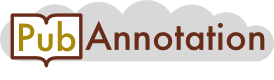
PMC:5551755 / 1196-5111
Annnotations
TEST0
1. Introduction
Clays are abundant natural materials with a low cost. To improve the catalytic and adsorptive properties of these materials, clays can be submitted to different processes, such as pillaring and acid activation. Usually, clay pillaring occurs through cation exchange of natural cations (Ca2+, Na+, Mg2+) present between clay layers for bigger cations such as polyhydroxy cations of Al (a pillaring agent). These larger cations act as pillars, separating the clay layers, increasing the basal space and creating microporosity. The calcination provides stability to the pillared clay, and the resultant material presents small cavities and a large surface area. These properties, combined with the low cost of clay, make pillared clays alternative catalysts to zeolites.
The majority of articles found in the literature use polyhydroxy cations (mostly aluminum, zirconium, iron, and titanium) as pillaring agents [1,2,3]. These cations can be used separately (just one type of pillar) [4,5,6,7,8,9,10] or as mixed pillars [11,12,13,14,15,16,17].
However, most papers about pillared clays report the use of polyhydroxy cations of only aluminum as the pillaring agent. Solutions containing this complex are made through addition of a base (hydroxide or carbonate) to a salt of aluminum (AlCl3 or Al(NO3)3) until a molar ratio of OH/Al = 2.5 is attained or through dissolution of powdered Al in AlCl3 [1]. Solutions prepared with these methods contain mostly three species: hydrated monomeric aluminum, the polyhydroxy cation [Al13O4(OH)24(H2O)12]7+, also known as ε-Keggin ion or Al13, and polynuclear aluminum [18,19,20]. Some of these Al-pillared clays have been reported as support for active phases, such as metals, in catalytic reactions [21,22,23].
Variations in the synthesis provide different characteristics to the resulting materials, and the most important parameters that can be varied are related to the formation, intercalation, and posterior fixation of the polynuclear cations between the clay layers. No general rules exist about the best conditions for the synthesis [24].
Several pillaring methods and pillaring solutions have been reported in the literature. Despite the major studies that have been performed on a laboratory scale (with small quantities of clay), some authors have utilized concentrated suspensions to increase the scale of pillaring [14,25,26,27,28,29,30,31]. In this sense, to reduce the volume of water and intercalation times, Sanabria et al. [14] have performed pillaring procedures by using dialysis membranes and ultrasound to produce pillared clays with mixed Al-Fe, Al-Ce-Fe pillars. By this methodology, they were able to produce pillared clays with similar features to those of the solid synthesized by their conventional procedure.
Nevertheless, a closer look into the literature reveals that an enormous amount of parameters can influence the pillaring processes, like the starting clay material, the synthesis condition and nature of the pillaring agent, the use of concentrated or dilute clay suspensions, time and temperature of intercalation and conditions of washing, drying and calcining processes. In this view, to study a scale-up pillaring process it is of primary importance the optimization of key parameters in order to obtain pillared clays with comparable features (basal spacing and surface areas) similar to the material synthesized by the conventional procedure. To achieve this purpose, a systematic study of the most important variables that influence a scale-up pillaring process, like pillaring method, concentration of clay suspension and amount of clay, using the same starting clay is of paramount importance.
Thus, the aim of the present study is to prepare and characterize pillared clays modifying the conditions of the synthesis to determine which parameters influence the increase in the pillaring scale of a bentonite clay.
2_test
1. Introduction
Clays are abundant natural materials with a low cost. To improve the catalytic and adsorptive properties of these materials, clays can be submitted to different processes, such as pillaring and acid activation. Usually, clay pillaring occurs through cation exchange of natural cations (Ca2+, Na+, Mg2+) present between clay layers for bigger cations such as polyhydroxy cations of Al (a pillaring agent). These larger cations act as pillars, separating the clay layers, increasing the basal space and creating microporosity. The calcination provides stability to the pillared clay, and the resultant material presents small cavities and a large surface area. These properties, combined with the low cost of clay, make pillared clays alternative catalysts to zeolites.
The majority of articles found in the literature use polyhydroxy cations (mostly aluminum, zirconium, iron, and titanium) as pillaring agents [1,2,3]. These cations can be used separately (just one type of pillar) [4,5,6,7,8,9,10] or as mixed pillars [11,12,13,14,15,16,17].
However, most papers about pillared clays report the use of polyhydroxy cations of only aluminum as the pillaring agent. Solutions containing this complex are made through addition of a base (hydroxide or carbonate) to a salt of aluminum (AlCl3 or Al(NO3)3) until a molar ratio of OH/Al = 2.5 is attained or through dissolution of powdered Al in AlCl3 [1]. Solutions prepared with these methods contain mostly three species: hydrated monomeric aluminum, the polyhydroxy cation [Al13O4(OH)24(H2O)12]7+, also known as ε-Keggin ion or Al13, and polynuclear aluminum [18,19,20]. Some of these Al-pillared clays have been reported as support for active phases, such as metals, in catalytic reactions [21,22,23].
Variations in the synthesis provide different characteristics to the resulting materials, and the most important parameters that can be varied are related to the formation, intercalation, and posterior fixation of the polynuclear cations between the clay layers. No general rules exist about the best conditions for the synthesis [24].
Several pillaring methods and pillaring solutions have been reported in the literature. Despite the major studies that have been performed on a laboratory scale (with small quantities of clay), some authors have utilized concentrated suspensions to increase the scale of pillaring [14,25,26,27,28,29,30,31]. In this sense, to reduce the volume of water and intercalation times, Sanabria et al. [14] have performed pillaring procedures by using dialysis membranes and ultrasound to produce pillared clays with mixed Al-Fe, Al-Ce-Fe pillars. By this methodology, they were able to produce pillared clays with similar features to those of the solid synthesized by their conventional procedure.
Nevertheless, a closer look into the literature reveals that an enormous amount of parameters can influence the pillaring processes, like the starting clay material, the synthesis condition and nature of the pillaring agent, the use of concentrated or dilute clay suspensions, time and temperature of intercalation and conditions of washing, drying and calcining processes. In this view, to study a scale-up pillaring process it is of primary importance the optimization of key parameters in order to obtain pillared clays with comparable features (basal spacing and surface areas) similar to the material synthesized by the conventional procedure. To achieve this purpose, a systematic study of the most important variables that influence a scale-up pillaring process, like pillaring method, concentration of clay suspension and amount of clay, using the same starting clay is of paramount importance.
Thus, the aim of the present study is to prepare and characterize pillared clays modifying the conditions of the synthesis to determine which parameters influence the increase in the pillaring scale of a bentonite clay.