is Au deposited using sputtering. Sputtering is an industrial-scale technique that is already being used in, for example, the car mirror and headlight industry [75].\n\n3.4. Chip Functioning\nCharacterization of the actual heat distribution is done using a FLIR One Pro iOS thermal camera (FLIR Systems, Inc., Wilsonville, OR, USA). Thermal images of the heat distribution are made at the side of the substrate without the resistor, whereas different input powers are used to heat up the heater. Au reflects the infrared radiation of the environment directly, therefore an image with the resistor facing the camera would give a heat map of the surrounding and not of the real temperature of the heater. These measurements also gives a better insight of the heat distribution inside the reaction chamber. The images are processed using the FLIR postprocessing freeware. Results of these measurements are shown in Figure 11a,b. The results are in good agreement with the estimations in Table 1. The slight deviation between the values can be explained by the fact that the heated area in the calculations had an assumed value, the thermal camera measurements used 1.5 mm thick COC substrates without a water-filled chamber, the actual resistors have small parts wich have a double thickness due to the two used shadow masks, and rounding of the values used in the calculations.\nThe reliability of the heater is tested by inserting the thermocouple into the temperature control chamber (see Figure 3a). A constant input potential of 4 V is applied using the Keithley source and the temperature is measured for 25 h. This exceeds the required operation time at least twelve-fold, meaning that it is a good indication for the reliability of the heater and thermocouple. The results are shown in Figure 11c.\nTo perform on-chip amplifications, the resistive heater on the chip is connected to the Keithley source using crocodile connections and the thermocouple is inserted in the temperature control chamber and connected to a Tenma 72-7715 Thermometer (see Figure 12).\n\n3.5. DNA Amplification\nFirst, to determine the temperature window of operation, MDA reactions are performed at 25 °C and 30 °C using the Illustra GenomiPhi V2 DNA amplification kit and EvaGreen fluorescence dye. From the literature, we know that this reaction does not work above 35 °C due to degradation of the protein activity in presence of a substrate [44]. In Figure 13, a graph of the fluorescence signal during MDA reactions at 25 °C and 30 °C, together with their non template control (NTC) is shown. These reactions are carried out in a conventional Bio-Rad CFX96 Touch Real-Time PCR machine (Bio-Rad Laboratories, Inc., Hercules, CA, USA) and the results show that the chosen proof-of-principle DNA amplification reaction is temperature dependent to some extent, but that there is a wide range of temperatures at which the amplification can be performed, i.e., 25°C to 35°C. This makes the functioning of the integrated resistive heater less critical than the stability shown in Figure 11c.\nMDA reactions are also performed inside an Eppendorf tube (Eppendorf AG, Hamburg, Germany) and inside the chip, again using the Illustra GenomiPhi V2 DNA amplification kit and EvaGreen fluorescence dye. As heat supply the water bath of an IKA Rotary Evaporator RV 8V (IKA-Werke, Staufen im Breisgau, Germany) is used. This water bath is according to its specification stable within a range of the set temperature ±0.1 °C. The chip and an Eppendorf tube are loaded with the reaction mixture containing the DNA sample and the EvaGreen dye solution. Here, the Eppendorf tube is serving as a control to show that the fabrication steps of the chips are not inhibiting the MDA reaction. The inlet and outlet of the chip are sealed with the Microseal “B” PCR plate sealing foil. The closed chip and tube are heated up in a separate water bath to 95 °C and kept at that temperature for 3 min to denaturate the dsDNA. Subsequently, the chip and tube are cooled down by placing it in an ice bath for 5 min after which the rest of the reagents are added. The complete mixtures are according to Table A3 in Appendix D. After closing the chip and tube again, they are placed in the water bath of the rotary evaporater and left there for 90 min, after which the reaction is terminated at 65 °C.\nThe MDA is also performed inside the chip, but with the integrated Au resistive heater serving as heat source. The set up shown schematically in Figure 12. The same procedure is followed as with the water bath heated test. Denaturation is done in a separate water bath. The heater is driven by an input potential of 3.2 V to get to a temperature of 30 °C and at the end of the reaction, the system is heated up to 65 °C by applying a potential of 9.2 V in order to terminate the amplification. In Figure 14 the logged temperature during the amplification is shown.\nAfter the amplifications, the reaction mixtures are pipetted out of the chips and tubes and into 1 mL quartz cuvettes containing 55 μL MilliQ DI water (Merck Millipore, Burlington, MA, USA). Fluorescence measurements are done in a Horiba Scientific FluoroMax+ spectrofluorometer to verify each amplification. The mixture is excitated at a wavelength of 500 nm and the emission spectrum is measured at wavelengths from 510 nm to 550 nm (bounded EvaGreen dye has a peak at 525 nm [63]). The measured spectra are normalized by subtracting the background signal of a mixture containing only the reaction buffer, the sample buffer, EvaGreen, and DNA. No Enzyme was added to this mixture, therefore no amplification could take place. See Figure 15 for the results obtained in the Eppendorf tube and chips. Figure A4 in Appendix E shows the background signal which is subtracted from all measurements.\nAs can be seen in Figure 15, the spectra of the amplification performed inside the chip, and by applying heat with the water bath as well as with the integrated Au-resistive heater, show the same trend as the amplification performed in the Eppendorf and heated by water bath. There is an order of magnitude difference in the fluorescence signal. However, the fluorescence intensity cannot be used as a value to quantify the amount of DNA. EvaGreen is a bis-intercalating cyanine fluorescence dye consisting of two monomeric DNA-binding dyes which are linked by a flexible spacer. These two DNA-binding dyes bind each in between two base pairs, which make them simple and fast, but also nonuniform and non-specific [44,63]. However, with this dye, a simple yes-or-no answer can be obtained if the amplification took place, as can be seen in Figure 15."}
LitCovid-PD-GO-BP
{"project":"LitCovid-PD-GO-BP","denotations":[{"id":"T10","span":{"begin":7435,"end":7443},"obj":"http://purl.obolibrary.org/obo/GO_0007610"},{"id":"T11","span":{"begin":8239,"end":8244},"obj":"http://purl.obolibrary.org/obo/GO_0007568"},{"id":"T12","span":{"begin":11202,"end":11219},"obj":"http://purl.obolibrary.org/obo/GO_0006277"},{"id":"T13","span":{"begin":11356,"end":11373},"obj":"http://purl.obolibrary.org/obo/GO_0006277"},{"id":"T14","span":{"begin":11490,"end":11501},"obj":"http://purl.obolibrary.org/obo/GO_0009056"},{"id":"T15","span":{"begin":11902,"end":11919},"obj":"http://purl.obolibrary.org/obo/GO_0006277"},{"id":"T16","span":{"begin":12348,"end":12365},"obj":"http://purl.obolibrary.org/obo/GO_0006277"}],"text":"3. Results and Discussion\n\n3.1. COMSOL MultiPhysics Simulation Results\nIn Figure 5, the results of heat transfer simulations of two different heater spacings are shown. The heater width for both geometries is 0.3 mm, while the heater spacing in Figure 5b,c are 0.3 mm and 2.0 mm, respectively. In Figure 6a–d, tables with the results of the full parametric sweep for different heater widths and heater spacings are shown. Figure 6a shows the temperature deviation between the highest and lowest temperature at the top of the chamber, i.e., the second H2O and COC interface (ΔTtopofchamber=Ttop,max−Ttop,min). Figure 6b shows the deviation between the highest and lowest temperature inside the chamber, i.e., between the two COC and H2O interfaces (ΔTacrosschamber=Tbottom,max−Ttop,min). Figure 6c shows the temperature deviation between the highest and lowest temperature at the bottom of the chamber, i.e., the first COC and H2O interface (ΔTbottomofchamber=Tbot,max−Tbot,min). Figure 6d shows the deviation between the set heater temperature of 30 °C and the lowest temperature at the top of the chamber, i.e., the second H2O and COC interface (ΔTdeviationfromsetT=Theater−Ttop,min). As can be seen from the results in Figure 6, a combination of small heater widths and heater spacings will result in smaller temperature differences inside the reaction mixture. This is evident as smaller heater spacings will result in a better coverage of the heated area by heater material. The smaller heater widths will result in a smaller heater cross-sectional area, and thus can be operated at lower powers, as is evident from Equation (1). Resulting in the fact that a densely packed meander structure with small heater widths and small heater spacings can dissipate more heat into the system.\nBased on these results and its simplicity, a meandering heater pattern of a heater with a width of 0.3 mm and a spacing of 0.3 mm in between the lines is designed. A side note on the chosen heater width and heater spacing is that according to the simulations, the temperature differences within the chamber are less than ±0.3 °C for the most unfavorable dimensions. This temperature difference is still well-accepted in the temperature window in which the MDA reaction takes place (25 °C to 35 °C). However, as pointed out, a smaller cross-sectional area will result in a lower power consumption and therefore these dimensions are chosen. It is known that a meandering heater structure does not give the optimal temperature distribution over the device [26]. Therefore, the heater lines are longer than the width of the reaction chamber, and thus also covering the bulk material outside the chamber in order to improve the temperature uniformity inside the reaction mixture.\nThe heater pattern is divided over two shadow masks to minimize the length of the narrow Mo tracks in between the meandering structure. This prevents curvature due to intrinsic stresses. See Figure 7 for the outlines of both shadow masks, together with the resulting pattern on COC. The use of two shadow masks will give a metal track in which small parts has the double thickness. Here, the temperature will be lower. The system is designed such that these thicker parts are outside the reaction chamber and temperature control chamber region.\n\n3.2. Fabrication\n\nMilling and Optical Transparency\nThe milling increased the surface roughness of the COC plates also increases the surface area. Inhibition of the amplification can be caused by large surface areas as the used chemicals have more surface to have interaction with [44]. The created surface roughness is visualized using a FEI Sirion high resolution scanning electron microscope (HR-SEM) (FEI Company, Hillsboro, OR, USA) and measured using a Bruker Icon Dimension AFM in tapping mode with Bruker Tespa-V2 cantilevers (Bruker Nano Surfaces, Santa Barbara, CA, USA) and Gwyddion 2.52 open source freeware [62]. The results are shown in Figure 8. The surface roughness of pristine COC had a RRMS of 3.5 nm. This increased two orders of magnitude after milling (RRMS of 310.1 nm). With the reported surface treatment [44,59] we were capable of decreasing the surface roughness to a value even lower than that of pristine COC and the lowest reported in literature (RRMS of 0.9 nm). For this grade of COC (TOPAS 6017) it worked the best to do four short exposures of 5 s, with N2 blow drying after each exposure, instead of one longer exposure, as is more common in other grades of COC [44,59]. The difference in duration for the cyclohexane vapor post-treatment can be explained by the different ratios of the copolymers present in each grade. As the grade number increase, the ratio changes towards more norbornene monomers and less linear ethene monomers. The norbornene is more apolar due to the bridged cyclic hydrocarbon present in its molecular structure and therefore, will dissolve faster in non-polar solvents, like cyclohexane (vapor).\nLowering the surface roughness also increased the optical transmittance fivefold. Transmittance measurements in the visible range are done using a Woollam M-2000UI ellipsometer (J.A. Woollam Co., Lincoln, NE, USA). The results can be seen in Figure 9 and Figure 10. Having a high optical transparency in the visible range can be desired when in situ fluorescence detection will be implemented (e.g., EvaGreen fluorescence dye has an excitation wavelength of 500 nm and emission wavelength of 525 nm [63]). However, as in situ fluorescence detection is not used yet in this system and can also be done through the transparent PCR plate sealing foil, no further effort is put into optimizing this procedure to get even better optical transmittance.\n\n3.3. Metal Adhesion\nTo get reliable heaters, four possible options are investigated for their adhesion properties to the COC substrate. The adhesion of Au and Pt deposited by either evaporation or DC magnetron sputtering is investigated using the Scotch tape test [60,61] before and after temperature cycling up to 100 °C. Test patterns consisting of rectangular metal strips of 2 mm by 14 mm are fabricated by depositing 100 nm of metal using a hand-made shadow mask made out of DuPont Kapton® HN polyimide film of 0.05 mm thickness (RS Components B.V., Haarlem, The Netherlands). See Table 4 for the results of the Scotch tape test.\nNormally, heating up a glass or Si substrate with thin metal strips while measuring the resistance (RT) in these metal strips at certain temperature intervals (T) yields directly a linear relation, which can be fitted with RT/R0=1+αT−T0 [64], in which α is the the temperature coefficient of resistance (TCR) value. The thin-film TCR values have to be measured as they differ from the bulk TCR values due to its dependency on layer purity, grain size, and deposition method [65,66]. Belser and Hicklin also lists other attributes, such as surface roughness, porosity, and adsorbed materials present in or on the substrate which could influence the TCR value [64]. The bulk TCR values are 0.0034 K−1 and 0.0037 K−1 for Au and Pt [67].\nThe TCR characterizations of the metal strips on a COC substrate did not yield trustworthy TCR values at the first cycle. The first temperature cycle can be seen as a kind of thermal annealing, and therefore gives an hysteresis in the graphs, as can be seen in Figure A2 in Appendix C.1. After this first cycle, the values more or less show the linear behavior. The resulting TCR of this linear part is in agreement with the TCR ranges of Belser and Hicklin [64] and is given in Table 4. Belser and Hicklin used for their experiments substrates with coefficients of linear thermal expansion lower than 1.2 × 10−5 °C−1 [64]. The coefficient of linear thermal expansion for Au and Pt are 1.42 × 10−5 K−1 and 0.88 × 10−5 K−1, respectively [68]. COC of the grade TOPAS 6017 has a coefficient of linear thermal expansion of 6.0 × 10−5 K−1 [42]. This mismatch in coefficients of linear thermal expansion can give strain in the metal layers. Both Au [69,70,71] and Pt [72,73,74] are used as strain-sensitive gauges, and thus are sensitive to strain-induced geometry changes due to thermal expansion.\nAnother effect influencing the TCR value of the metal layer is aging. As can be seen in Figure A3 in Appendix C.2, the TCR value already changes after two weeks storing in ambient conditions. This could be due to adsorbed materials present on the surface [64].\nHowever, in this device, the TCR is not of importance as the metal structure will not be used as temperature sensor. Real-time temperature sensing is done using a thermocouple in the temperature monitor chamber. The resistance of the heater structure changes with temperature; thus, the dissipated power changes when a fixed voltage or current is used. However, the results in Section 3.4 show a 25 h stability test with a constant input potential and only a ±1.5 °C deviation. The TCR can become more important when other (higher) temperatures are required for the amplification.\nBased on the results in Table 4, the choice of heater material and deposition method to be used in the actual device is Au deposited using sputtering. Sputtering is an industrial-scale technique that is already being used in, for example, the car mirror and headlight industry [75].\n\n3.4. Chip Functioning\nCharacterization of the actual heat distribution is done using a FLIR One Pro iOS thermal camera (FLIR Systems, Inc., Wilsonville, OR, USA). Thermal images of the heat distribution are made at the side of the substrate without the resistor, whereas different input powers are used to heat up the heater. Au reflects the infrared radiation of the environment directly, therefore an image with the resistor facing the camera would give a heat map of the surrounding and not of the real temperature of the heater. These measurements also gives a better insight of the heat distribution inside the reaction chamber. The images are processed using the FLIR postprocessing freeware. Results of these measurements are shown in Figure 11a,b. The results are in good agreement with the estimations in Table 1. The slight deviation between the values can be explained by the fact that the heated area in the calculations had an assumed value, the thermal camera measurements used 1.5 mm thick COC substrates without a water-filled chamber, the actual resistors have small parts wich have a double thickness due to the two used shadow masks, and rounding of the values used in the calculations.\nThe reliability of the heater is tested by inserting the thermocouple into the temperature control chamber (see Figure 3a). A constant input potential of 4 V is applied using the Keithley source and the temperature is measured for 25 h. This exceeds the required operation time at least twelve-fold, meaning that it is a good indication for the reliability of the heater and thermocouple. The results are shown in Figure 11c.\nTo perform on-chip amplifications, the resistive heater on the chip is connected to the Keithley source using crocodile connections and the thermocouple is inserted in the temperature control chamber and connected to a Tenma 72-7715 Thermometer (see Figure 12).\n\n3.5. DNA Amplification\nFirst, to determine the temperature window of operation, MDA reactions are performed at 25 °C and 30 °C using the Illustra GenomiPhi V2 DNA amplification kit and EvaGreen fluorescence dye. From the literature, we know that this reaction does not work above 35 °C due to degradation of the protein activity in presence of a substrate [44]. In Figure 13, a graph of the fluorescence signal during MDA reactions at 25 °C and 30 °C, together with their non template control (NTC) is shown. These reactions are carried out in a conventional Bio-Rad CFX96 Touch Real-Time PCR machine (Bio-Rad Laboratories, Inc., Hercules, CA, USA) and the results show that the chosen proof-of-principle DNA amplification reaction is temperature dependent to some extent, but that there is a wide range of temperatures at which the amplification can be performed, i.e., 25°C to 35°C. This makes the functioning of the integrated resistive heater less critical than the stability shown in Figure 11c.\nMDA reactions are also performed inside an Eppendorf tube (Eppendorf AG, Hamburg, Germany) and inside the chip, again using the Illustra GenomiPhi V2 DNA amplification kit and EvaGreen fluorescence dye. As heat supply the water bath of an IKA Rotary Evaporator RV 8V (IKA-Werke, Staufen im Breisgau, Germany) is used. This water bath is according to its specification stable within a range of the set temperature ±0.1 °C. The chip and an Eppendorf tube are loaded with the reaction mixture containing the DNA sample and the EvaGreen dye solution. Here, the Eppendorf tube is serving as a control to show that the fabrication steps of the chips are not inhibiting the MDA reaction. The inlet and outlet of the chip are sealed with the Microseal “B” PCR plate sealing foil. The closed chip and tube are heated up in a separate water bath to 95 °C and kept at that temperature for 3 min to denaturate the dsDNA. Subsequently, the chip and tube are cooled down by placing it in an ice bath for 5 min after which the rest of the reagents are added. The complete mixtures are according to Table A3 in Appendix D. After closing the chip and tube again, they are placed in the water bath of the rotary evaporater and left there for 90 min, after which the reaction is terminated at 65 °C.\nThe MDA is also performed inside the chip, but with the integrated Au resistive heater serving as heat source. The set up shown schematically in Figure 12. The same procedure is followed as with the water bath heated test. Denaturation is done in a separate water bath. The heater is driven by an input potential of 3.2 V to get to a temperature of 30 °C and at the end of the reaction, the system is heated up to 65 °C by applying a potential of 9.2 V in order to terminate the amplification. In Figure 14 the logged temperature during the amplification is shown.\nAfter the amplifications, the reaction mixtures are pipetted out of the chips and tubes and into 1 mL quartz cuvettes containing 55 μL MilliQ DI water (Merck Millipore, Burlington, MA, USA). Fluorescence measurements are done in a Horiba Scientific FluoroMax+ spectrofluorometer to verify each amplification. The mixture is excitated at a wavelength of 500 nm and the emission spectrum is measured at wavelengths from 510 nm to 550 nm (bounded EvaGreen dye has a peak at 525 nm [63]). The measured spectra are normalized by subtracting the background signal of a mixture containing only the reaction buffer, the sample buffer, EvaGreen, and DNA. No Enzyme was added to this mixture, therefore no amplification could take place. See Figure 15 for the results obtained in the Eppendorf tube and chips. Figure A4 in Appendix E shows the background signal which is subtracted from all measurements.\nAs can be seen in Figure 15, the spectra of the amplification performed inside the chip, and by applying heat with the water bath as well as with the integrated Au-resistive heater, show the same trend as the amplification performed in the Eppendorf and heated by water bath. There is an order of magnitude difference in the fluorescence signal. However, the fluorescence intensity cannot be used as a value to quantify the amount of DNA. EvaGreen is a bis-intercalating cyanine fluorescence dye consisting of two monomeric DNA-binding dyes which are linked by a flexible spacer. These two DNA-binding dyes bind each in between two base pairs, which make them simple and fast, but also nonuniform and non-specific [44,63]. However, with this dye, a simple yes-or-no answer can be obtained if the amplification took place, as can be seen in Figure 15."}
LitCovid-sentences
{"project":"LitCovid-sentences","denotations":[{"id":"T207","span":{"begin":0,"end":2},"obj":"Sentence"},{"id":"T208","span":{"begin":3,"end":25},"obj":"Sentence"},{"id":"T209","span":{"begin":27,"end":31},"obj":"Sentence"},{"id":"T210","span":{"begin":32,"end":70},"obj":"Sentence"},{"id":"T211","span":{"begin":71,"end":168},"obj":"Sentence"},{"id":"T212","span":{"begin":169,"end":293},"obj":"Sentence"},{"id":"T213","span":{"begin":294,"end":421},"obj":"Sentence"},{"id":"T214","span":{"begin":422,"end":608},"obj":"Sentence"},{"id":"T215","span":{"begin":609,"end":786},"obj":"Sentence"},{"id":"T216","span":{"begin":787,"end":978},"obj":"Sentence"},{"id":"T217","span":{"begin":979,"end":1185},"obj":"Sentence"},{"id":"T218","span":{"begin":1186,"end":1363},"obj":"Sentence"},{"id":"T219","span":{"begin":1364,"end":1478},"obj":"Sentence"},{"id":"T220","span":{"begin":1479,"end":1633},"obj":"Sentence"},{"id":"T221","span":{"begin":1634,"end":1787},"obj":"Sentence"},{"id":"T222","span":{"begin":1788,"end":1951},"obj":"Sentence"},{"id":"T223","span":{"begin":1952,"end":2153},"obj":"Sentence"},{"id":"T224","span":{"begin":2154,"end":2286},"obj":"Sentence"},{"id":"T225","span":{"begin":2287,"end":2426},"obj":"Sentence"},{"id":"T226","span":{"begin":2427,"end":2546},"obj":"Sentence"},{"id":"T227","span":{"begin":2547,"end":2762},"obj":"Sentence"},{"id":"T228","span":{"begin":2763,"end":2898},"obj":"Sentence"},{"id":"T229","span":{"begin":2899,"end":2949},"obj":"Sentence"},{"id":"T230","span":{"begin":2950,"end":3045},"obj":"Sentence"},{"id":"T231","span":{"begin":3046,"end":3144},"obj":"Sentence"},{"id":"T232","span":{"begin":3145,"end":3181},"obj":"Sentence"},{"id":"T233","span":{"begin":3182,"end":3307},"obj":"Sentence"},{"id":"T234","span":{"begin":3309,"end":3313},"obj":"Sentence"},{"id":"T235","span":{"begin":3314,"end":3325},"obj":"Sentence"},{"id":"T236","span":{"begin":3327,"end":3359},"obj":"Sentence"},{"id":"T237","span":{"begin":3360,"end":3454},"obj":"Sentence"},{"id":"T238","span":{"begin":3455,"end":3594},"obj":"Sentence"},{"id":"T239","span":{"begin":3595,"end":3933},"obj":"Sentence"},{"id":"T240","span":{"begin":3934,"end":3968},"obj":"Sentence"},{"id":"T241","span":{"begin":3969,"end":4028},"obj":"Sentence"},{"id":"T242","span":{"begin":4029,"end":4101},"obj":"Sentence"},{"id":"T243","span":{"begin":4102,"end":4301},"obj":"Sentence"},{"id":"T244","span":{"begin":4302,"end":4513},"obj":"Sentence"},{"id":"T245","span":{"begin":4514,"end":4663},"obj":"Sentence"},{"id":"T246","span":{"begin":4664,"end":4777},"obj":"Sentence"},{"id":"T247","span":{"begin":4778,"end":4965},"obj":"Sentence"},{"id":"T248","span":{"begin":4966,"end":5047},"obj":"Sentence"},{"id":"T249","span":{"begin":5048,"end":5148},"obj":"Sentence"},{"id":"T250","span":{"begin":5149,"end":5180},"obj":"Sentence"},{"id":"T251","span":{"begin":5181,"end":5231},"obj":"Sentence"},{"id":"T252","span":{"begin":5232,"end":5471},"obj":"Sentence"},{"id":"T253","span":{"begin":5472,"end":5712},"obj":"Sentence"},{"id":"T254","span":{"begin":5714,"end":5718},"obj":"Sentence"},{"id":"T255","span":{"begin":5719,"end":5733},"obj":"Sentence"},{"id":"T256","span":{"begin":5734,"end":5849},"obj":"Sentence"},{"id":"T257","span":{"begin":5850,"end":6036},"obj":"Sentence"},{"id":"T258","span":{"begin":6037,"end":6295},"obj":"Sentence"},{"id":"T259","span":{"begin":6296,"end":6348},"obj":"Sentence"},{"id":"T260","span":{"begin":6349,"end":6664},"obj":"Sentence"},{"id":"T261","span":{"begin":6665,"end":6831},"obj":"Sentence"},{"id":"T262","span":{"begin":6832,"end":7012},"obj":"Sentence"},{"id":"T263","span":{"begin":7013,"end":7082},"obj":"Sentence"},{"id":"T264","span":{"begin":7083,"end":7204},"obj":"Sentence"},{"id":"T265","span":{"begin":7205,"end":7370},"obj":"Sentence"},{"id":"T266","span":{"begin":7371,"end":7444},"obj":"Sentence"},{"id":"T267","span":{"begin":7445,"end":7570},"obj":"Sentence"},{"id":"T268","span":{"begin":7571,"end":7706},"obj":"Sentence"},{"id":"T269","span":{"begin":7707,"end":7824},"obj":"Sentence"},{"id":"T270","span":{"begin":7825,"end":7922},"obj":"Sentence"},{"id":"T271","span":{"begin":7923,"end":8017},"obj":"Sentence"},{"id":"T272","span":{"begin":8018,"end":8175},"obj":"Sentence"},{"id":"T273","span":{"begin":8176,"end":8245},"obj":"Sentence"},{"id":"T274","span":{"begin":8246,"end":8367},"obj":"Sentence"},{"id":"T275","span":{"begin":8368,"end":8436},"obj":"Sentence"},{"id":"T276","span":{"begin":8437,"end":8553},"obj":"Sentence"},{"id":"T277","span":{"begin":8554,"end":8648},"obj":"Sentence"},{"id":"T278","span":{"begin":8649,"end":8789},"obj":"Sentence"},{"id":"T279","span":{"begin":8790,"end":8914},"obj":"Sentence"},{"id":"T280","span":{"begin":8915,"end":9017},"obj":"Sentence"},{"id":"T281","span":{"begin":9018,"end":9168},"obj":"Sentence"},{"id":"T282","span":{"begin":9169,"end":9300},"obj":"Sentence"},{"id":"T283","span":{"begin":9302,"end":9306},"obj":"Sentence"},{"id":"T284","span":{"begin":9307,"end":9323},"obj":"Sentence"},{"id":"T285","span":{"begin":9324,"end":9464},"obj":"Sentence"},{"id":"T286","span":{"begin":9465,"end":9627},"obj":"Sentence"},{"id":"T287","span":{"begin":9628,"end":9834},"obj":"Sentence"},{"id":"T288","span":{"begin":9835,"end":9935},"obj":"Sentence"},{"id":"T289","span":{"begin":9936,"end":10000},"obj":"Sentence"},{"id":"T290","span":{"begin":10001,"end":10057},"obj":"Sentence"},{"id":"T291","span":{"begin":10058,"end":10124},"obj":"Sentence"},{"id":"T292","span":{"begin":10125,"end":10507},"obj":"Sentence"},{"id":"T293","span":{"begin":10508,"end":10631},"obj":"Sentence"},{"id":"T294","span":{"begin":10632,"end":10744},"obj":"Sentence"},{"id":"T295","span":{"begin":10745,"end":10896},"obj":"Sentence"},{"id":"T296","span":{"begin":10897,"end":10933},"obj":"Sentence"},{"id":"T297","span":{"begin":10934,"end":11195},"obj":"Sentence"},{"id":"T298","span":{"begin":11197,"end":11201},"obj":"Sentence"},{"id":"T299","span":{"begin":11202,"end":11219},"obj":"Sentence"},{"id":"T300","span":{"begin":11220,"end":11408},"obj":"Sentence"},{"id":"T301","span":{"begin":11409,"end":11558},"obj":"Sentence"},{"id":"T302","span":{"begin":11559,"end":11705},"obj":"Sentence"},{"id":"T303","span":{"begin":11706,"end":12081},"obj":"Sentence"},{"id":"T304","span":{"begin":12082,"end":12197},"obj":"Sentence"},{"id":"T305","span":{"begin":12198,"end":12400},"obj":"Sentence"},{"id":"T306","span":{"begin":12401,"end":12515},"obj":"Sentence"},{"id":"T307","span":{"begin":12516,"end":12619},"obj":"Sentence"},{"id":"T308","span":{"begin":12620,"end":12744},"obj":"Sentence"},{"id":"T309","span":{"begin":12745,"end":12878},"obj":"Sentence"},{"id":"T310","span":{"begin":12879,"end":12969},"obj":"Sentence"},{"id":"T311","span":{"begin":12970,"end":13106},"obj":"Sentence"},{"id":"T312","span":{"begin":13107,"end":13241},"obj":"Sentence"},{"id":"T313","span":{"begin":13242,"end":13304},"obj":"Sentence"},{"id":"T314","span":{"begin":13305,"end":13478},"obj":"Sentence"},{"id":"T315","span":{"begin":13479,"end":13589},"obj":"Sentence"},{"id":"T316","span":{"begin":13590,"end":13634},"obj":"Sentence"},{"id":"T317","span":{"begin":13635,"end":13701},"obj":"Sentence"},{"id":"T318","span":{"begin":13702,"end":13748},"obj":"Sentence"},{"id":"T319","span":{"begin":13749,"end":13972},"obj":"Sentence"},{"id":"T320","span":{"begin":13973,"end":14043},"obj":"Sentence"},{"id":"T321","span":{"begin":14044,"end":14234},"obj":"Sentence"},{"id":"T322","span":{"begin":14235,"end":14352},"obj":"Sentence"},{"id":"T323","span":{"begin":14353,"end":14528},"obj":"Sentence"},{"id":"T324","span":{"begin":14529,"end":14689},"obj":"Sentence"},{"id":"T325","span":{"begin":14690,"end":14771},"obj":"Sentence"},{"id":"T326","span":{"begin":14772,"end":14843},"obj":"Sentence"},{"id":"T327","span":{"begin":14844,"end":14938},"obj":"Sentence"},{"id":"T328","span":{"begin":14939,"end":15214},"obj":"Sentence"},{"id":"T329","span":{"begin":15215,"end":15284},"obj":"Sentence"},{"id":"T330","span":{"begin":15285,"end":15377},"obj":"Sentence"},{"id":"T331","span":{"begin":15378,"end":15518},"obj":"Sentence"},{"id":"T332","span":{"begin":15519,"end":15661},"obj":"Sentence"},{"id":"T333","span":{"begin":15662,"end":15789},"obj":"Sentence"}],"namespaces":[{"prefix":"_base","uri":"http://pubannotation.org/ontology/tao.owl#"}],"text":"3. Results and Discussion\n\n3.1. COMSOL MultiPhysics Simulation Results\nIn Figure 5, the results of heat transfer simulations of two different heater spacings are shown. The heater width for both geometries is 0.3 mm, while the heater spacing in Figure 5b,c are 0.3 mm and 2.0 mm, respectively. In Figure 6a–d, tables with the results of the full parametric sweep for different heater widths and heater spacings are shown. Figure 6a shows the temperature deviation between the highest and lowest temperature at the top of the chamber, i.e., the second H2O and COC interface (ΔTtopofchamber=Ttop,max−Ttop,min). Figure 6b shows the deviation between the highest and lowest temperature inside the chamber, i.e., between the two COC and H2O interfaces (ΔTacrosschamber=Tbottom,max−Ttop,min). Figure 6c shows the temperature deviation between the highest and lowest temperature at the bottom of the chamber, i.e., the first COC and H2O interface (ΔTbottomofchamber=Tbot,max−Tbot,min). Figure 6d shows the deviation between the set heater temperature of 30 °C and the lowest temperature at the top of the chamber, i.e., the second H2O and COC interface (ΔTdeviationfromsetT=Theater−Ttop,min). As can be seen from the results in Figure 6, a combination of small heater widths and heater spacings will result in smaller temperature differences inside the reaction mixture. This is evident as smaller heater spacings will result in a better coverage of the heated area by heater material. The smaller heater widths will result in a smaller heater cross-sectional area, and thus can be operated at lower powers, as is evident from Equation (1). Resulting in the fact that a densely packed meander structure with small heater widths and small heater spacings can dissipate more heat into the system.\nBased on these results and its simplicity, a meandering heater pattern of a heater with a width of 0.3 mm and a spacing of 0.3 mm in between the lines is designed. A side note on the chosen heater width and heater spacing is that according to the simulations, the temperature differences within the chamber are less than ±0.3 °C for the most unfavorable dimensions. This temperature difference is still well-accepted in the temperature window in which the MDA reaction takes place (25 °C to 35 °C). However, as pointed out, a smaller cross-sectional area will result in a lower power consumption and therefore these dimensions are chosen. It is known that a meandering heater structure does not give the optimal temperature distribution over the device [26]. Therefore, the heater lines are longer than the width of the reaction chamber, and thus also covering the bulk material outside the chamber in order to improve the temperature uniformity inside the reaction mixture.\nThe heater pattern is divided over two shadow masks to minimize the length of the narrow Mo tracks in between the meandering structure. This prevents curvature due to intrinsic stresses. See Figure 7 for the outlines of both shadow masks, together with the resulting pattern on COC. The use of two shadow masks will give a metal track in which small parts has the double thickness. Here, the temperature will be lower. The system is designed such that these thicker parts are outside the reaction chamber and temperature control chamber region.\n\n3.2. Fabrication\n\nMilling and Optical Transparency\nThe milling increased the surface roughness of the COC plates also increases the surface area. Inhibition of the amplification can be caused by large surface areas as the used chemicals have more surface to have interaction with [44]. The created surface roughness is visualized using a FEI Sirion high resolution scanning electron microscope (HR-SEM) (FEI Company, Hillsboro, OR, USA) and measured using a Bruker Icon Dimension AFM in tapping mode with Bruker Tespa-V2 cantilevers (Bruker Nano Surfaces, Santa Barbara, CA, USA) and Gwyddion 2.52 open source freeware [62]. The results are shown in Figure 8. The surface roughness of pristine COC had a RRMS of 3.5 nm. This increased two orders of magnitude after milling (RRMS of 310.1 nm). With the reported surface treatment [44,59] we were capable of decreasing the surface roughness to a value even lower than that of pristine COC and the lowest reported in literature (RRMS of 0.9 nm). For this grade of COC (TOPAS 6017) it worked the best to do four short exposures of 5 s, with N2 blow drying after each exposure, instead of one longer exposure, as is more common in other grades of COC [44,59]. The difference in duration for the cyclohexane vapor post-treatment can be explained by the different ratios of the copolymers present in each grade. As the grade number increase, the ratio changes towards more norbornene monomers and less linear ethene monomers. The norbornene is more apolar due to the bridged cyclic hydrocarbon present in its molecular structure and therefore, will dissolve faster in non-polar solvents, like cyclohexane (vapor).\nLowering the surface roughness also increased the optical transmittance fivefold. Transmittance measurements in the visible range are done using a Woollam M-2000UI ellipsometer (J.A. Woollam Co., Lincoln, NE, USA). The results can be seen in Figure 9 and Figure 10. Having a high optical transparency in the visible range can be desired when in situ fluorescence detection will be implemented (e.g., EvaGreen fluorescence dye has an excitation wavelength of 500 nm and emission wavelength of 525 nm [63]). However, as in situ fluorescence detection is not used yet in this system and can also be done through the transparent PCR plate sealing foil, no further effort is put into optimizing this procedure to get even better optical transmittance.\n\n3.3. Metal Adhesion\nTo get reliable heaters, four possible options are investigated for their adhesion properties to the COC substrate. The adhesion of Au and Pt deposited by either evaporation or DC magnetron sputtering is investigated using the Scotch tape test [60,61] before and after temperature cycling up to 100 °C. Test patterns consisting of rectangular metal strips of 2 mm by 14 mm are fabricated by depositing 100 nm of metal using a hand-made shadow mask made out of DuPont Kapton® HN polyimide film of 0.05 mm thickness (RS Components B.V., Haarlem, The Netherlands). See Table 4 for the results of the Scotch tape test.\nNormally, heating up a glass or Si substrate with thin metal strips while measuring the resistance (RT) in these metal strips at certain temperature intervals (T) yields directly a linear relation, which can be fitted with RT/R0=1+αT−T0 [64], in which α is the the temperature coefficient of resistance (TCR) value. The thin-film TCR values have to be measured as they differ from the bulk TCR values due to its dependency on layer purity, grain size, and deposition method [65,66]. Belser and Hicklin also lists other attributes, such as surface roughness, porosity, and adsorbed materials present in or on the substrate which could influence the TCR value [64]. The bulk TCR values are 0.0034 K−1 and 0.0037 K−1 for Au and Pt [67].\nThe TCR characterizations of the metal strips on a COC substrate did not yield trustworthy TCR values at the first cycle. The first temperature cycle can be seen as a kind of thermal annealing, and therefore gives an hysteresis in the graphs, as can be seen in Figure A2 in Appendix C.1. After this first cycle, the values more or less show the linear behavior. The resulting TCR of this linear part is in agreement with the TCR ranges of Belser and Hicklin [64] and is given in Table 4. Belser and Hicklin used for their experiments substrates with coefficients of linear thermal expansion lower than 1.2 × 10−5 °C−1 [64]. The coefficient of linear thermal expansion for Au and Pt are 1.42 × 10−5 K−1 and 0.88 × 10−5 K−1, respectively [68]. COC of the grade TOPAS 6017 has a coefficient of linear thermal expansion of 6.0 × 10−5 K−1 [42]. This mismatch in coefficients of linear thermal expansion can give strain in the metal layers. Both Au [69,70,71] and Pt [72,73,74] are used as strain-sensitive gauges, and thus are sensitive to strain-induced geometry changes due to thermal expansion.\nAnother effect influencing the TCR value of the metal layer is aging. As can be seen in Figure A3 in Appendix C.2, the TCR value already changes after two weeks storing in ambient conditions. This could be due to adsorbed materials present on the surface [64].\nHowever, in this device, the TCR is not of importance as the metal structure will not be used as temperature sensor. Real-time temperature sensing is done using a thermocouple in the temperature monitor chamber. The resistance of the heater structure changes with temperature; thus, the dissipated power changes when a fixed voltage or current is used. However, the results in Section 3.4 show a 25 h stability test with a constant input potential and only a ±1.5 °C deviation. The TCR can become more important when other (higher) temperatures are required for the amplification.\nBased on the results in Table 4, the choice of heater material and deposition method to be used in the actual device is Au deposited using sputtering. Sputtering is an industrial-scale technique that is already being used in, for example, the car mirror and headlight industry [75].\n\n3.4. Chip Functioning\nCharacterization of the actual heat distribution is done using a FLIR One Pro iOS thermal camera (FLIR Systems, Inc., Wilsonville, OR, USA). Thermal images of the heat distribution are made at the side of the substrate without the resistor, whereas different input powers are used to heat up the heater. Au reflects the infrared radiation of the environment directly, therefore an image with the resistor facing the camera would give a heat map of the surrounding and not of the real temperature of the heater. These measurements also gives a better insight of the heat distribution inside the reaction chamber. The images are processed using the FLIR postprocessing freeware. Results of these measurements are shown in Figure 11a,b. The results are in good agreement with the estimations in Table 1. The slight deviation between the values can be explained by the fact that the heated area in the calculations had an assumed value, the thermal camera measurements used 1.5 mm thick COC substrates without a water-filled chamber, the actual resistors have small parts wich have a double thickness due to the two used shadow masks, and rounding of the values used in the calculations.\nThe reliability of the heater is tested by inserting the thermocouple into the temperature control chamber (see Figure 3a). A constant input potential of 4 V is applied using the Keithley source and the temperature is measured for 25 h. This exceeds the required operation time at least twelve-fold, meaning that it is a good indication for the reliability of the heater and thermocouple. The results are shown in Figure 11c.\nTo perform on-chip amplifications, the resistive heater on the chip is connected to the Keithley source using crocodile connections and the thermocouple is inserted in the temperature control chamber and connected to a Tenma 72-7715 Thermometer (see Figure 12).\n\n3.5. DNA Amplification\nFirst, to determine the temperature window of operation, MDA reactions are performed at 25 °C and 30 °C using the Illustra GenomiPhi V2 DNA amplification kit and EvaGreen fluorescence dye. From the literature, we know that this reaction does not work above 35 °C due to degradation of the protein activity in presence of a substrate [44]. In Figure 13, a graph of the fluorescence signal during MDA reactions at 25 °C and 30 °C, together with their non template control (NTC) is shown. These reactions are carried out in a conventional Bio-Rad CFX96 Touch Real-Time PCR machine (Bio-Rad Laboratories, Inc., Hercules, CA, USA) and the results show that the chosen proof-of-principle DNA amplification reaction is temperature dependent to some extent, but that there is a wide range of temperatures at which the amplification can be performed, i.e., 25°C to 35°C. This makes the functioning of the integrated resistive heater less critical than the stability shown in Figure 11c.\nMDA reactions are also performed inside an Eppendorf tube (Eppendorf AG, Hamburg, Germany) and inside the chip, again using the Illustra GenomiPhi V2 DNA amplification kit and EvaGreen fluorescence dye. As heat supply the water bath of an IKA Rotary Evaporator RV 8V (IKA-Werke, Staufen im Breisgau, Germany) is used. This water bath is according to its specification stable within a range of the set temperature ±0.1 °C. The chip and an Eppendorf tube are loaded with the reaction mixture containing the DNA sample and the EvaGreen dye solution. Here, the Eppendorf tube is serving as a control to show that the fabrication steps of the chips are not inhibiting the MDA reaction. The inlet and outlet of the chip are sealed with the Microseal “B” PCR plate sealing foil. The closed chip and tube are heated up in a separate water bath to 95 °C and kept at that temperature for 3 min to denaturate the dsDNA. Subsequently, the chip and tube are cooled down by placing it in an ice bath for 5 min after which the rest of the reagents are added. The complete mixtures are according to Table A3 in Appendix D. After closing the chip and tube again, they are placed in the water bath of the rotary evaporater and left there for 90 min, after which the reaction is terminated at 65 °C.\nThe MDA is also performed inside the chip, but with the integrated Au resistive heater serving as heat source. The set up shown schematically in Figure 12. The same procedure is followed as with the water bath heated test. Denaturation is done in a separate water bath. The heater is driven by an input potential of 3.2 V to get to a temperature of 30 °C and at the end of the reaction, the system is heated up to 65 °C by applying a potential of 9.2 V in order to terminate the amplification. In Figure 14 the logged temperature during the amplification is shown.\nAfter the amplifications, the reaction mixtures are pipetted out of the chips and tubes and into 1 mL quartz cuvettes containing 55 μL MilliQ DI water (Merck Millipore, Burlington, MA, USA). Fluorescence measurements are done in a Horiba Scientific FluoroMax+ spectrofluorometer to verify each amplification. The mixture is excitated at a wavelength of 500 nm and the emission spectrum is measured at wavelengths from 510 nm to 550 nm (bounded EvaGreen dye has a peak at 525 nm [63]). The measured spectra are normalized by subtracting the background signal of a mixture containing only the reaction buffer, the sample buffer, EvaGreen, and DNA. No Enzyme was added to this mixture, therefore no amplification could take place. See Figure 15 for the results obtained in the Eppendorf tube and chips. Figure A4 in Appendix E shows the background signal which is subtracted from all measurements.\nAs can be seen in Figure 15, the spectra of the amplification performed inside the chip, and by applying heat with the water bath as well as with the integrated Au-resistive heater, show the same trend as the amplification performed in the Eppendorf and heated by water bath. There is an order of magnitude difference in the fluorescence signal. However, the fluorescence intensity cannot be used as a value to quantify the amount of DNA. EvaGreen is a bis-intercalating cyanine fluorescence dye consisting of two monomeric DNA-binding dyes which are linked by a flexible spacer. These two DNA-binding dyes bind each in between two base pairs, which make them simple and fast, but also nonuniform and non-specific [44,63]. However, with this dye, a simple yes-or-no answer can be obtained if the amplification took place, as can be seen in Figure 15."}