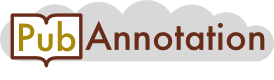
PMC:7143804 / 18842-20197
Annnotations
LitCovid-PubTator
{"project":"LitCovid-PubTator","denotations":[{"id":"119","span":{"begin":325,"end":328},"obj":"Chemical"},{"id":"120","span":{"begin":396,"end":399},"obj":"Chemical"},{"id":"121","span":{"begin":809,"end":812},"obj":"Chemical"},{"id":"122","span":{"begin":813,"end":816},"obj":"Chemical"},{"id":"123","span":{"begin":817,"end":820},"obj":"Chemical"}],"namespaces":[{"prefix":"Tax","uri":"https://www.ncbi.nlm.nih.gov/taxonomy/"},{"prefix":"MESH","uri":"https://id.nlm.nih.gov/mesh/"},{"prefix":"Gene","uri":"https://www.ncbi.nlm.nih.gov/gene/"},{"prefix":"CVCL","uri":"https://web.expasy.org/cellosaurus/CVCL_"}],"text":"To determine the optimal heater width and heater spacing in the heated area, a parametric study using COMSOL Multiphysics 5.3a finite element method simulations with the Heat Transfer in Solids (ht) package is done (COMSOL Inc., Burlington, MA, USA). The model is designed such that it consists of two parallel rectangles of COC (in the real device, the upper plate is an adhesive PCR foil) with H2O in between. The meandering heater are assumed to be lines at the bottom side of the layer stack. This reduces the required complexity of the mesh tremendously, as the heater in the real device will be approximately 100 nm in thickness. The heater temperature is set at a constant temperature of 303.15 K. This makes the heater material independent and the model purely focused on the heat transfer inside the COC–H2O–COC stack. All used values and equations are given in Appendix B. The layer stack is meshed with an extremely fine mapped mesh consisting of 280.650 elements with average quality of 0.9966. A parametric sweep from 0.3 mm to 2.0 mm, in steps of 0.1 mm, is done for both the heater width (wheater) and the heater spacing (sheater), giving 324 combinations. The simulations are solved by using the fully coupled, direct Pardiso solver on a custom-build and 40% CPU overclocked simulation computer, containing the equipment listed in Table 2."}
LitCovid-PD-FMA-UBERON
{"project":"LitCovid-PD-FMA-UBERON","denotations":[{"id":"T45","span":{"begin":871,"end":879},"obj":"Body_part"}],"attributes":[{"id":"A45","pred":"fma_id","subj":"T45","obj":"http://purl.org/sig/ont/fma/fma14542"}],"text":"To determine the optimal heater width and heater spacing in the heated area, a parametric study using COMSOL Multiphysics 5.3a finite element method simulations with the Heat Transfer in Solids (ht) package is done (COMSOL Inc., Burlington, MA, USA). The model is designed such that it consists of two parallel rectangles of COC (in the real device, the upper plate is an adhesive PCR foil) with H2O in between. The meandering heater are assumed to be lines at the bottom side of the layer stack. This reduces the required complexity of the mesh tremendously, as the heater in the real device will be approximately 100 nm in thickness. The heater temperature is set at a constant temperature of 303.15 K. This makes the heater material independent and the model purely focused on the heat transfer inside the COC–H2O–COC stack. All used values and equations are given in Appendix B. The layer stack is meshed with an extremely fine mapped mesh consisting of 280.650 elements with average quality of 0.9966. A parametric sweep from 0.3 mm to 2.0 mm, in steps of 0.1 mm, is done for both the heater width (wheater) and the heater spacing (sheater), giving 324 combinations. The simulations are solved by using the fully coupled, direct Pardiso solver on a custom-build and 40% CPU overclocked simulation computer, containing the equipment listed in Table 2."}
LitCovid-PD-CLO
{"project":"LitCovid-PD-CLO","denotations":[{"id":"T128","span":{"begin":77,"end":78},"obj":"http://purl.obolibrary.org/obo/CLO_0001020"},{"id":"T129","span":{"begin":195,"end":197},"obj":"http://purl.obolibrary.org/obo/CLO_0004265"},{"id":"T130","span":{"begin":342,"end":348},"obj":"http://purl.obolibrary.org/obo/OBI_0000968"},{"id":"T131","span":{"begin":586,"end":592},"obj":"http://purl.obolibrary.org/obo/OBI_0000968"},{"id":"T132","span":{"begin":669,"end":670},"obj":"http://purl.obolibrary.org/obo/CLO_0001020"},{"id":"T133","span":{"begin":769,"end":776},"obj":"http://purl.obolibrary.org/obo/CLO_0009985"},{"id":"T134","span":{"begin":880,"end":881},"obj":"http://purl.obolibrary.org/obo/CLO_0001021"},{"id":"T135","span":{"begin":917,"end":926},"obj":"http://www.ebi.ac.uk/efo/EFO_0000876"},{"id":"T136","span":{"begin":1007,"end":1008},"obj":"http://purl.obolibrary.org/obo/CLO_0001020"},{"id":"T137","span":{"begin":1252,"end":1253},"obj":"http://purl.obolibrary.org/obo/CLO_0001020"}],"text":"To determine the optimal heater width and heater spacing in the heated area, a parametric study using COMSOL Multiphysics 5.3a finite element method simulations with the Heat Transfer in Solids (ht) package is done (COMSOL Inc., Burlington, MA, USA). The model is designed such that it consists of two parallel rectangles of COC (in the real device, the upper plate is an adhesive PCR foil) with H2O in between. The meandering heater are assumed to be lines at the bottom side of the layer stack. This reduces the required complexity of the mesh tremendously, as the heater in the real device will be approximately 100 nm in thickness. The heater temperature is set at a constant temperature of 303.15 K. This makes the heater material independent and the model purely focused on the heat transfer inside the COC–H2O–COC stack. All used values and equations are given in Appendix B. The layer stack is meshed with an extremely fine mapped mesh consisting of 280.650 elements with average quality of 0.9966. A parametric sweep from 0.3 mm to 2.0 mm, in steps of 0.1 mm, is done for both the heater width (wheater) and the heater spacing (sheater), giving 324 combinations. The simulations are solved by using the fully coupled, direct Pardiso solver on a custom-build and 40% CPU overclocked simulation computer, containing the equipment listed in Table 2."}
LitCovid-PD-CHEBI
{"project":"LitCovid-PD-CHEBI","denotations":[{"id":"T104","span":{"begin":241,"end":243},"obj":"Chemical"},{"id":"T107","span":{"begin":325,"end":328},"obj":"Chemical"},{"id":"T108","span":{"begin":396,"end":399},"obj":"Chemical"},{"id":"T109","span":{"begin":809,"end":812},"obj":"Chemical"},{"id":"T110","span":{"begin":813,"end":816},"obj":"Chemical"},{"id":"T111","span":{"begin":817,"end":820},"obj":"Chemical"}],"attributes":[{"id":"A104","pred":"chebi_id","subj":"T104","obj":"http://purl.obolibrary.org/obo/CHEBI_474859"},{"id":"A105","pred":"chebi_id","subj":"T104","obj":"http://purl.obolibrary.org/obo/CHEBI_73610"},{"id":"A106","pred":"chebi_id","subj":"T104","obj":"http://purl.obolibrary.org/obo/CHEBI_90325"},{"id":"A107","pred":"chebi_id","subj":"T107","obj":"http://purl.obolibrary.org/obo/CHEBI_53310"},{"id":"A108","pred":"chebi_id","subj":"T108","obj":"http://purl.obolibrary.org/obo/CHEBI_15377"},{"id":"A109","pred":"chebi_id","subj":"T109","obj":"http://purl.obolibrary.org/obo/CHEBI_53310"},{"id":"A110","pred":"chebi_id","subj":"T110","obj":"http://purl.obolibrary.org/obo/CHEBI_15377"},{"id":"A111","pred":"chebi_id","subj":"T111","obj":"http://purl.obolibrary.org/obo/CHEBI_53310"}],"text":"To determine the optimal heater width and heater spacing in the heated area, a parametric study using COMSOL Multiphysics 5.3a finite element method simulations with the Heat Transfer in Solids (ht) package is done (COMSOL Inc., Burlington, MA, USA). The model is designed such that it consists of two parallel rectangles of COC (in the real device, the upper plate is an adhesive PCR foil) with H2O in between. The meandering heater are assumed to be lines at the bottom side of the layer stack. This reduces the required complexity of the mesh tremendously, as the heater in the real device will be approximately 100 nm in thickness. The heater temperature is set at a constant temperature of 303.15 K. This makes the heater material independent and the model purely focused on the heat transfer inside the COC–H2O–COC stack. All used values and equations are given in Appendix B. The layer stack is meshed with an extremely fine mapped mesh consisting of 280.650 elements with average quality of 0.9966. A parametric sweep from 0.3 mm to 2.0 mm, in steps of 0.1 mm, is done for both the heater width (wheater) and the heater spacing (sheater), giving 324 combinations. The simulations are solved by using the fully coupled, direct Pardiso solver on a custom-build and 40% CPU overclocked simulation computer, containing the equipment listed in Table 2."}
LitCovid-sentences
{"project":"LitCovid-sentences","denotations":[{"id":"T150","span":{"begin":0,"end":250},"obj":"Sentence"},{"id":"T151","span":{"begin":251,"end":411},"obj":"Sentence"},{"id":"T152","span":{"begin":412,"end":496},"obj":"Sentence"},{"id":"T153","span":{"begin":497,"end":635},"obj":"Sentence"},{"id":"T154","span":{"begin":636,"end":704},"obj":"Sentence"},{"id":"T155","span":{"begin":705,"end":827},"obj":"Sentence"},{"id":"T156","span":{"begin":828,"end":882},"obj":"Sentence"},{"id":"T157","span":{"begin":883,"end":1006},"obj":"Sentence"},{"id":"T158","span":{"begin":1007,"end":1171},"obj":"Sentence"},{"id":"T159","span":{"begin":1172,"end":1355},"obj":"Sentence"}],"namespaces":[{"prefix":"_base","uri":"http://pubannotation.org/ontology/tao.owl#"}],"text":"To determine the optimal heater width and heater spacing in the heated area, a parametric study using COMSOL Multiphysics 5.3a finite element method simulations with the Heat Transfer in Solids (ht) package is done (COMSOL Inc., Burlington, MA, USA). The model is designed such that it consists of two parallel rectangles of COC (in the real device, the upper plate is an adhesive PCR foil) with H2O in between. The meandering heater are assumed to be lines at the bottom side of the layer stack. This reduces the required complexity of the mesh tremendously, as the heater in the real device will be approximately 100 nm in thickness. The heater temperature is set at a constant temperature of 303.15 K. This makes the heater material independent and the model purely focused on the heat transfer inside the COC–H2O–COC stack. All used values and equations are given in Appendix B. The layer stack is meshed with an extremely fine mapped mesh consisting of 280.650 elements with average quality of 0.9966. A parametric sweep from 0.3 mm to 2.0 mm, in steps of 0.1 mm, is done for both the heater width (wheater) and the heater spacing (sheater), giving 324 combinations. The simulations are solved by using the fully coupled, direct Pardiso solver on a custom-build and 40% CPU overclocked simulation computer, containing the equipment listed in Table 2."}