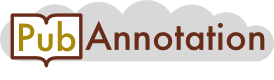
PMC:4534144 / 10971-13089
Annnotations
TEST0
{"project":"TEST0","denotations":[{"id":"26269746-121-127-1455814","span":{"begin":1963,"end":1965},"obj":"[\"17134732\"]"}],"text":"Efficiency Optimization\nBaffles were embedded in the incinerator to remove large rotating currents (or eddy). In the first case, two baffles each with an angle of 90° were installed on the height of 3 and 5 m from the bottom of the studied incinerator. Fig. 4a, shows the two-dimensional motion of particles in this case. The baffles were made of steel as the studied incinerator body. Unlike the previous case, the motion path is divided into several parts. Removal of large eddies and the sudden displacements of gaseous emissions increase the residence time and thereby optimal air mixing. The residence time calculated for this case is 3.3 s. Fig. 4b, shows the temperature profile. The maximum temperature in this case was 1400 °C. Although the heat concentration can be observed in the middle of the studied incinerator, the temperature profile is not significantly different with the previous case.\nFig. 4 a The schematic motion path of gases in the incinerator for the Case 1, (b) The temperature profile (°C) inside the incinerator for the Case 1\nIn the second case, 3 baffles were installed on the height of 2, 4 and 8 m from the bottom of the studied incinerator with an angle of 90 °. Fig. 5a, shows the gas motion path in this case. As shown, the large volume of the incoming gas is located adjacent to the heat source. The gas emission leaves the incinerator with a lower speed across a longer path compared to the previous case. In this case, the turbulent flow in the incinerator is stronger than the previous case. The average residence time is 3.5 s. The temperature profile is shown in Fig. 5b, Little changes in the temperature profile are observed. Like the previous case, the heat concentration is observed in the middle of the incinerator. The maximum temperature in this case is 100 °C higher than the previous case. Other studies have shown that longer path incinerator or multiple chamber incinerator can be increased PCB removal rate [15, 26].\nFig. 5 a Schematic motion path of gases in the incinerator for the Case 2, (b) The temperature profile (°C) inside the incinerator for the case 2"}
2_test
{"project":"2_test","denotations":[{"id":"26269746-17134732-59012432","span":{"begin":1963,"end":1965},"obj":"17134732"}],"text":"Efficiency Optimization\nBaffles were embedded in the incinerator to remove large rotating currents (or eddy). In the first case, two baffles each with an angle of 90° were installed on the height of 3 and 5 m from the bottom of the studied incinerator. Fig. 4a, shows the two-dimensional motion of particles in this case. The baffles were made of steel as the studied incinerator body. Unlike the previous case, the motion path is divided into several parts. Removal of large eddies and the sudden displacements of gaseous emissions increase the residence time and thereby optimal air mixing. The residence time calculated for this case is 3.3 s. Fig. 4b, shows the temperature profile. The maximum temperature in this case was 1400 °C. Although the heat concentration can be observed in the middle of the studied incinerator, the temperature profile is not significantly different with the previous case.\nFig. 4 a The schematic motion path of gases in the incinerator for the Case 1, (b) The temperature profile (°C) inside the incinerator for the Case 1\nIn the second case, 3 baffles were installed on the height of 2, 4 and 8 m from the bottom of the studied incinerator with an angle of 90 °. Fig. 5a, shows the gas motion path in this case. As shown, the large volume of the incoming gas is located adjacent to the heat source. The gas emission leaves the incinerator with a lower speed across a longer path compared to the previous case. In this case, the turbulent flow in the incinerator is stronger than the previous case. The average residence time is 3.5 s. The temperature profile is shown in Fig. 5b, Little changes in the temperature profile are observed. Like the previous case, the heat concentration is observed in the middle of the incinerator. The maximum temperature in this case is 100 °C higher than the previous case. Other studies have shown that longer path incinerator or multiple chamber incinerator can be increased PCB removal rate [15, 26].\nFig. 5 a Schematic motion path of gases in the incinerator for the Case 2, (b) The temperature profile (°C) inside the incinerator for the case 2"}