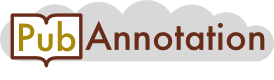
PMC:2871132 / 206658-209676
Annnotations
2_test
{"project":"2_test","denotations":[{"id":"20480036-12322975-52068964","span":{"begin":2440,"end":2443},"obj":"12322975"},{"id":"20480036-12322975-52068965","span":{"begin":3013,"end":3016},"obj":"12322975"},{"id":"T49026","span":{"begin":2440,"end":2443},"obj":"12322975"},{"id":"T64756","span":{"begin":3013,"end":3016},"obj":"12322975"}],"text":"5.2. Gradient Functional Material System\nMaterial is composed of multilayer, with each layer having unique characteristics, yet adjacent layers having some similarity is called gradient functional material (GFM). Although such functions can include various properties, it is limited to mechanical, physical, or thermal properties since other properties, such as chemical or electrochemical, are more likely important to the surface layer, and not related to bulky or semi-bulky behavior. For example, if hydroxyapatite is needed to spray-coat onto CpTi, this GFM concept can be applied. Instead of applying HA powder directly onto the CpTi surface, a multilayer of the following sequence: HA/HA + Al2O3/Al2O3 + TiO2/TiO2/CpTi can be prepared to enhance the bonding strength. From the HA side to CpTi side, the mechanical properties (particularly, modulus of elasticity) and thermal properties (such as linear coefficient of thermal expansion) are gradually changing, so that when this HA-coated CpTi is subjected to stressing, interfacial stress between each constituent layer can be minimized, resulting in that the degree of discreteness in the stress field can also be minimized.\nA novel technology for forming a gradient functional titanium-oxide film on a titanium alloy (Ti-6Al-4V) was developed by the reactive DC sputtering vapor deposition method [371]. The method was developed for fabricating denture bases and implants, and the oxygen concentration was changed continuously during sputtering to provide a gradient in the film composition, by which adhesivity to the alloy, surface hardness, and biocompatibility was improved. Denture bases produced by superplastic forming (SPF) are cleaned with an organic solvent, the oxygen concentration is changed continuously during sputtering, and pure titanium is vapor-deposited by the reactive DC sputtering. In the initial stage, intermetallic bonding is achieved by oxygen-free vapor deposition, so the adhesion is excellent and there is no fear of exfoliation. But farther away from the metal surface, the oxygen concentration is raised gradually to form a gradient film. At the surface some titanium oxides are formed. Titanium oxide features excellent biocompatibility, and since it is a hard material, resists damage. The overall film thickness in the experimental was 3 μm, and the Vickers hardness of the surface was 1,500 (200–300 for pure titanium) [371].\nBogdanski et al. [372] fabricated the functionally graded material, which was prepared through powder metallurgical processing with thoroughly mixed powders of the elements. Ten mixtures were prepared ranging from Ni:Ti of 90:10 (by atomic %) through 80:20, to Ni:Ti of 10:90, and pure Ti (0:100). The compaction was done by hot isostatic pressing (HIP) at 1,050 °C and 195 MPa for 5 h. It was reported that, using cells (comprised of osteoblast-like osteosarcoma cells, primary human osteoblasts, and murine fibroblasts), good biocompatibility of Ni-Ti alloys has shown up to about Ni 50% [372]."}