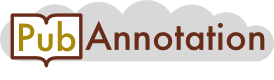
PMC:2871132 / 55389-59195
Annnotations
2_test
{"project":"2_test","denotations":[{"id":"20480036-14530083-52068681","span":{"begin":1741,"end":1744},"obj":"14530083"},{"id":"20480036-10768759-52068682","span":{"begin":2277,"end":2280},"obj":"10768759"},{"id":"20480036-16106434-52068683","span":{"begin":2814,"end":2817},"obj":"16106434"},{"id":"20480036-16106434-52068684","span":{"begin":3801,"end":3804},"obj":"16106434"},{"id":"T41872","span":{"begin":1741,"end":1744},"obj":"14530083"},{"id":"T57608","span":{"begin":2277,"end":2280},"obj":"10768759"},{"id":"T76957","span":{"begin":2814,"end":2817},"obj":"16106434"},{"id":"T59259","span":{"begin":3801,"end":3804},"obj":"16106434"}],"text":"3.2. Shot-Peening and Laser-Peening\nShot peening (which is a similar technique to sand-blasting, but has more controlled peening power, intensity, and direction) is a cold working process in which the surface of a part is bombarded with small spherical media called shot. Each piece of shot striking the material acts as a tiny hammer, imparting to the surface small indentations or dimples. In order for the dimple to be created, the surface fibers of the material must be yielded in tension. Below the surface, the fibers try to restore the surface to its original shape, thereby producing below the dimple a hemisphere of cold-worked material highly stressed in compression. Overlapping dimples (which are sometimes called forged dimples) develop an even layer of metal in residual compressive stress. Both compressive stresses and cold working effects are used in the application of shot peening in forming metal parts, called “shot forming” [132].\nThe laser peening technology is recently developed, claiming non-contact, no-media, and contamination-free peening method [132]. Before treatment, the workpiece is covered with a protective ablative layer (paint or tape) and a thin layer of water. High-intensity (5–15 GW/cm2) nanosecond pulses (10–30 ns) of laser light beam (3–5 mm width) striking the ablative layer generate a short-lived plasma which causes a shock wave to travel into the workpiece. The shock wave induces compressive residual stress that penetrates beneath the surface and strengthens the workpiece [133–136], resulting in improvements in fatigue life and retarding in stress corrosion cracking occurrence. Cho et al. laser-treated CpTi screws and inserted in right tibia metaphysics of white rabbits for 8 weeks [137]. It was reported that (i) SEM of laser-treated implants demonstrated a deep and regular honeycomb pattern with small pores, and (ii) eight weeks implantation, the removal torque was 23.58 N-cm for control machined and 62.57 N-cm for laser-treated implants. Gaggl et al. reported that (i) surfaces of laser-treated Ti implants showed a high purity with appropriate roughness for good osseointegration, and (ii) the laser-treated Ti had regular patterns of micropore with interval of 10–12 μm, diameter of 25 μm, and depth of 20 μm [138].\nAt the end of this section, it is necessary to summarize various techniques to measure and characterize the surface roughness. They include that (1) surface roughness can be measured using a profilometer with sharp edge stylus, which is a contact method, (2) atomic force microscopy can provide non-contact surface topography from which the surface roughness can be indirectly measured, and (3) fractal dimension analysis can be used to present the surface roughness in non-Euclidian dimension [121,124]. Recently, Hansson et al. [139] employed computer simulations to measure surface roughness. The lateral resolution was defined as the pixel size of a profiling system. A surface roughness was simulated by a trigonometric function with random periodicity and amplitude. The function was divided into an array of pixels simulating the pixels of the profiling system. The mean height value for each pixel was used to calculate the surface roughness parameters. It was found that the accuracy of all the surface roughness parameters investigated decreased with increasing pixel size. This tendency was most pronounced for mean slope and developed length ratio, amounting to about 80% of their true values for a pixel size of 20% of the true mean high-spot spacing. It was concluded that the lateral resolution of an instrument/method severely compromises the precision of surface roughness parameters which are measured for roughness features with a mean high-spot spacing less than five times the lateral resolution [139]."}
NEUROSES
{"project":"NEUROSES","denotations":[{"id":"T1241","span":{"begin":130,"end":135},"obj":"PATO_0001024"},{"id":"T1242","span":{"begin":137,"end":146},"obj":"PATO_0000049"},{"id":"T1243","span":{"begin":1207,"end":1216},"obj":"PATO_0000049"},{"id":"T1244","span":{"begin":152,"end":161},"obj":"PATO_0000039"},{"id":"T1245","span":{"begin":168,"end":172},"obj":"PATO_0001306"},{"id":"T1246","span":{"begin":626,"end":630},"obj":"PATO_0001306"},{"id":"T1247","span":{"begin":836,"end":840},"obj":"PATO_0001306"},{"id":"T1248","span":{"begin":181,"end":188},"obj":"PATO_0000006"},{"id":"T1249","span":{"begin":238,"end":243},"obj":"PATO_0000587"},{"id":"T1250","span":{"begin":324,"end":328},"obj":"PATO_0000587"},{"id":"T1251","span":{"begin":362,"end":367},"obj":"PATO_0000587"},{"id":"T1252","span":{"begin":244,"end":253},"obj":"PATO_0001499"},{"id":"T1253","span":{"begin":486,"end":493},"obj":"PATO_0002284"},{"id":"T1254","span":{"begin":568,"end":573},"obj":"PATO_0000052"},{"id":"T1255","span":{"begin":679,"end":690},"obj":"PATO_0002488"},{"id":"T1256","span":{"begin":768,"end":773},"obj":"CHEBI_33521"},{"id":"T1257","span":{"begin":912,"end":917},"obj":"CHEBI_33521"},{"id":"T1258","span":{"begin":873,"end":884},"obj":"CHEBI_33232"},{"id":"T1259","span":{"begin":1056,"end":1060},"obj":"PATO_0002316"},{"id":"T1260","span":{"begin":1195,"end":1200},"obj":"CHEBI_46629"},{"id":"T1261","span":{"begin":1195,"end":1200},"obj":"CHEBI_15377"},{"id":"T1262","span":{"begin":1202,"end":1206},"obj":"PATO_0000469"},{"id":"T1263","span":{"begin":2081,"end":2085},"obj":"PATO_0000469"},{"id":"T1264","span":{"begin":3529,"end":3533},"obj":"PATO_0000469"},{"id":"T1265","span":{"begin":3738,"end":3742},"obj":"PATO_0000469"},{"id":"T1266","span":{"begin":1269,"end":1274},"obj":"CHEBI_30212"},{"id":"T1267","span":{"begin":1269,"end":1274},"obj":"PATO_0000665"},{"id":"T1268","span":{"begin":1288,"end":1293},"obj":"PATO_0000921"},{"id":"T1269","span":{"begin":1334,"end":1339},"obj":"PATO_0000574"},{"id":"T1270","span":{"begin":1334,"end":1339},"obj":"PATO_0000569"},{"id":"T1271","span":{"begin":1622,"end":1632},"obj":"PATO_0000057"},{"id":"T1272","span":{"begin":1634,"end":1637},"obj":"CHEBI_42485"},{"id":"T1273","span":{"begin":1634,"end":1637},"obj":"CHEBI_58072"},{"id":"T1274","span":{"begin":1634,"end":1637},"obj":"CHEBI_29327"},{"id":"T1275","span":{"begin":1675,"end":1683},"obj":"PATO_0000624"},{"id":"T1276","span":{"begin":1687,"end":1692},"obj":"PATO_0000367"},{"id":"T1277","span":{"begin":1714,"end":1719},"obj":"PATO_0000323"},{"id":"T1278","span":{"begin":1772,"end":1775},"obj":"CHEBI_30019"},{"id":"T1279","span":{"begin":1817,"end":1821},"obj":"PATO_0001596"},{"id":"T1280","span":{"begin":1844,"end":1851},"obj":"PATO_0000060"},{"id":"T1281","span":{"begin":1917,"end":1923},"obj":"CHEBI_39294"},{"id":"T1282","span":{"begin":2238,"end":2246},"obj":"PATO_0001334"},{"id":"T1283","span":{"begin":2261,"end":2266},"obj":"PATO_0001595"},{"id":"T1284","span":{"begin":2492,"end":2497},"obj":"PATO_0001419"},{"id":"T1285","span":{"begin":2549,"end":2554},"obj":"PATO_0001035"},{"id":"T1286","span":{"begin":2720,"end":2727},"obj":"PATO_0000467"},{"id":"T1287","span":{"begin":2883,"end":2890},"obj":"PATO_0001193"},{"id":"T1288","span":{"begin":3574,"end":3581},"obj":"PATO_0001193"},{"id":"T1289","span":{"begin":3781,"end":3788},"obj":"PATO_0001193"},{"id":"T1290","span":{"begin":2927,"end":2931},"obj":"PATO_0000117"},{"id":"T1291","span":{"begin":3361,"end":3365},"obj":"PATO_0000117"},{"id":"T1292","span":{"begin":3500,"end":3504},"obj":"PATO_0000117"},{"id":"T1293","span":{"begin":3008,"end":3016},"obj":"PATO_0000173"},{"id":"T1294","span":{"begin":3060,"end":3068},"obj":"PATO_0000173"},{"id":"T1295","span":{"begin":3045,"end":3054},"obj":"PATO_0000080"},{"id":"T1296","span":{"begin":3073,"end":3080},"obj":"PATO_0001786"},{"id":"T1297","span":{"begin":3329,"end":3338},"obj":"PATO_0001997"},{"id":"T1298","span":{"begin":3372,"end":3380},"obj":"PATO_0001727"},{"id":"T1299","span":{"begin":3372,"end":3380},"obj":"PATO_0002360"},{"id":"T1300","span":{"begin":3430,"end":3436},"obj":"PATO_0000122"},{"id":"T1301","span":{"begin":3437,"end":3442},"obj":"PATO_0001038"},{"id":"T1302","span":{"begin":3437,"end":3442},"obj":"PATO_0001470"}],"text":"3.2. Shot-Peening and Laser-Peening\nShot peening (which is a similar technique to sand-blasting, but has more controlled peening power, intensity, and direction) is a cold working process in which the surface of a part is bombarded with small spherical media called shot. Each piece of shot striking the material acts as a tiny hammer, imparting to the surface small indentations or dimples. In order for the dimple to be created, the surface fibers of the material must be yielded in tension. Below the surface, the fibers try to restore the surface to its original shape, thereby producing below the dimple a hemisphere of cold-worked material highly stressed in compression. Overlapping dimples (which are sometimes called forged dimples) develop an even layer of metal in residual compressive stress. Both compressive stresses and cold working effects are used in the application of shot peening in forming metal parts, called “shot forming” [132].\nThe laser peening technology is recently developed, claiming non-contact, no-media, and contamination-free peening method [132]. Before treatment, the workpiece is covered with a protective ablative layer (paint or tape) and a thin layer of water. High-intensity (5–15 GW/cm2) nanosecond pulses (10–30 ns) of laser light beam (3–5 mm width) striking the ablative layer generate a short-lived plasma which causes a shock wave to travel into the workpiece. The shock wave induces compressive residual stress that penetrates beneath the surface and strengthens the workpiece [133–136], resulting in improvements in fatigue life and retarding in stress corrosion cracking occurrence. Cho et al. laser-treated CpTi screws and inserted in right tibia metaphysics of white rabbits for 8 weeks [137]. It was reported that (i) SEM of laser-treated implants demonstrated a deep and regular honeycomb pattern with small pores, and (ii) eight weeks implantation, the removal torque was 23.58 N-cm for control machined and 62.57 N-cm for laser-treated implants. Gaggl et al. reported that (i) surfaces of laser-treated Ti implants showed a high purity with appropriate roughness for good osseointegration, and (ii) the laser-treated Ti had regular patterns of micropore with interval of 10–12 μm, diameter of 25 μm, and depth of 20 μm [138].\nAt the end of this section, it is necessary to summarize various techniques to measure and characterize the surface roughness. They include that (1) surface roughness can be measured using a profilometer with sharp edge stylus, which is a contact method, (2) atomic force microscopy can provide non-contact surface topography from which the surface roughness can be indirectly measured, and (3) fractal dimension analysis can be used to present the surface roughness in non-Euclidian dimension [121,124]. Recently, Hansson et al. [139] employed computer simulations to measure surface roughness. The lateral resolution was defined as the pixel size of a profiling system. A surface roughness was simulated by a trigonometric function with random periodicity and amplitude. The function was divided into an array of pixels simulating the pixels of the profiling system. The mean height value for each pixel was used to calculate the surface roughness parameters. It was found that the accuracy of all the surface roughness parameters investigated decreased with increasing pixel size. This tendency was most pronounced for mean slope and developed length ratio, amounting to about 80% of their true values for a pixel size of 20% of the true mean high-spot spacing. It was concluded that the lateral resolution of an instrument/method severely compromises the precision of surface roughness parameters which are measured for roughness features with a mean high-spot spacing less than five times the lateral resolution [139]."}