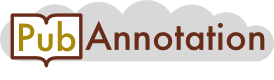
PMC:2871132 / 44699-55387
Annnotations
2_test
{"project":"2_test","denotations":[{"id":"20480036-8902237-52068669","span":{"begin":2316,"end":2319},"obj":"8902237"},{"id":"20480036-8902237-52068670","span":{"begin":2958,"end":2961},"obj":"8902237"},{"id":"20480036-15207462-52068671","span":{"begin":3135,"end":3138},"obj":"15207462"},{"id":"20480036-15207462-52068672","span":{"begin":3234,"end":3237},"obj":"15207462"},{"id":"20480036-15207462-52068673","span":{"begin":3343,"end":3346},"obj":"15207462"},{"id":"20480036-15207462-52068674","span":{"begin":3522,"end":3525},"obj":"15207462"},{"id":"20480036-15207462-52068675","span":{"begin":4439,"end":4442},"obj":"15207462"},{"id":"20480036-8940534-52068676","span":{"begin":5413,"end":5416},"obj":"8940534"},{"id":"20480036-8940534-52068677","span":{"begin":6377,"end":6380},"obj":"8940534"},{"id":"20480036-8962942-52068678","span":{"begin":8940,"end":8943},"obj":"8962942"},{"id":"20480036-9522688-52068679","span":{"begin":9927,"end":9930},"obj":"9522688"},{"id":"20480036-9522688-52068680","span":{"begin":10683,"end":10686},"obj":"9522688"},{"id":"T19896","span":{"begin":2316,"end":2319},"obj":"8902237"},{"id":"T16480","span":{"begin":2958,"end":2961},"obj":"8902237"},{"id":"T66209","span":{"begin":3135,"end":3138},"obj":"15207462"},{"id":"T6429","span":{"begin":3234,"end":3237},"obj":"15207462"},{"id":"T90139","span":{"begin":3343,"end":3346},"obj":"15207462"},{"id":"T11857","span":{"begin":3522,"end":3525},"obj":"15207462"},{"id":"T78796","span":{"begin":4439,"end":4442},"obj":"15207462"},{"id":"T86233","span":{"begin":5413,"end":5416},"obj":"8940534"},{"id":"T11241","span":{"begin":6377,"end":6380},"obj":"8940534"},{"id":"T7152","span":{"begin":8940,"end":8943},"obj":"8962942"},{"id":"T126","span":{"begin":9927,"end":9930},"obj":"9522688"},{"id":"T61525","span":{"begin":10683,"end":10686},"obj":"9522688"}],"text":"3.1. Sand-Blasting\nSand-blasting, as well as shot-peening (which will be discussed in the following section), has three purposes: (1) cleaning surface contaminants prior to further operation, (2) roughening surfaces to increase effective surface area (for example, under some circumstances, the effective surface area could be double than the original surface area), and (3) producing beneficial surface compressive residual stress [114]. As a result, such treated surfaces exhibit higher surface energy, indicating higher surface chemical and physical activities, and enhancing fatigue strength as well as fatigue life due to compressive residual stress [114].\nIn order to obtain satisfactory fixation and biofunctionality of biotolerated and bioinert materials, some of the mechanical surface alternation such as threaded surface, grooved surface, pored surface, and rough surface have been produced that promote tissue and bone ingrowth [115]. But so far, there is no report on suitable roughness to specific metallic biomaterials. In general, on the macroscopic level (\u003e10 μm), roughness will influence the mechanical properties of the interface, the way stresses are distributed and transmitted, the mechanical interlocking of the interface, and the biocompatibility of biomaterials. On a smaller scale, surface roughness in the range from 10 nm to 10 μm may influence the interface biology, since it is of the same order in size as cells and large biomolecules [48]. Topographic variations of the order of 10 nm and less may become important because microroughness on this scale length consists of material defects such as grain boundaries, dislocation steps, and vacancies, which are known to be active sites for adsorption, and thus may influence the bonding of biomolecules to the implant surface. There is evidence that surface roughness on a micron scale allows cellular adhesion that alters the overall tissue response to biomaterials [48]. Microrough surfaces allow early better adhesion of mineral ions or atoms, biomolecules, and cells, form stronger fixation of bone or connective tissue, result in a thinner tissue-reaction layer with inflammatory cells decreased or absent, and prevent microorganism adhesion and plaque accumulation, when compared with the smooth surfaces [48].\nPiattelli et al. [116] conducted a histological and histochemical evaluation in rabbits to study the presence of multinucleated giant cells (MGCs) at the interface with machined, sand-blasted (with 150 μm alumina media), and plasma-sprayed titanium implants. It was reported that (i) MGCs were not observed at any of the experimental times around machined and sand-blasted titanium surfaces; whereas (ii) MGCs were present at the interface with titanium plasma-sprayed implants at two weeks and two months, (iii) at four and eight weeks these cells tended to decrease in number, and (iv) an inflammatory infiltrate was not present in connection with the MGCs [116].\nAlthough alumina (Al2O3) or silica (SiO2) particles are most frequently used as a blasting media, there are several different types of powder particles utilized as media [113]. Surface roughness modulates the osseointegration of orthopedic and dental titanium implants [113]. This process may cause the release of cytotoxic silicium or aluminium ions in the peri-implant tissue [113]. To generate a biocompatible roughened titanium surface, an innovative grid-blasting process using biphasic calcium phosphate (BCP) particles was developed by Citeau et al. [113]. Ti-6Al-4V discs were either polished, BCP grid-blasted, or left as-machined. BCP grid-blasting created an average surface roughness of 1.57 μm compared to the original machined surface of 0.58 μm. X-ray photoelectron spectroscopy indicated traces of calcium and phosphorus and relatively less aluminum on the BCP grid-blasted surface than on the initial titanium specimen. It was reported that (i) scanning electronic microscopy observations and measurement of mitochondrial activity (MTS assay) showed that osteoblastic MC3T3-E1 cells were viable in contact with the BCP grid-blasted titanium surface, (ii) MC3T3-E1 cells expressed alkaline phosphate (ALP) activity and conserved their responsiveness to bone morphogenetic protein BMP-2, and (iii) the calcium phosphate grid-blasting technique increased the roughness of titanium implants and provided a non-cytotoxic surface with regard to mouse osteoblasts [113]. Tribo-chemical treatment has been proposed to enhance the bond strength between titanium crown and resin base [117]. Using silica-coated alumina as a blasting media under relatively low pressure, silica layer is expected to remain on the blasted surface so that retention force is enhanced by silan-coupling treatment.\nAlthough the recent development of investment materials and casting machines has enabled clinical applications of titanium in dentistry, there remain several problems to be solved. First of all, efficient finishing techniques are required. Titanium is known to be difficult to grind because of its plasticity, stickiness, low heat conductivity, and chemical reactivity at high temperatures [118,119]. Although blasting shows several advantages, there is evidence of adverse effects: (1) surface contamination, depending on type of blasting media, and (2) distortion of blasted workpiece, depending on blasting manner and intensity. Miyakawa et al. [120] studied the surface contamination of abraded titanium. Despite low grinding speeds and water cooling, the abraded surfaces were found to be contaminated by abrasive constituent elements. Element analysis and chemical bond state analysis of the contaminants were performed using an electron probe microanalyzer. X-ray diffraction of the abraded surface was performed to identify the contaminants. It was reported that (i) the contamination of titanium is related to its reactivity as well as its hardness, (ii) in spite of water cooling and slow-speed abrading, titanium surfaces were obviously contaminated, (iii) contaminant deposits with dimensions ranging from about 10 to 30 μm occurred throughout the surfaces, and (iv) the contaminant of titanium, although related to the hardness, resulted primarily from a reaction with abrasive materials, and such contamination could negatively influence titanium’s resistance to corrosion and its biocompatibility [120].\nNormally, fine alumina particles (50 μm Al2O3) are recycled within the sand-blasting machine. Ceramics such as alumina are brittle in nature, therefore some portions of recycled alumina might be brittle-fractured. If fractured sand blasting particles are involved in the recycling media, it might result in irregular surfaces, as well as potential contamination. Using fractal dimension analysis [121–123], a sample plate surface was weekly analyzed in terms of topographic changes, as well as chemical analysis of sampled recycled Al2O3 particles. It was found that after accumulated use time exceeded 30 mins, the fractal dimension (DF) remained a constant value of about 1.4, prior to that it continuously increased from 1.25 to 1.4. By the electron probe microanalysis on collected blasting particles, unused Al2O3 contains 100% Al, whereas used (accumulated usage time was about 2,400 sec) particles contained Al (83.32 wt%), Ti (5.48), Ca (1.68), Ni (1.36), Mo (1.31), S (1.02), Si (0.65), P (0.55), Mn (0.49), K (0.29), Cl (0.26), and V (0.08), strongly indicating that used alumina powder was heavily contaminated, and a high risk for the next material surface to be contaminated. Such contaminants are from previously blasted materials having various chemical compositions, and investing materials as well [124].\nThere is evidence of surface contamination due to mechanical abrasive actions [125]. As a metallographic preparation, the surface needs to be mechanically polished with a metallographic paper (which is normally SiC-adhered paper) under running water [125]. It is worth mentioning here that polishing paper should be changed between different types of materials, and particularly when a dissimilar metal-couple is used for galvanic corrosion tests, such couple should not be polished prior to corrosion testing because both materials could become cross-contaminated. Hence, there are attempts to use TiO2 powder for blasting onto titanium material surfaces. It was reported that titanium surfaces were sand-blasted using TiO2 powder (particle size ranging from 45 μm, 45 μm-63 μm, and 63 μm-90 μm) to produce the different surface textures prior to fibroblast cell attachment [126].\nIn the rabbit tibia, CpTi implants, which were sand-blasted with 25 μm Al2O3 and TiO2 particles, were inserted in the rabbit tibia for 12 weeks [127]. Even though the amount of Al on the implant surface was higher than for the Al2O3-blasted implants compared to implants not blasted with Al2O3, any negative effects of the Al element were not detected [128], which is in contrast to those reported by Johansson et al. [127], who reported that Al release from Ti-6Al-4V implants was found to coincide with a poorer bone-to-implant over a three month period. It is possible that the lack of differences between TiO2-blasted and the Al2O3-blasted implants depends on lower surface concentrations of toxic Al ions than those reported by Johansson et al. [127]. Wang [129] investigated the effects of various surface modifications on porcelain bond strengths. Such modifications included Al2O3 blasting, TiO2 blasting, HNO3 + HF + H2O treatment, H2O2 treatment, and pre-oxidation in air at 600 °C for 10 min. Ti-porcelain couples were subjected to 3-point bending tests. It was concluded that TiO2 air abrasion showed the highest bond strength, which was significantly different from other surface treatments.\nRecently, it was reported that sand-blasting using alumina particle caused a remarkable distortion on a Co-Cr alloy and a noble alloy [130,131]. It was estimated that the stress causing the deflection exceeded the yield strength of tested materials. It was also suggested that the sand-blasting should be done using the lowest air pressure, duration of blasting period, and particle size alumina in order to minimize distortion of crowns and frameworks. To measure distortion, Co-Cr alloy plates (25 mm long, 5 mm wide, 0.7 mm thick) were sand-blasted with Al2O3 of 125 μm. Distortion was determined as the deflection of the plates as a distance of 20mm from the surface. It was reported that (i) the mean deflections varied between 0.37 mm and 1.72 mm, and (ii) deflection increased by an increase in duration of the blasting, pressure, particle size, and by a decrease in plate thickness [130]."}
NEUROSES
{"project":"NEUROSES","denotations":[{"id":"T884","span":{"begin":247,"end":251},"obj":"PATO_0001323"},{"id":"T885","span":{"begin":314,"end":318},"obj":"PATO_0001323"},{"id":"T886","span":{"begin":361,"end":365},"obj":"PATO_0001323"},{"id":"T887","span":{"begin":498,"end":504},"obj":"PATO_0001021"},{"id":"T888","span":{"begin":588,"end":596},"obj":"PATO_0001230"},{"id":"T889","span":{"begin":796,"end":807},"obj":"PATO_0000999"},{"id":"T890","span":{"begin":834,"end":841},"obj":"PATO_0002255"},{"id":"T891","span":{"begin":870,"end":875},"obj":"PATO_0000700"},{"id":"T892","span":{"begin":1173,"end":1184},"obj":"PATO_0001566"},{"id":"T893","span":{"begin":1431,"end":1435},"obj":"PATO_0000117"},{"id":"T894","span":{"begin":1449,"end":1454},"obj":"PATO_0000586"},{"id":"T895","span":{"begin":1586,"end":1592},"obj":"PATO_0000122"},{"id":"T896","span":{"begin":1648,"end":1659},"obj":"PATO_0001852"},{"id":"T897","span":{"begin":1704,"end":1710},"obj":"PATO_0002354"},{"id":"T898","span":{"begin":1980,"end":1985},"obj":"PATO_0000694"},{"id":"T899","span":{"begin":2005,"end":2012},"obj":"CHEBI_46662"},{"id":"T900","span":{"begin":2013,"end":2017},"obj":"CHEBI_24870"},{"id":"T901","span":{"begin":2021,"end":2026},"obj":"CHEBI_33250"},{"id":"T902","span":{"begin":2153,"end":2165},"obj":"PATO_0002104"},{"id":"T903","span":{"begin":2889,"end":2901},"obj":"PATO_0002104"},{"id":"T904","span":{"begin":2172,"end":2181},"obj":"PATO_0001997"},{"id":"T905","span":{"begin":2185,"end":2191},"obj":"PATO_0000462"},{"id":"T906","span":{"begin":2239,"end":2251},"obj":"PATO_0002269"},{"id":"T907","span":{"begin":2276,"end":2282},"obj":"PATO_0000701"},{"id":"T908","span":{"begin":2399,"end":2407},"obj":"PATO_0000070"},{"id":"T909","span":{"begin":2869,"end":2875},"obj":"PATO_0000070"},{"id":"T910","span":{"begin":2426,"end":2431},"obj":"PATO_0001940"},{"id":"T911","span":{"begin":2503,"end":2510},"obj":"CHEBI_30187"},{"id":"T912","span":{"begin":2973,"end":2980},"obj":"CHEBI_30187"},{"id":"T913","span":{"begin":2982,"end":2987},"obj":"CHEBI_30187"},{"id":"T914","span":{"begin":2538,"end":2546},"obj":"CHEBI_33341"},{"id":"T915","span":{"begin":2671,"end":2679},"obj":"CHEBI_33341"},{"id":"T916","span":{"begin":2743,"end":2751},"obj":"CHEBI_33341"},{"id":"T917","span":{"begin":2713,"end":2720},"obj":"PATO_0000467"},{"id":"T918","span":{"begin":2921,"end":2928},"obj":"PATO_0000467"},{"id":"T919","span":{"begin":2869,"end":2875},"obj":"PATO_0001056"},{"id":"T920","span":{"begin":2869,"end":2875},"obj":"PATO_0001555"},{"id":"T921","span":{"begin":2982,"end":2987},"obj":"CHEBI_30192"},{"id":"T922","span":{"begin":2982,"end":2987},"obj":"CHEBI_30191"},{"id":"T923","span":{"begin":2992,"end":2998},"obj":"CHEBI_30563"},{"id":"T924","span":{"begin":3000,"end":3004},"obj":"CHEBI_30563"},{"id":"T925","span":{"begin":3215,"end":3223},"obj":"CHEBI_33341"},{"id":"T926","span":{"begin":3387,"end":3395},"obj":"CHEBI_33341"},{"id":"T927","span":{"begin":3882,"end":3890},"obj":"CHEBI_33341"},{"id":"T928","span":{"begin":4113,"end":4121},"obj":"CHEBI_33341"},{"id":"T929","span":{"begin":4350,"end":4358},"obj":"CHEBI_33341"},{"id":"T930","span":{"begin":3245,"end":3252},"obj":"PATO_0000006"},{"id":"T931","span":{"begin":3433,"end":3440},"obj":"PATO_0000006"},{"id":"T932","span":{"begin":3288,"end":3296},"obj":"CHEBI_27573"},{"id":"T933","span":{"begin":3300,"end":3309},"obj":"CHEBI_28984"},{"id":"T934","span":{"begin":3821,"end":3829},"obj":"CHEBI_28984"},{"id":"T935","span":{"begin":3310,"end":3314},"obj":"CHEBI_24870"},{"id":"T936","span":{"begin":3000,"end":3004},"obj":"CHEBI_30563"},{"id":"T937","span":{"begin":3215,"end":3223},"obj":"CHEBI_33341"},{"id":"T938","span":{"begin":3387,"end":3395},"obj":"CHEBI_33341"},{"id":"T939","span":{"begin":3882,"end":3890},"obj":"CHEBI_33341"},{"id":"T940","span":{"begin":4113,"end":4121},"obj":"CHEBI_33341"},{"id":"T941","span":{"begin":4350,"end":4358},"obj":"CHEBI_33341"},{"id":"T942","span":{"begin":3245,"end":3252},"obj":"PATO_0000006"},{"id":"T943","span":{"begin":3433,"end":3440},"obj":"PATO_0000006"},{"id":"T944","span":{"begin":3288,"end":3296},"obj":"CHEBI_27573"},{"id":"T945","span":{"begin":3300,"end":3309},"obj":"CHEBI_28984"},{"id":"T946","span":{"begin":3821,"end":3829},"obj":"CHEBI_28984"},{"id":"T947","span":{"begin":3310,"end":3314},"obj":"CHEBI_24870"},{"id":"T948","span":{"begin":3000,"end":3004},"obj":"CHEBI_30563"},{"id":"T949","span":{"begin":3215,"end":3223},"obj":"CHEBI_33341"},{"id":"T950","span":{"begin":3387,"end":3395},"obj":"CHEBI_33341"},{"id":"T951","span":{"begin":3882,"end":3890},"obj":"CHEBI_33341"},{"id":"T952","span":{"begin":4113,"end":4121},"obj":"CHEBI_33341"},{"id":"T953","span":{"begin":4350,"end":4358},"obj":"CHEBI_33341"},{"id":"T954","span":{"begin":3245,"end":3252},"obj":"PATO_0000006"},{"id":"T955","span":{"begin":3433,"end":3440},"obj":"PATO_0000006"},{"id":"T956","span":{"begin":3288,"end":3296},"obj":"CHEBI_27573"},{"id":"T957","span":{"begin":3300,"end":3309},"obj":"CHEBI_28984"},{"id":"T958","span":{"begin":3821,"end":3829},"obj":"CHEBI_28984"},{"id":"T959","span":{"begin":3310,"end":3314},"obj":"CHEBI_24870"},{"id":"T960","span":{"begin":3000,"end":3004},"obj":"CHEBI_30563"},{"id":"T961","span":{"begin":3215,"end":3223},"obj":"CHEBI_33341"},{"id":"T962","span":{"begin":3387,"end":3395},"obj":"CHEBI_33341"},{"id":"T963","span":{"begin":3882,"end":3890},"obj":"CHEBI_33341"},{"id":"T964","span":{"begin":4113,"end":4121},"obj":"CHEBI_33341"},{"id":"T965","span":{"begin":4350,"end":4358},"obj":"CHEBI_33341"},{"id":"T966","span":{"begin":3245,"end":3252},"obj":"PATO_0000006"},{"id":"T967","span":{"begin":3433,"end":3440},"obj":"PATO_0000006"},{"id":"T968","span":{"begin":3288,"end":3296},"obj":"CHEBI_27573"},{"id":"T969","span":{"begin":3300,"end":3309},"obj":"CHEBI_28984"},{"id":"T970","span":{"begin":3821,"end":3829},"obj":"CHEBI_28984"},{"id":"T971","span":{"begin":3310,"end":3314},"obj":"CHEBI_24870"},{"id":"T972","span":{"begin":3000,"end":3004},"obj":"CHEBI_30563"},{"id":"T973","span":{"begin":3215,"end":3223},"obj":"CHEBI_33341"},{"id":"T974","span":{"begin":3387,"end":3395},"obj":"CHEBI_33341"},{"id":"T975","span":{"begin":3882,"end":3890},"obj":"CHEBI_33341"},{"id":"T976","span":{"begin":4113,"end":4121},"obj":"CHEBI_33341"},{"id":"T977","span":{"begin":4350,"end":4358},"obj":"CHEBI_33341"},{"id":"T978","span":{"begin":3245,"end":3252},"obj":"PATO_0000006"},{"id":"T979","span":{"begin":3433,"end":3440},"obj":"PATO_0000006"},{"id":"T980","span":{"begin":3288,"end":3296},"obj":"CHEBI_27573"},{"id":"T981","span":{"begin":3300,"end":3309},"obj":"CHEBI_28984"},{"id":"T982","span":{"begin":3821,"end":3829},"obj":"CHEBI_28984"},{"id":"T983","span":{"begin":3310,"end":3314},"obj":"CHEBI_24870"},{"id":"T984","span":{"begin":3000,"end":3004},"obj":"CHEBI_30563"},{"id":"T985","span":{"begin":3215,"end":3223},"obj":"CHEBI_33341"},{"id":"T986","span":{"begin":3387,"end":3395},"obj":"CHEBI_33341"},{"id":"T987","span":{"begin":3882,"end":3890},"obj":"CHEBI_33341"},{"id":"T988","span":{"begin":4113,"end":4121},"obj":"CHEBI_33341"},{"id":"T989","span":{"begin":4350,"end":4358},"obj":"CHEBI_33341"},{"id":"T990","span":{"begin":3245,"end":3252},"obj":"PATO_0000006"},{"id":"T991","span":{"begin":3433,"end":3440},"obj":"PATO_0000006"},{"id":"T992","span":{"begin":3288,"end":3296},"obj":"CHEBI_27573"},{"id":"T993","span":{"begin":3300,"end":3309},"obj":"CHEBI_28984"},{"id":"T994","span":{"begin":3821,"end":3829},"obj":"CHEBI_28984"},{"id":"T995","span":{"begin":3310,"end":3314},"obj":"CHEBI_24870"},{"id":"T996","span":{"begin":3000,"end":3004},"obj":"CHEBI_30563"},{"id":"T997","span":{"begin":3215,"end":3223},"obj":"CHEBI_33341"},{"id":"T998","span":{"begin":3387,"end":3395},"obj":"CHEBI_33341"},{"id":"T999","span":{"begin":3882,"end":3890},"obj":"CHEBI_33341"},{"id":"T1000","span":{"begin":4113,"end":4121},"obj":"CHEBI_33341"},{"id":"T1001","span":{"begin":4350,"end":4358},"obj":"CHEBI_33341"},{"id":"T1002","span":{"begin":3245,"end":3252},"obj":"PATO_0000006"},{"id":"T1003","span":{"begin":3433,"end":3440},"obj":"PATO_0000006"},{"id":"T1004","span":{"begin":3288,"end":3296},"obj":"CHEBI_27573"},{"id":"T1005","span":{"begin":3300,"end":3309},"obj":"CHEBI_28984"},{"id":"T1006","span":{"begin":3821,"end":3829},"obj":"CHEBI_28984"},{"id":"T1007","span":{"begin":3310,"end":3314},"obj":"CHEBI_24870"},{"id":"T1008","span":{"begin":3000,"end":3004},"obj":"CHEBI_30563"},{"id":"T1009","span":{"begin":3215,"end":3223},"obj":"CHEBI_33341"},{"id":"T1010","span":{"begin":3387,"end":3395},"obj":"CHEBI_33341"},{"id":"T1011","span":{"begin":3882,"end":3890},"obj":"CHEBI_33341"},{"id":"T1012","span":{"begin":4113,"end":4121},"obj":"CHEBI_33341"},{"id":"T1013","span":{"begin":4350,"end":4358},"obj":"CHEBI_33341"},{"id":"T1014","span":{"begin":3245,"end":3252},"obj":"PATO_0000006"},{"id":"T1015","span":{"begin":3433,"end":3440},"obj":"PATO_0000006"},{"id":"T1016","span":{"begin":3288,"end":3296},"obj":"CHEBI_27573"},{"id":"T1017","span":{"begin":3300,"end":3309},"obj":"CHEBI_28984"},{"id":"T1018","span":{"begin":3821,"end":3829},"obj":"CHEBI_28984"},{"id":"T1019","span":{"begin":3310,"end":3314},"obj":"CHEBI_24870"},{"id":"T1020","span":{"begin":3000,"end":3004},"obj":"CHEBI_30563"},{"id":"T1021","span":{"begin":3215,"end":3223},"obj":"CHEBI_33341"},{"id":"T1022","span":{"begin":3387,"end":3395},"obj":"CHEBI_33341"},{"id":"T1023","span":{"begin":3882,"end":3890},"obj":"CHEBI_33341"},{"id":"T1024","span":{"begin":4113,"end":4121},"obj":"CHEBI_33341"},{"id":"T1025","span":{"begin":4350,"end":4358},"obj":"CHEBI_33341"},{"id":"T1026","span":{"begin":3245,"end":3252},"obj":"PATO_0000006"},{"id":"T1027","span":{"begin":3433,"end":3440},"obj":"PATO_0000006"},{"id":"T1028","span":{"begin":3288,"end":3296},"obj":"CHEBI_27573"},{"id":"T1029","span":{"begin":3300,"end":3309},"obj":"CHEBI_28984"},{"id":"T1030","span":{"begin":3821,"end":3829},"obj":"CHEBI_28984"},{"id":"T1031","span":{"begin":3310,"end":3314},"obj":"CHEBI_24870"},{"id":"T1032","span":{"begin":3000,"end":3004},"obj":"CHEBI_30563"},{"id":"T1033","span":{"begin":3215,"end":3223},"obj":"CHEBI_33341"},{"id":"T1034","span":{"begin":3387,"end":3395},"obj":"CHEBI_33341"},{"id":"T1035","span":{"begin":3882,"end":3890},"obj":"CHEBI_33341"},{"id":"T1036","span":{"begin":4113,"end":4121},"obj":"CHEBI_33341"},{"id":"T1037","span":{"begin":4350,"end":4358},"obj":"CHEBI_33341"},{"id":"T1038","span":{"begin":3245,"end":3252},"obj":"PATO_0000006"},{"id":"T1039","span":{"begin":3433,"end":3440},"obj":"PATO_0000006"},{"id":"T1040","span":{"begin":3288,"end":3296},"obj":"CHEBI_27573"},{"id":"T1041","span":{"begin":3300,"end":3309},"obj":"CHEBI_28984"},{"id":"T1042","span":{"begin":3821,"end":3829},"obj":"CHEBI_28984"},{"id":"T1043","span":{"begin":3310,"end":3314},"obj":"CHEBI_24870"},{"id":"T1044","span":{"begin":3000,"end":3004},"obj":"CHEBI_30563"},{"id":"T1045","span":{"begin":3215,"end":3223},"obj":"CHEBI_33341"},{"id":"T1046","span":{"begin":3387,"end":3395},"obj":"CHEBI_33341"},{"id":"T1047","span":{"begin":3882,"end":3890},"obj":"CHEBI_33341"},{"id":"T1048","span":{"begin":4113,"end":4121},"obj":"CHEBI_33341"},{"id":"T1049","span":{"begin":4350,"end":4358},"obj":"CHEBI_33341"},{"id":"T1050","span":{"begin":3245,"end":3252},"obj":"PATO_0000006"},{"id":"T1051","span":{"begin":3433,"end":3440},"obj":"PATO_0000006"},{"id":"T1052","span":{"begin":3288,"end":3296},"obj":"CHEBI_27573"},{"id":"T1053","span":{"begin":3300,"end":3309},"obj":"CHEBI_28984"},{"id":"T1054","span":{"begin":3821,"end":3829},"obj":"CHEBI_28984"},{"id":"T1055","span":{"begin":3310,"end":3314},"obj":"CHEBI_24870"},{"id":"T1056","span":{"begin":4508,"end":4516},"obj":"PATO_0001230"},{"id":"T1057","span":{"begin":4525,"end":4533},"obj":"CHEBI_33341"},{"id":"T1058","span":{"begin":4878,"end":4886},"obj":"CHEBI_33341"},{"id":"T1059","span":{"begin":5004,"end":5012},"obj":"CHEBI_33341"},{"id":"T1060","span":{"begin":5463,"end":5471},"obj":"CHEBI_33341"},{"id":"T1061","span":{"begin":5979,"end":5987},"obj":"CHEBI_33341"},{"id":"T1062","span":{"begin":4534,"end":4539},"obj":"CHEBI_37409"},{"id":"T1063","span":{"begin":4550,"end":4554},"obj":"CHEBI_22695"},{"id":"T1064","span":{"begin":4550,"end":4554},"obj":"CHEBI_18282"},{"id":"T1065","span":{"begin":4568,"end":4574},"obj":"CHEBI_30563"},{"id":"T1066","span":{"begin":4641,"end":4647},"obj":"CHEBI_30563"},{"id":"T1067","span":{"begin":4582,"end":4589},"obj":"CHEBI_30187"},{"id":"T1068","span":{"begin":4717,"end":4722},"obj":"PATO_0001035"},{"id":"T1069","span":{"begin":4726,"end":4734},"obj":"PATO_0001589"},{"id":"T1070","span":{"begin":4777,"end":4783},"obj":"PATO_0001484"},{"id":"T1071","span":{"begin":5074,"end":5084},"obj":"PATO_0001431"},{"id":"T1072","span":{"begin":5086,"end":5089},"obj":"PATO_0000471"},{"id":"T1073","span":{"begin":5481,"end":5484},"obj":"PATO_0000471"},{"id":"T1074","span":{"begin":5136,"end":5140},"obj":"PATO_0000469"},{"id":"T1075","span":{"begin":5385,"end":5394},"obj":"PATO_0000049"},{"id":"T1076","span":{"begin":5505,"end":5510},"obj":"CHEBI_46629"},{"id":"T1077","span":{"begin":5505,"end":5510},"obj":"CHEBI_15377"},{"id":"T1078","span":{"begin":5595,"end":5603},"obj":"CHEBI_33250"},{"id":"T1079","span":{"begin":5605,"end":5612},"obj":"CHEBI_33250"},{"id":"T1080","span":{"begin":5699,"end":5707},"obj":"CHEBI_10545"},{"id":"T1081","span":{"begin":5708,"end":5713},"obj":"CHEBI_50406"},{"id":"T1082","span":{"begin":5913,"end":5921},"obj":"PATO_0000048"},{"id":"T1083","span":{"begin":5958,"end":5962},"obj":"PATO_0000304"},{"id":"T1084","span":{"begin":5963,"end":5968},"obj":"PATO_0000008"},{"id":"T1085","span":{"begin":6162,"end":6170},"obj":"CHEBI_33341"},{"id":"T1086","span":{"begin":6196,"end":6204},"obj":"PATO_0000048"},{"id":"T1087","span":{"begin":6398,"end":6405},"obj":"CHEBI_30187"},{"id":"T1088","span":{"begin":6423,"end":6428},"obj":"CHEBI_30187"},{"id":"T1089","span":{"begin":6494,"end":6501},"obj":"CHEBI_30187"},{"id":"T1090","span":{"begin":6561,"end":6568},"obj":"CHEBI_30187"},{"id":"T1091","span":{"begin":6915,"end":6920},"obj":"CHEBI_30187"},{"id":"T1092","span":{"begin":7196,"end":7201},"obj":"CHEBI_30187"},{"id":"T1093","span":{"begin":7465,"end":7472},"obj":"CHEBI_30187"},{"id":"T1094","span":{"begin":6423,"end":6428},"obj":"CHEBI_30192"},{"id":"T1095","span":{"begin":6915,"end":6920},"obj":"CHEBI_30192"},{"id":"T1096","span":{"begin":7196,"end":7201},"obj":"CHEBI_30192"},{"id":"T1097","span":{"begin":6423,"end":6428},"obj":"CHEBI_30191"},{"id":"T1098","span":{"begin":6915,"end":6920},"obj":"CHEBI_30191"},{"id":"T1099","span":{"begin":7196,"end":7201},"obj":"CHEBI_30191"},{"id":"T1100","span":{"begin":6506,"end":6513},"obj":"PATO_0002477"},{"id":"T1101","span":{"begin":6578,"end":6585},"obj":"PATO_0002477"},{"id":"T1102","span":{"begin":6586,"end":6595},"obj":"PATO_0001444"},{"id":"T1103","span":{"begin":6600,"end":6609},"obj":"PATO_0001444"},{"id":"T1104","span":{"begin":6956,"end":6967},"obj":"PATO_0002270"},{"id":"T1105","span":{"begin":7234,"end":7245},"obj":"PATO_0002270"},{"id":"T1106","span":{"begin":6972,"end":6976},"obj":"PATO_0001309"},{"id":"T1107","span":{"begin":7252,"end":7256},"obj":"PATO_0001309"},{"id":"T1108","span":{"begin":6972,"end":6976},"obj":"PATO_0000165"},{"id":"T1109","span":{"begin":7252,"end":7256},"obj":"PATO_0000165"},{"id":"T1110","span":{"begin":7033,"end":7041},"obj":"PATO_0000438"},{"id":"T1111","span":{"begin":7042,"end":7047},"obj":"PATO_0000002"},{"id":"T1112","span":{"begin":7092,"end":7101},"obj":"PATO_0000470"},{"id":"T1113","span":{"begin":7127,"end":7135},"obj":"CHEBI_10545"},{"id":"T1114","span":{"begin":7136,"end":7141},"obj":"CHEBI_50406"},{"id":"T1115","span":{"begin":7273,"end":7276},"obj":"CHEBI_30000"},{"id":"T1116","span":{"begin":7512,"end":7516},"obj":"PATO_0000469"},{"id":"T1117","span":{"begin":7916,"end":7919},"obj":"CHEBI_29390"},{"id":"T1118","span":{"begin":7949,"end":7954},"obj":"CHEBI_46629"},{"id":"T1119","span":{"begin":7949,"end":7954},"obj":"CHEBI_15377"},{"id":"T1120","span":{"begin":8102,"end":8107},"obj":"CHEBI_33521"},{"id":"T1121","span":{"begin":8304,"end":8308},"obj":"CHEBI_32234"},{"id":"T1122","span":{"begin":8425,"end":8429},"obj":"CHEBI_32234"},{"id":"T1123","span":{"begin":8668,"end":8672},"obj":"CHEBI_32234"},{"id":"T1124","span":{"begin":8334,"end":8342},"obj":"CHEBI_33341"},{"id":"T1125","span":{"begin":8383,"end":8391},"obj":"CHEBI_33341"},{"id":"T1126","span":{"begin":8447,"end":8451},"obj":"PATO_0000117"},{"id":"T1127","span":{"begin":8658,"end":8663},"obj":"CHEBI_30192"},{"id":"T1128","span":{"begin":8814,"end":8819},"obj":"CHEBI_30192"},{"id":"T1129","span":{"begin":8875,"end":8880},"obj":"CHEBI_30192"},{"id":"T1130","span":{"begin":8658,"end":8663},"obj":"CHEBI_30191"},{"id":"T1131","span":{"begin":8814,"end":8819},"obj":"CHEBI_30191"},{"id":"T1132","span":{"begin":8875,"end":8880},"obj":"CHEBI_30191"},{"id":"T1133","span":{"begin":8658,"end":8663},"obj":"CHEBI_30187"},{"id":"T1134","span":{"begin":8814,"end":8819},"obj":"CHEBI_30187"},{"id":"T1135","span":{"begin":8875,"end":8880},"obj":"CHEBI_30187"},{"id":"T1136","span":{"begin":8689,"end":8697},"obj":"PATO_0000624"},{"id":"T1137","span":{"begin":8913,"end":8920},"obj":"CHEBI_33250"},{"id":"T1138","span":{"begin":9136,"end":9142},"obj":"PATO_0001309"},{"id":"T1139","span":{"begin":10133,"end":10141},"obj":"PATO_0001309"},{"id":"T1140","span":{"begin":10154,"end":10160},"obj":"PATO_0001309"},{"id":"T1141","span":{"begin":9196,"end":9200},"obj":"CHEBI_32234"},{"id":"T1142","span":{"begin":9486,"end":9490},"obj":"CHEBI_32234"},{"id":"T1143","span":{"begin":9675,"end":9679},"obj":"CHEBI_32234"},{"id":"T1144","span":{"begin":9217,"end":9222},"obj":"CHEBI_30192"},{"id":"T1145","span":{"begin":9470,"end":9475},"obj":"CHEBI_30192"},{"id":"T1146","span":{"begin":10349,"end":10354},"obj":"CHEBI_30192"},{"id":"T1147","span":{"begin":9217,"end":9222},"obj":"CHEBI_30187"},{"id":"T1148","span":{"begin":9470,"end":9475},"obj":"CHEBI_30187"},{"id":"T1149","span":{"begin":9843,"end":9850},"obj":"CHEBI_30187"},{"id":"T1150","span":{"begin":10180,"end":10187},"obj":"CHEBI_30187"},{"id":"T1151","span":{"begin":10349,"end":10354},"obj":"CHEBI_30187"},{"id":"T1152","span":{"begin":9217,"end":9222},"obj":"CHEBI_30191"},{"id":"T1153","span":{"begin":9470,"end":9475},"obj":"CHEBI_30191"},{"id":"T1154","span":{"begin":10349,"end":10354},"obj":"CHEBI_30191"},{"id":"T1155","span":{"begin":9292,"end":9296},"obj":"CHEBI_24870"},{"id":"T1156","span":{"begin":9501,"end":9505},"obj":"CHEBI_48107"},{"id":"T1157","span":{"begin":9501,"end":9505},"obj":"CHEBI_25942"},{"id":"T1158","span":{"begin":9513,"end":9516},"obj":"CHEBI_33813"},{"id":"T1159","span":{"begin":9513,"end":9516},"obj":"CHEBI_15377"},{"id":"T1160","span":{"begin":9513,"end":9516},"obj":"CHEBI_29375"},{"id":"T1161","span":{"begin":9528,"end":9532},"obj":"CHEBI_30492"},{"id":"T1162","span":{"begin":9528,"end":9532},"obj":"CHEBI_16240"},{"id":"T1163","span":{"begin":9565,"end":9568},"obj":"CHEBI_28843"},{"id":"T1164","span":{"begin":9680,"end":9683},"obj":"CHEBI_28843"},{"id":"T1165","span":{"begin":10119,"end":10122},"obj":"CHEBI_28843"},{"id":"T1166","span":{"begin":9717,"end":9725},"obj":"PATO_0001230"},{"id":"T1167","span":{"begin":10012,"end":10020},"obj":"PATO_0001230"},{"id":"T1168","span":{"begin":10006,"end":10011},"obj":"PATO_0000170"},{"id":"T1169","span":{"begin":10123,"end":10131},"obj":"PATO_0001025"},{"id":"T1170","span":{"begin":10175,"end":10179},"obj":"PATO_0000117"},{"id":"T1171","span":{"begin":10295,"end":10299},"obj":"PATO_0000573"},{"id":"T1172","span":{"begin":10306,"end":10310},"obj":"PATO_0000600"},{"id":"T1173","span":{"begin":10429,"end":10437},"obj":"PATO_0000040"},{"id":"T1174","span":{"begin":10566,"end":10575},"obj":"PATO_0000470"},{"id":"T1175","span":{"begin":10594,"end":10602},"obj":"PATO_0001309"},{"id":"T1176","span":{"begin":10620,"end":10628},"obj":"PATO_0001025"},{"id":"T1177","span":{"begin":10639,"end":10643},"obj":"PATO_0000117"},{"id":"T1178","span":{"begin":10672,"end":10681},"obj":"PATO_0000915"}],"text":"3.1. Sand-Blasting\nSand-blasting, as well as shot-peening (which will be discussed in the following section), has three purposes: (1) cleaning surface contaminants prior to further operation, (2) roughening surfaces to increase effective surface area (for example, under some circumstances, the effective surface area could be double than the original surface area), and (3) producing beneficial surface compressive residual stress [114]. As a result, such treated surfaces exhibit higher surface energy, indicating higher surface chemical and physical activities, and enhancing fatigue strength as well as fatigue life due to compressive residual stress [114].\nIn order to obtain satisfactory fixation and biofunctionality of biotolerated and bioinert materials, some of the mechanical surface alternation such as threaded surface, grooved surface, pored surface, and rough surface have been produced that promote tissue and bone ingrowth [115]. But so far, there is no report on suitable roughness to specific metallic biomaterials. In general, on the macroscopic level (\u003e10 μm), roughness will influence the mechanical properties of the interface, the way stresses are distributed and transmitted, the mechanical interlocking of the interface, and the biocompatibility of biomaterials. On a smaller scale, surface roughness in the range from 10 nm to 10 μm may influence the interface biology, since it is of the same order in size as cells and large biomolecules [48]. Topographic variations of the order of 10 nm and less may become important because microroughness on this scale length consists of material defects such as grain boundaries, dislocation steps, and vacancies, which are known to be active sites for adsorption, and thus may influence the bonding of biomolecules to the implant surface. There is evidence that surface roughness on a micron scale allows cellular adhesion that alters the overall tissue response to biomaterials [48]. Microrough surfaces allow early better adhesion of mineral ions or atoms, biomolecules, and cells, form stronger fixation of bone or connective tissue, result in a thinner tissue-reaction layer with inflammatory cells decreased or absent, and prevent microorganism adhesion and plaque accumulation, when compared with the smooth surfaces [48].\nPiattelli et al. [116] conducted a histological and histochemical evaluation in rabbits to study the presence of multinucleated giant cells (MGCs) at the interface with machined, sand-blasted (with 150 μm alumina media), and plasma-sprayed titanium implants. It was reported that (i) MGCs were not observed at any of the experimental times around machined and sand-blasted titanium surfaces; whereas (ii) MGCs were present at the interface with titanium plasma-sprayed implants at two weeks and two months, (iii) at four and eight weeks these cells tended to decrease in number, and (iv) an inflammatory infiltrate was not present in connection with the MGCs [116].\nAlthough alumina (Al2O3) or silica (SiO2) particles are most frequently used as a blasting media, there are several different types of powder particles utilized as media [113]. Surface roughness modulates the osseointegration of orthopedic and dental titanium implants [113]. This process may cause the release of cytotoxic silicium or aluminium ions in the peri-implant tissue [113]. To generate a biocompatible roughened titanium surface, an innovative grid-blasting process using biphasic calcium phosphate (BCP) particles was developed by Citeau et al. [113]. Ti-6Al-4V discs were either polished, BCP grid-blasted, or left as-machined. BCP grid-blasting created an average surface roughness of 1.57 μm compared to the original machined surface of 0.58 μm. X-ray photoelectron spectroscopy indicated traces of calcium and phosphorus and relatively less aluminum on the BCP grid-blasted surface than on the initial titanium specimen. It was reported that (i) scanning electronic microscopy observations and measurement of mitochondrial activity (MTS assay) showed that osteoblastic MC3T3-E1 cells were viable in contact with the BCP grid-blasted titanium surface, (ii) MC3T3-E1 cells expressed alkaline phosphate (ALP) activity and conserved their responsiveness to bone morphogenetic protein BMP-2, and (iii) the calcium phosphate grid-blasting technique increased the roughness of titanium implants and provided a non-cytotoxic surface with regard to mouse osteoblasts [113]. Tribo-chemical treatment has been proposed to enhance the bond strength between titanium crown and resin base [117]. Using silica-coated alumina as a blasting media under relatively low pressure, silica layer is expected to remain on the blasted surface so that retention force is enhanced by silan-coupling treatment.\nAlthough the recent development of investment materials and casting machines has enabled clinical applications of titanium in dentistry, there remain several problems to be solved. First of all, efficient finishing techniques are required. Titanium is known to be difficult to grind because of its plasticity, stickiness, low heat conductivity, and chemical reactivity at high temperatures [118,119]. Although blasting shows several advantages, there is evidence of adverse effects: (1) surface contamination, depending on type of blasting media, and (2) distortion of blasted workpiece, depending on blasting manner and intensity. Miyakawa et al. [120] studied the surface contamination of abraded titanium. Despite low grinding speeds and water cooling, the abraded surfaces were found to be contaminated by abrasive constituent elements. Element analysis and chemical bond state analysis of the contaminants were performed using an electron probe microanalyzer. X-ray diffraction of the abraded surface was performed to identify the contaminants. It was reported that (i) the contamination of titanium is related to its reactivity as well as its hardness, (ii) in spite of water cooling and slow-speed abrading, titanium surfaces were obviously contaminated, (iii) contaminant deposits with dimensions ranging from about 10 to 30 μm occurred throughout the surfaces, and (iv) the contaminant of titanium, although related to the hardness, resulted primarily from a reaction with abrasive materials, and such contamination could negatively influence titanium’s resistance to corrosion and its biocompatibility [120].\nNormally, fine alumina particles (50 μm Al2O3) are recycled within the sand-blasting machine. Ceramics such as alumina are brittle in nature, therefore some portions of recycled alumina might be brittle-fractured. If fractured sand blasting particles are involved in the recycling media, it might result in irregular surfaces, as well as potential contamination. Using fractal dimension analysis [121–123], a sample plate surface was weekly analyzed in terms of topographic changes, as well as chemical analysis of sampled recycled Al2O3 particles. It was found that after accumulated use time exceeded 30 mins, the fractal dimension (DF) remained a constant value of about 1.4, prior to that it continuously increased from 1.25 to 1.4. By the electron probe microanalysis on collected blasting particles, unused Al2O3 contains 100% Al, whereas used (accumulated usage time was about 2,400 sec) particles contained Al (83.32 wt%), Ti (5.48), Ca (1.68), Ni (1.36), Mo (1.31), S (1.02), Si (0.65), P (0.55), Mn (0.49), K (0.29), Cl (0.26), and V (0.08), strongly indicating that used alumina powder was heavily contaminated, and a high risk for the next material surface to be contaminated. Such contaminants are from previously blasted materials having various chemical compositions, and investing materials as well [124].\nThere is evidence of surface contamination due to mechanical abrasive actions [125]. As a metallographic preparation, the surface needs to be mechanically polished with a metallographic paper (which is normally SiC-adhered paper) under running water [125]. It is worth mentioning here that polishing paper should be changed between different types of materials, and particularly when a dissimilar metal-couple is used for galvanic corrosion tests, such couple should not be polished prior to corrosion testing because both materials could become cross-contaminated. Hence, there are attempts to use TiO2 powder for blasting onto titanium material surfaces. It was reported that titanium surfaces were sand-blasted using TiO2 powder (particle size ranging from 45 μm, 45 μm-63 μm, and 63 μm-90 μm) to produce the different surface textures prior to fibroblast cell attachment [126].\nIn the rabbit tibia, CpTi implants, which were sand-blasted with 25 μm Al2O3 and TiO2 particles, were inserted in the rabbit tibia for 12 weeks [127]. Even though the amount of Al on the implant surface was higher than for the Al2O3-blasted implants compared to implants not blasted with Al2O3, any negative effects of the Al element were not detected [128], which is in contrast to those reported by Johansson et al. [127], who reported that Al release from Ti-6Al-4V implants was found to coincide with a poorer bone-to-implant over a three month period. It is possible that the lack of differences between TiO2-blasted and the Al2O3-blasted implants depends on lower surface concentrations of toxic Al ions than those reported by Johansson et al. [127]. Wang [129] investigated the effects of various surface modifications on porcelain bond strengths. Such modifications included Al2O3 blasting, TiO2 blasting, HNO3 + HF + H2O treatment, H2O2 treatment, and pre-oxidation in air at 600 °C for 10 min. Ti-porcelain couples were subjected to 3-point bending tests. It was concluded that TiO2 air abrasion showed the highest bond strength, which was significantly different from other surface treatments.\nRecently, it was reported that sand-blasting using alumina particle caused a remarkable distortion on a Co-Cr alloy and a noble alloy [130,131]. It was estimated that the stress causing the deflection exceeded the yield strength of tested materials. It was also suggested that the sand-blasting should be done using the lowest air pressure, duration of blasting period, and particle size alumina in order to minimize distortion of crowns and frameworks. To measure distortion, Co-Cr alloy plates (25 mm long, 5 mm wide, 0.7 mm thick) were sand-blasted with Al2O3 of 125 μm. Distortion was determined as the deflection of the plates as a distance of 20mm from the surface. It was reported that (i) the mean deflections varied between 0.37 mm and 1.72 mm, and (ii) deflection increased by an increase in duration of the blasting, pressure, particle size, and by a decrease in plate thickness [130]."}