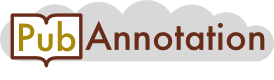
PMC:2871132 / 225010-229135
Annnotations
2_test
{"project":"2_test","denotations":[{"id":"20480036-16115681-52068988","span":{"begin":2632,"end":2635},"obj":"16115681"},{"id":"20480036-16115681-52068989","span":{"begin":3518,"end":3521},"obj":"16115681"},{"id":"T88139","span":{"begin":2632,"end":2635},"obj":"16115681"},{"id":"T37519","span":{"begin":3518,"end":3521},"obj":"16115681"}],"text":"5.5. Laser Applications\nAs mentioned before, laser technology and laser application have advanced remarkably. Lasers can be made to heat, melt, or vaporize materials, depending on laser power density [397,398]. Materials absorb power more readily from Nd:Yag laser beams (λ = 1.06 μm) than they do from CO2 laser beams (λ = 10.6μm). By heating materials, materials can be annealed, or solid state phase-transformation hardened. Using melting, materials can be alloyed, cladded, grain refined, amorphatized, and welded. Using vaporization, materials can be thin film deposited, cleaned, textured, and etched. Using shocking, materials can be shock hardened/peened [399]. Recent advances in the Nd:Yag and CO2 lasers have made possible a wide range of applications and emerging technologies in the computer, microelectronics, and materials fields. In the realm of materials processing, surface treatments and surface processing, surface treatments and surface modification for metals and semiconductors are of particular interest. With appropriate manipulation of the processing conditions (e.g., laser power density or interaction time), a single laser can be used to perform several processes [400,401].\nLaser alloying is a material-processing method that utilizes the high power density available from focused laser sources to melt metal coatings and a portion of the underlying substrate [402]. Since the melting occurs in a very short time and only at the surface, the bulk of the material remains cool, thus serving as an infinite heat sink. Large temperature gradients exist across the boundary between the melted surface region and the underlying solid substrate. This results in rapid self-quenching (1011 ks−1) and resolidification (velocities of 20 m/s). What makes laser surface alloying both attractive and interesting is the wide variety of chemical and microstructural states that can be retained because of the repaid quench from the liquid phase. The types of observed microstructures include extended solid solutions, metastable crystalline phases and metallic glasses as an amorphous metal [402,403]. Alloy production with a wide variety of elements, as well as a wide range of compositional content, can also be accomplished by a mechanical alloying or powder metallurgy, both of which do not involve liquids (in other words, in solid state fabrication).\nDirect laser forming (DLF) is a rapid prototyping technique that enables prompt modeling of metal parts with high bulk density on the base of individual three-dimensional data, including computer tomography models of anatomical structures. Hollander et al. [404] investigated DLFed Ti-6Al-4V for its applicability as hard tissue biomaterial. It was reported that rotating bending tests revealed that the fatigue profile of post-DLF annealed Ti-6Al-4 V was comparable to cast/hot isostatic pressed alloy. In an in vitro investigation, human osteoblasts were cultured on non-porous and porous blasted DLFed Ti-6Al-4V specimens to study morphology, vitality, proliferation and differentiation of the cells. It was reported that (i) the cells spread and proliferated on DLFed Ti-6Al-4V over a culture time of 14 days, (ii) on porous specimens, osteoblasts grew along the rims of the pores and formed circle-shaped structures, as visualized by live/dead staining, as well as scanning electron microscopy, and (iii) overall, the DLFed Ti-6Al-4V approach proved to be efficient, and could be further advanced in the field of hard tissue biomaterials [404].\nRecently, the femtosecond-laser-based tooth preparation technique has been developed [405,406]. Any one of the existing laser technologies using a CO2 laser, Er:Yag laser, Ho:Yag laser, excimer laser, frequency-doubled Alexandrite laser, superpulsed CO2 laser, or picosecond Nd:Yag laser induce severe thermal adverse effects or do not supply sufficient ablation rates for completion of the mechanical drill [407]. Using the femtosecond laser technology for micromachining was successfully developed, for example in machining tools for repairing photolithographic masks or fuel injector nozzles [408]."}
NEUROSES
{"project":"NEUROSES","denotations":[{"id":"T4780","span":{"begin":1108,"end":1115},"obj":"PATO_0001019"},{"id":"T4781","span":{"begin":1281,"end":1288},"obj":"PATO_0001019"},{"id":"T4782","span":{"begin":304,"end":307},"obj":"CHEBI_84390"},{"id":"T4783","span":{"begin":705,"end":708},"obj":"CHEBI_84390"},{"id":"T4784","span":{"begin":304,"end":307},"obj":"CHEBI_29325"},{"id":"T4785","span":{"begin":705,"end":708},"obj":"CHEBI_29325"},{"id":"T4786","span":{"begin":304,"end":307},"obj":"CHEBI_84377"},{"id":"T4787","span":{"begin":705,"end":708},"obj":"CHEBI_84377"},{"id":"T4788","span":{"begin":304,"end":307},"obj":"CHEBI_16526"},{"id":"T4789","span":{"begin":705,"end":708},"obj":"CHEBI_16526"},{"id":"T4790","span":{"begin":304,"end":307},"obj":"CHEBI_18245"},{"id":"T4791","span":{"begin":705,"end":708},"obj":"CHEBI_18245"},{"id":"T4792","span":{"begin":304,"end":307},"obj":"CHEBI_82680"},{"id":"T4793","span":{"begin":705,"end":708},"obj":"CHEBI_82680"},{"id":"T4794","span":{"begin":386,"end":391},"obj":"PATO_0001736"},{"id":"T4795","span":{"begin":398,"end":403},"obj":"PATO_0000083"},{"id":"T4796","span":{"begin":671,"end":677},"obj":"PATO_0001484"},{"id":"T4797","span":{"begin":737,"end":741},"obj":"PATO_0000600"},{"id":"T4798","span":{"begin":976,"end":982},"obj":"CHEBI_33521"},{"id":"T4799","span":{"begin":1334,"end":1339},"obj":"CHEBI_33521"},{"id":"T4800","span":{"begin":1131,"end":1135},"obj":"PATO_0001309"},{"id":"T4801","span":{"begin":1439,"end":1443},"obj":"PATO_0001309"},{"id":"T4802","span":{"begin":1131,"end":1135},"obj":"PATO_0000165"},{"id":"T4803","span":{"begin":1439,"end":1443},"obj":"PATO_0000165"},{"id":"T4804","span":{"begin":1270,"end":1274},"obj":"PATO_0000469"},{"id":"T4805","span":{"begin":1304,"end":1311},"obj":"PATO_0001517"},{"id":"T4806","span":{"begin":1433,"end":1438},"obj":"PATO_0000569"},{"id":"T4807","span":{"begin":1433,"end":1438},"obj":"PATO_0000574"},{"id":"T4808","span":{"begin":1547,"end":1552},"obj":"PATO_0000586"},{"id":"T4809","span":{"begin":1553,"end":1564},"obj":"PATO_0000146"},{"id":"T4810","span":{"begin":1654,"end":1659},"obj":"PATO_0001736"},{"id":"T4811","span":{"begin":2018,"end":2023},"obj":"PATO_0001736"},{"id":"T4812","span":{"begin":2348,"end":2353},"obj":"PATO_0001736"},{"id":"T4813","span":{"begin":1838,"end":1842},"obj":"PATO_0000600"},{"id":"T4814","span":{"begin":2143,"end":2147},"obj":"PATO_0000600"},{"id":"T4815","span":{"begin":2182,"end":2186},"obj":"PATO_0000600"},{"id":"T4816","span":{"begin":1949,"end":1955},"obj":"PATO_0001735"},{"id":"T4817","span":{"begin":1956,"end":1961},"obj":"PATO_0000083"},{"id":"T4818","span":{"begin":2092,"end":2101},"obj":"PATO_0001332"},{"id":"T4819","span":{"begin":2102,"end":2107},"obj":"CHEBI_33521"},{"id":"T4820","span":{"begin":2466,"end":2471},"obj":"CHEBI_33521"},{"id":"T4821","span":{"begin":2159,"end":2167},"obj":"CHEBI_33250"},{"id":"T4822","span":{"begin":2210,"end":2217},"obj":"PATO_0000025"},{"id":"T4823","span":{"begin":2483,"end":2487},"obj":"PATO_0000469"},{"id":"T4824","span":{"begin":2493,"end":2500},"obj":"PATO_0001019"},{"id":"T4825","span":{"begin":2508,"end":2512},"obj":"CHEBI_18282"},{"id":"T4826","span":{"begin":2508,"end":2512},"obj":"CHEBI_22695"},{"id":"T4827","span":{"begin":2691,"end":2695},"obj":"PATO_0000386"},{"id":"T4828","span":{"begin":2849,"end":2852},"obj":"PATO_0001305"},{"id":"T4829","span":{"begin":2943,"end":2953},"obj":"PATO_0000985"},{"id":"T4830","span":{"begin":2958,"end":2964},"obj":"PATO_0000982"},{"id":"T4831","span":{"begin":2958,"end":2964},"obj":"PATO_0000984"},{"id":"T4832","span":{"begin":3008,"end":3018},"obj":"PATO_0000051"},{"id":"T4833","span":{"begin":3171,"end":3175},"obj":"PATO_0001309"},{"id":"T4834","span":{"begin":3171,"end":3175},"obj":"PATO_0000165"},{"id":"T4835","span":{"begin":3196,"end":3202},"obj":"PATO_0000984"},{"id":"T4836","span":{"begin":3196,"end":3202},"obj":"PATO_0000982"},{"id":"T4837","span":{"begin":3318,"end":3322},"obj":"PATO_0001422"},{"id":"T4838","span":{"begin":3353,"end":3361},"obj":"CHEBI_10545"},{"id":"T4839","span":{"begin":3435,"end":3444},"obj":"PATO_0001678"},{"id":"T4840","span":{"begin":3467,"end":3475},"obj":"PATO_0000694"},{"id":"T4841","span":{"begin":3492,"end":3496},"obj":"PATO_0000386"},{"id":"T4842","span":{"begin":3671,"end":3674},"obj":"CHEBI_29325"},{"id":"T4843","span":{"begin":3774,"end":3777},"obj":"CHEBI_29325"},{"id":"T4844","span":{"begin":3671,"end":3674},"obj":"CHEBI_84390"},{"id":"T4845","span":{"begin":3774,"end":3777},"obj":"CHEBI_84390"},{"id":"T4846","span":{"begin":3671,"end":3674},"obj":"CHEBI_84377"},{"id":"T4847","span":{"begin":3774,"end":3777},"obj":"CHEBI_84377"},{"id":"T4848","span":{"begin":3671,"end":3674},"obj":"CHEBI_18245"},{"id":"T4849","span":{"begin":3774,"end":3777},"obj":"CHEBI_18245"},{"id":"T4850","span":{"begin":3671,"end":3674},"obj":"CHEBI_82680"},{"id":"T4851","span":{"begin":3774,"end":3777},"obj":"CHEBI_82680"},{"id":"T4852","span":{"begin":3671,"end":3674},"obj":"CHEBI_16526"},{"id":"T4853","span":{"begin":3774,"end":3777},"obj":"CHEBI_16526"},{"id":"T4854","span":{"begin":3725,"end":3734},"obj":"PATO_0000044"},{"id":"T4855","span":{"begin":3735,"end":3742},"obj":"PATO_0001473"},{"id":"T4856","span":{"begin":3867,"end":3877},"obj":"PATO_0001627"},{"id":"T4857","span":{"begin":4097,"end":4101},"obj":"CHEBI_33292"},{"id":"T4773","span":{"begin":73,"end":84},"obj":"CHEBI_33232"},{"id":"T4774","span":{"begin":90,"end":98},"obj":"PATO_0000694"},{"id":"T4775","span":{"begin":187,"end":192},"obj":"PATO_0001024"},{"id":"T4776","span":{"begin":229,"end":234},"obj":"PATO_0001024"},{"id":"T4777","span":{"begin":1102,"end":1107},"obj":"PATO_0001024"},{"id":"T4778","span":{"begin":1275,"end":1280},"obj":"PATO_0001024"},{"id":"T4779","span":{"begin":193,"end":200},"obj":"PATO_0001019"}],"text":"5.5. Laser Applications\nAs mentioned before, laser technology and laser application have advanced remarkably. Lasers can be made to heat, melt, or vaporize materials, depending on laser power density [397,398]. Materials absorb power more readily from Nd:Yag laser beams (λ = 1.06 μm) than they do from CO2 laser beams (λ = 10.6μm). By heating materials, materials can be annealed, or solid state phase-transformation hardened. Using melting, materials can be alloyed, cladded, grain refined, amorphatized, and welded. Using vaporization, materials can be thin film deposited, cleaned, textured, and etched. Using shocking, materials can be shock hardened/peened [399]. Recent advances in the Nd:Yag and CO2 lasers have made possible a wide range of applications and emerging technologies in the computer, microelectronics, and materials fields. In the realm of materials processing, surface treatments and surface processing, surface treatments and surface modification for metals and semiconductors are of particular interest. With appropriate manipulation of the processing conditions (e.g., laser power density or interaction time), a single laser can be used to perform several processes [400,401].\nLaser alloying is a material-processing method that utilizes the high power density available from focused laser sources to melt metal coatings and a portion of the underlying substrate [402]. Since the melting occurs in a very short time and only at the surface, the bulk of the material remains cool, thus serving as an infinite heat sink. Large temperature gradients exist across the boundary between the melted surface region and the underlying solid substrate. This results in rapid self-quenching (1011 ks−1) and resolidification (velocities of 20 m/s). What makes laser surface alloying both attractive and interesting is the wide variety of chemical and microstructural states that can be retained because of the repaid quench from the liquid phase. The types of observed microstructures include extended solid solutions, metastable crystalline phases and metallic glasses as an amorphous metal [402,403]. Alloy production with a wide variety of elements, as well as a wide range of compositional content, can also be accomplished by a mechanical alloying or powder metallurgy, both of which do not involve liquids (in other words, in solid state fabrication).\nDirect laser forming (DLF) is a rapid prototyping technique that enables prompt modeling of metal parts with high bulk density on the base of individual three-dimensional data, including computer tomography models of anatomical structures. Hollander et al. [404] investigated DLFed Ti-6Al-4V for its applicability as hard tissue biomaterial. It was reported that rotating bending tests revealed that the fatigue profile of post-DLF annealed Ti-6Al-4 V was comparable to cast/hot isostatic pressed alloy. In an in vitro investigation, human osteoblasts were cultured on non-porous and porous blasted DLFed Ti-6Al-4V specimens to study morphology, vitality, proliferation and differentiation of the cells. It was reported that (i) the cells spread and proliferated on DLFed Ti-6Al-4V over a culture time of 14 days, (ii) on porous specimens, osteoblasts grew along the rims of the pores and formed circle-shaped structures, as visualized by live/dead staining, as well as scanning electron microscopy, and (iii) overall, the DLFed Ti-6Al-4V approach proved to be efficient, and could be further advanced in the field of hard tissue biomaterials [404].\nRecently, the femtosecond-laser-based tooth preparation technique has been developed [405,406]. Any one of the existing laser technologies using a CO2 laser, Er:Yag laser, Ho:Yag laser, excimer laser, frequency-doubled Alexandrite laser, superpulsed CO2 laser, or picosecond Nd:Yag laser induce severe thermal adverse effects or do not supply sufficient ablation rates for completion of the mechanical drill [407]. Using the femtosecond laser technology for micromachining was successfully developed, for example in machining tools for repairing photolithographic masks or fuel injector nozzles [408]."}